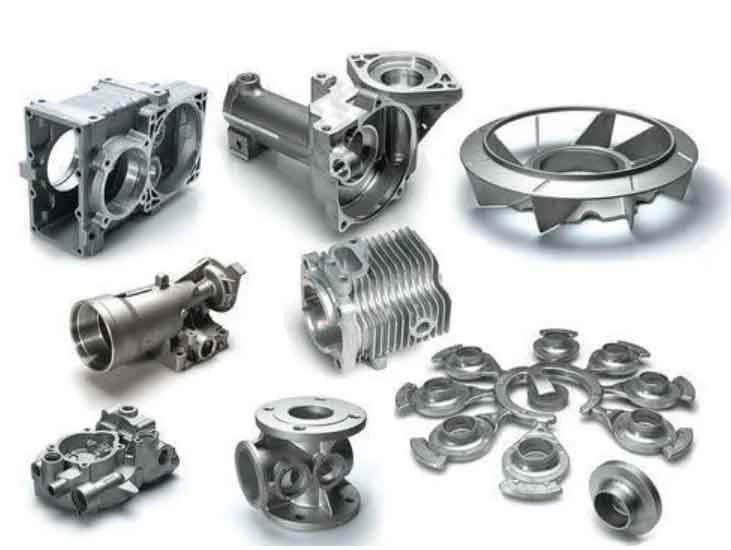
Grey cast iron, like any other casting material, is susceptible to various defects that can impact the quality and performance of castings. Understanding these common defects, their causes, and implementing preventive measures is crucial for ensuring the production of high-quality grey cast iron components. Here are some common defects, along with prevention and remediation techniques:
1. Porosity:
- Description: Porosity refers to the presence of voids or gas pockets in the casting, which can weaken the material and reduce its density.
- Causes: Porosity can result from the entrapment of gases during the casting process, inadequate gating and risering design, or improper pouring techniques.
- Prevention and Remediation: Use proper gating and risering systems to facilitate proper molten metal flow and gas escape. Control pouring temperature and ensure adequate venting.
2. Shrinkage Defects:
- Description: Shrinkage defects occur when the casting cools and solidifies, resulting in internal voids or shrinkage cavities.
- Causes: Inadequate risering, improper cooling rate, or insufficient feed metal can cause shrinkage defects.
- Prevention and Remediation: Ensure proper risering design to allow for sufficient feed metal to compensate for shrinkage. Optimize cooling rates and gating design to minimize thermal gradients.
3. Inclusions:
- Description: Inclusions are non-metallic particles or foreign materials embedded in the casting, which can weaken the material and lead to failure.
- Causes: Inclusions may originate from contaminated melt or improperly cleaned mold cavity surfaces.
- Prevention and Remediation: Use clean and high-quality materials, ensure proper melt treatment, and maintain clean mold surfaces to prevent inclusions.
4. Cold Shut:
- Description: Cold shut is a defect where two portions of the casting fail to fuse completely during solidification, leaving a visible line or seam.
- Causes: Cold shut occurs due to inadequate gating design or improper pouring techniques.
- Prevention and Remediation: Optimize gating design and pouring techniques to ensure complete fusion of molten metal during solidification.
5. Misruns and Runouts:
- Description: Misruns and runouts occur when the molten metal fails to fill the entire mold cavity, resulting in incomplete castings.
- Causes: Insufficient pouring temperature, inadequate gating, or clogged channels can lead to misruns and runouts.
- Prevention and Remediation: Maintain proper pouring temperature, design an appropriate gating system, and ensure proper channel cleanliness.
6. Hot Tears and Cracks:
- Description: Hot tears and cracks are defects caused by tensile stresses during solidification, leading to localized cracking or tearing of the casting.
- Causes: Improper cooling, inadequate risering, or high levels of sulfur and phosphorus can contribute to hot tears and cracks.
- Prevention and Remediation: Optimize cooling rates, use proper risering to counteract tensile stresses, and control alloy composition to minimize sulfur and phosphorus content.
Preventing and remedying these common defects requires a combination of proper process control, design optimization, and material management. Grey cast iron foundries should implement rigorous quality control measures, conduct regular inspections, and continuously improve their processes to minimize defects and ensure the production of high-quality castings. Additionally, utilizing advanced simulation and modeling software can aid in identifying potential defects before actual casting, enabling proactive defect prevention.