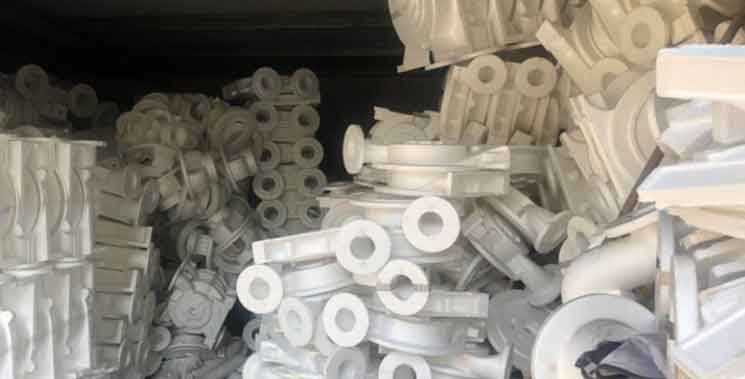
Investment casting, also known as precision casting or lost wax casting, plays a crucial role in meeting the medical industry’s demand for precision, reliability, and high-quality components. From surgical instruments to orthopedic implants, investment casting offers several benefits that make it well-suited for medical device manufacturing. Here’s how investment casting meets the unique requirements of the medical industry:
- Precision and Dimensional Accuracy: Investment casting enables the production of medical components with exceptional precision and dimensional accuracy. The process allows for the replication of intricate details and complex geometries, ensuring that the final components meet tight tolerances and precise specifications. This level of precision is critical for medical devices that require precise fit, alignment, and performance.
- High-Quality Surface Finish: Investment casting provides a smooth and high-quality surface finish, which is essential for medical devices that come into direct contact with patients’ bodies. The fine surface finish minimizes the risk of friction, irritation, or tissue damage, enhancing patient comfort and safety.
- Material Selection: Investment casting accommodates a wide range of materials suitable for medical applications, including stainless steel, titanium, cobalt-chromium alloys, and other biocompatible materials. These materials offer excellent corrosion resistance, mechanical properties, and compatibility with the human body. Medical device manufacturers can select the most appropriate material based on the specific application and requirements.
- Complex and Intricate Designs: Investment casting enables the production of medical components with intricate and complex designs. This allows for the creation of features such as fine threads, delicate patterns, and internal channels, which are essential for medical devices like surgical instruments and implantable devices.
- Single-Piece Construction and Integration: Investment casting allows for the production of medical components as a single piece, eliminating the need for multiple components and assembly processes. This reduces the risk of component failure at joints or interfaces, enhances structural integrity, and simplifies the manufacturing and sterilization processes.
- Consistency and Reliability: Investment casting offers high repeatability and consistency in the manufacturing process. Each casting replicates the original pattern precisely, ensuring consistent quality and performance across multiple components. This reliability is vital for medical devices that require consistent performance and compatibility.
- Customization and Tailored Solutions: Investment casting provides the flexibility to customize and tailor medical components to specific patient needs. Implants, for example, can be produced in various sizes and shapes to accommodate individual patient anatomy. This level of customization enhances patient outcomes and contributes to the overall success of medical treatments.
- Regulatory Compliance: Investment casting is well-established and widely accepted in the medical industry. Manufacturers using investment casting for medical devices follow stringent quality control measures and adhere to regulatory standards, such as ISO 13485 and FDA guidelines. This ensures that the produced components meet the required quality, safety, and reliability standards.
Investment casting plays a vital role in meeting the medical industry’s demand for precise, reliable, and high-quality components. Its ability to produce intricate designs, provide customization options, and offer a wide range of material choices makes it an invaluable process in the manufacturing of medical devices. Investment casting continues to drive innovation and contribute to advancements in medical technology, improving patient care and outcomes.