Investment casting, also known as precision casting or lost-wax casting, is a manufacturing process that is widely used in the aerospace and defense industries to create complex and high-performance components. It involves creating a wax pattern of the desired part, coating it with ceramic to form a mold, and then melting the wax to leave a cavity. The molten metal is then poured into the mold, solidifies, and the ceramic shell is removed to reveal the final part.
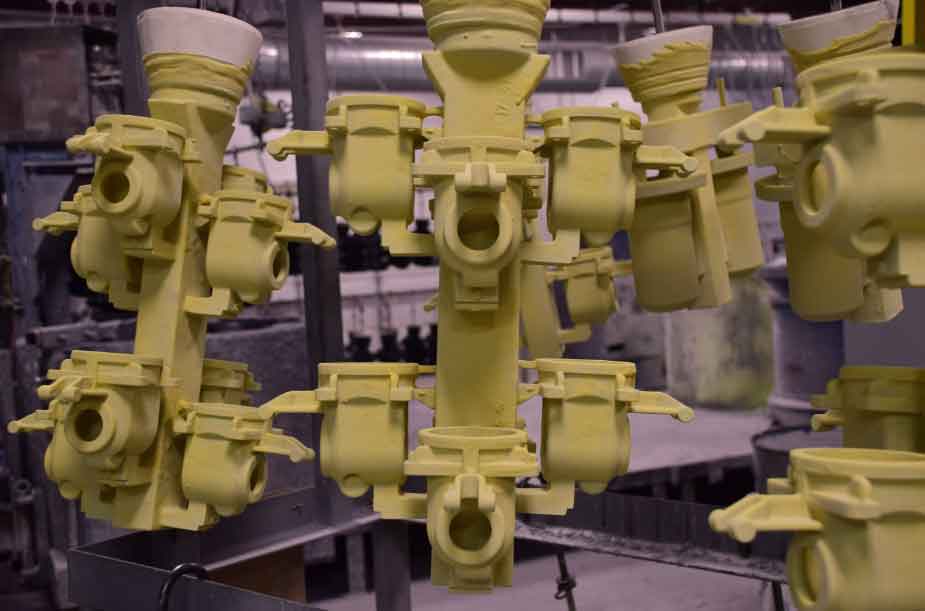
In the aerospace and defense sectors, investment casting offers several advantages that make it a preferred choice for producing critical components:
- Complex Geometries: Investment casting enables the production of parts with intricate shapes, including thin-walled sections, undercuts, and internal features. This allows designers to create components optimized for performance, such as turbine blades, engine components, and airframe parts, with minimal machining or assembly requirements.
- High Precision: Investment casting offers excellent dimensional accuracy and repeatability, leading to tight tolerances and precise parts. This is crucial in aerospace and defense applications where strict specifications must be met to ensure optimal performance, reliability, and safety.
- Material Versatility: Investment casting supports a wide range of materials, including superalloys, stainless steels, titanium, and aluminum. These materials possess superior mechanical properties, heat resistance, and corrosion resistance, making them suitable for demanding aerospace and defense environments.
- Weight Reduction: The ability to produce complex shapes and thin-walled sections allows for weight reduction in components, which is critical in aerospace applications where every kilogram saved can contribute to fuel efficiency, payload capacity, and overall performance.
- Enhanced Performance: Investment casting enables the creation of parts with excellent surface finishes, reducing aerodynamic drag and improving overall performance. Additionally, the process provides greater control over the material microstructure, resulting in improved mechanical properties, such as high tensile strength, fatigue resistance, and temperature resistance.
- Cost Efficiency: While investment casting can involve higher upfront costs compared to other manufacturing processes, it offers long-term cost benefits. The reduced need for machining, assembly, and material waste, combined with the ability to produce complex parts in a single operation, can lead to overall cost savings in the production of aerospace and defense components.
- Rapid Prototyping: Investment casting allows for the relatively quick production of prototypes and small batch sizes, facilitating iterative design improvements and reducing time-to-market for new aerospace and defense systems.
- Supply Chain Optimization: Investment casting can simplify the supply chain by eliminating the need for multiple component assemblies, reducing inventory, and streamlining production processes. This can result in improved logistics, reduced lead times, and enhanced overall efficiency.
In summary, investment casting plays a vital role in pushing the limits of performance in aerospace and defense industries. Its ability to produce complex geometries, high precision, and superior mechanical properties make it a valuable manufacturing technique for critical components, contributing to the advancement of aerospace and defense systems.