Investment casting, also known as lost-wax casting, is a multi-step process used to create complex metal components with high precision and intricate details. Here is a step-by-step guide to the investment casting process:
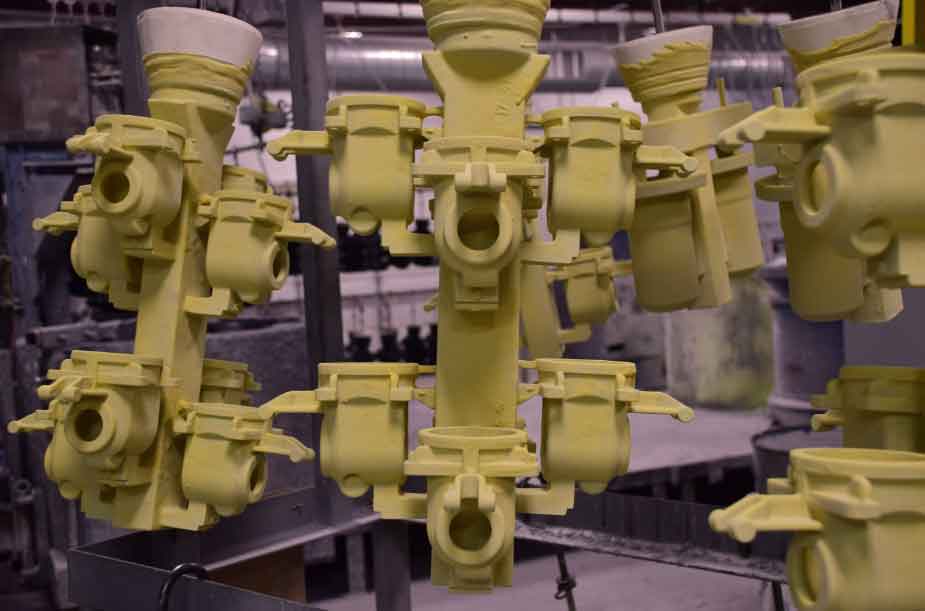
1. Pattern Creation:
The process begins with the creation of a pattern, which can be made from wax, plastic, or other materials. The pattern is an exact replica of the desired final component. It can be produced using various techniques such as injection molding, 3D printing, or hand carving.
2. Pattern Assembly:
Multiple patterns, often called wax patterns, are attached to a central wax sprue, forming a cluster. The sprue serves as a channel for the molten metal to flow into the mold cavity.
3. Investment (Mold) Preparation:
The cluster of patterns is then coated with a ceramic slurry. This slurry adheres to the patterns and forms a ceramic shell around them. The shell helps maintain the shape of the patterns during the casting process.
4. Dewaxing (Pattern Removal):
Once the ceramic shell is dry, it is heated to remove the wax or other pattern material, leaving behind a cavity in the shape of the desired component. This step is called dewaxing and can be done through various methods, including autoclaving, steam dewaxing, or thermal burnout.
5. Preheating:
The ceramic shell is preheated to a specific temperature to prepare it for the molten metal. Preheating helps to minimize thermal shock when the hot metal is poured into the mold.
6. Metal Pouring:
The preheated ceramic shell is placed in a casting flask, and the flask is filled with a molten metal or alloy of the desired material. The metal is poured into the mold cavity through the sprue and flows through the channels and gates to fill the entire mold.
7. Solidification and Cooling:
The poured metal fills the mold cavity and solidifies as it cools. The solidification time depends on the type of metal and component geometry. Cooling can be accelerated using controlled cooling methods such as water or air quenching.
8. Shell Removal:
Once the metal has solidified and cooled, the ceramic shell is removed. This can be done by mechanically breaking the shell or by using chemicals to dissolve it. The result is the raw casting, which requires further finishing and cleaning.
9. Finishing Operations:
The raw casting undergoes various finishing operations to remove any remaining gating system components, such as sprues and risers. Additional processes like grinding, machining, polishing, and heat treatment may be performed to achieve the desired final dimensions, surface finish, and mechanical properties.
10. Inspection and Quality Control:
The finished casting undergoes thorough inspection and quality control to ensure it meets the required specifications and standards. This may involve dimensional inspection, visual inspection, non-destructive testing, and material analysis.
11. Finalizing the Component:
After passing the inspection, the component is ready for any additional surface treatments, such as coating, painting, or plating, if necessary. It is then prepared for assembly or integration into the final product.
Investment casting enables the production of complex and precise metal components with intricate details. The process offers design flexibility, excellent dimensional accuracy, and a wide range of material options, making it suitable for various industries such as aerospace, automotive, medical, and more.