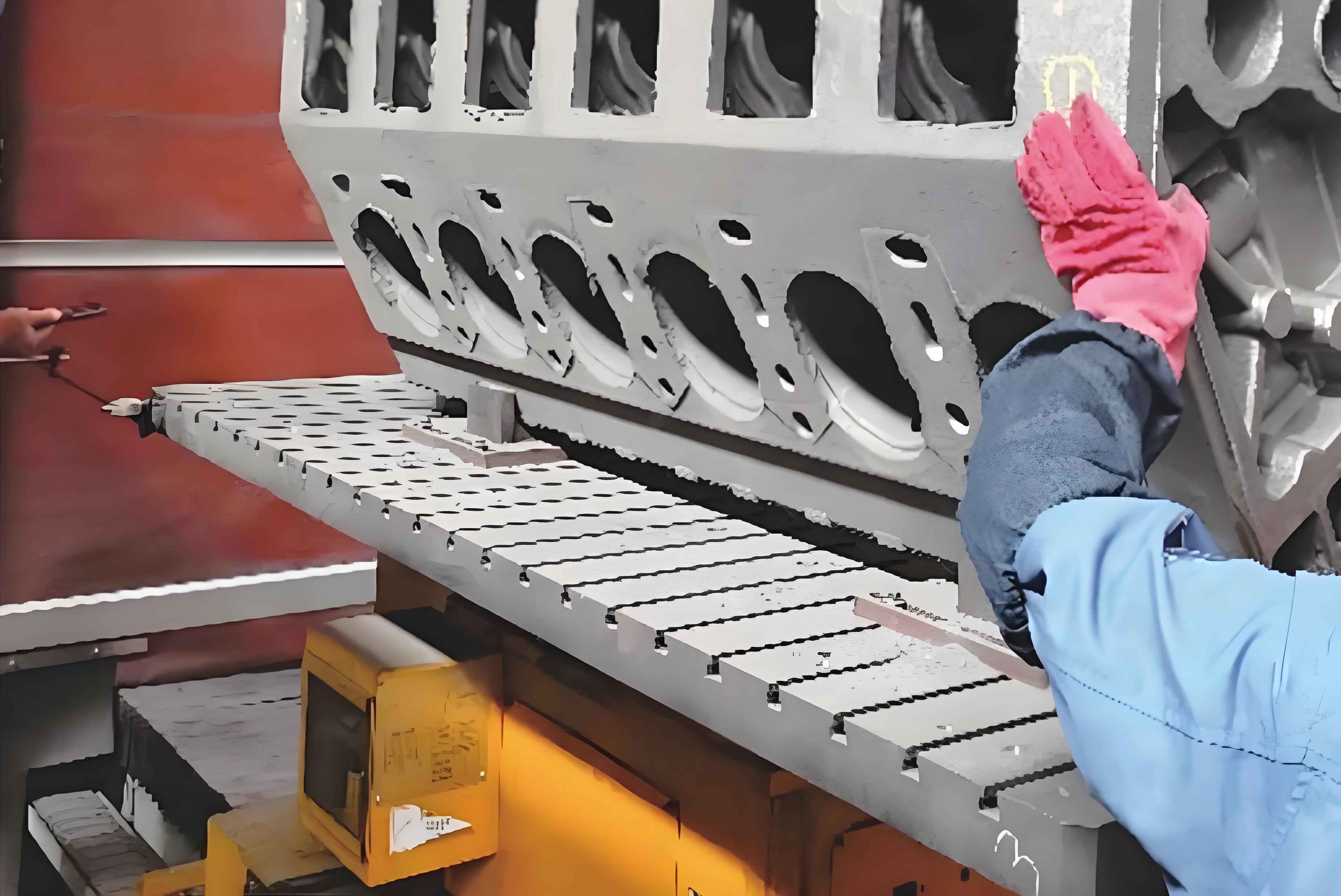
Our company has achieved breakthrough progress in engine cylinder block cleaning through comprehensive automation process innovation. This article systematically presents the technical solutions addressing challenges in environmental conditions, labor intensity, and quality consistency during engine cylinder block post-casting treatment.
1. Process Characteristics and Challenges
The modern engine cylinder block exhibits complex structural features including:
$$ V_{complexity} = \int_{0}^{T} (S_{surface} + C_{cavity}) dt $$
Where $S_{surface}$ represents surface complexity factors and $C_{cavity}$ denotes internal cavity complexity parameters. Typical parameters for heavy-duty engine cylinder blocks include:
Parameter | Value Range | Unit |
---|---|---|
Minimum Wall Thickness | 4-5.5 | mm |
Cast Weight | 270-400 | kg |
Surface Tension | RT450 | – |
2. Automated Material Handling System
The core algorithm for robotic grasping position determination in engine cylinder block handling:
$$ P_{grasp} = \arg\min_{p \in \Omega} \left( \sum_{i=1}^{n} w_i \cdot d(p,c_i) \right) $$
Where $w_i$ represents weight coefficients for different grasping constraints and $d(p,c_i)$ denotes distance functions to critical features.
Process Stage | Traditional Method | Automated Solution |
---|---|---|
Workpiece Transfer | Manual hoisting (3-5 min/pc) | Robotic handling (45-60 sec/pc) |
Positioning Accuracy | ±15 mm | ±0.5 mm |
3. Intelligent Grinding System
The adaptive grinding force control model for engine cylinder block surface treatment:
$$ F_{grind} = k \cdot \left( \frac{\partial E}{\partial t} \right) + \mu \cdot v^{1.2} $$
Where $k$ represents material removal coefficient and $\mu$ denotes dynamic friction factor.
Grinding Parameter | Value | Unit |
---|---|---|
Spindle Speed | 8,000-15,000 | rpm |
Feed Rate | 0.5-2.0 | m/min |
4. Internal Cavity Cleaning Technology
The shot peening energy distribution model for engine cylinder block internal passages:
$$ E_{peen} = \frac{1}{2} m_p v_p^2 \cdot \eta \cdot \left(1 – e^{-\lambda L}\right) $$
Where $m_p$ = media mass, $v_p$ = projection velocity, and $\lambda$ = attenuation coefficient.
Process Parameter | Value | Unit |
---|---|---|
Nozzle Pressure | 0.5-0.8 | MPa |
Media Size | Φ0.6-1.0 | mm |
5. System Integration and Optimization
The production line efficiency optimization model for engine cylinder block cleaning:
$$ \eta_{system} = \prod_{i=1}^{n} \eta_i \cdot \left(1 – \frac{t_{transfer}}{\sum t_{process}}\right) $$
Where $\eta_i$ represents individual station efficiency and $t_{transfer}$ denotes material handling time.
Performance Metric | Before Automation | After Automation |
---|---|---|
Cycle Time | 120 min | 45 min |
Rejection Rate | 2.8% | 0.5% |
This comprehensive automation solution for engine cylinder block cleaning demonstrates significant improvements in production efficiency, quality consistency, and operational safety, establishing new industry benchmarks for heavy-duty engine component manufacturing.