Titanium alloy has the characteristics of low density, high specific strength, good corrosion resistance, low thermal conductivity, low linear expansion coefficient, non-toxic and non-magnetic. It is a light and high-strength corrosion resistant material, which is widely used in aviation, aerospace, shipbuilding, petrochemical and other fields. The higher production cost is the obstacle to its further expansion of application, while the casting and molding technology with or without allowance can minimize the material loss, which is one of the main ways to reduce its manufacturing cost.
As a near-net forming technology, investment casting is particularly suitable for parts that cannot be directly processed and welded due to their complex shape; Or structural parts that can be processed and welded, but are economically unbearable due to high production costs. The investment casting process of the impeller casting of a certain type of complex curved blade is designed. The wax scale and the reverse deformation process correction amount are set in sections to ensure that the shell size matches the process design size. The top pouring and the dispersed introduction of the inner runner are adopted to realize the smooth filling, and the castings with high internal quality, surface quality and dimensional accuracy are successfully produced, realizing the overall casting forming of the products. Compared with the original profile processing and manufacturing method, it not only greatly reduces the manufacturing cost, but also greatly reduces its production cycle.
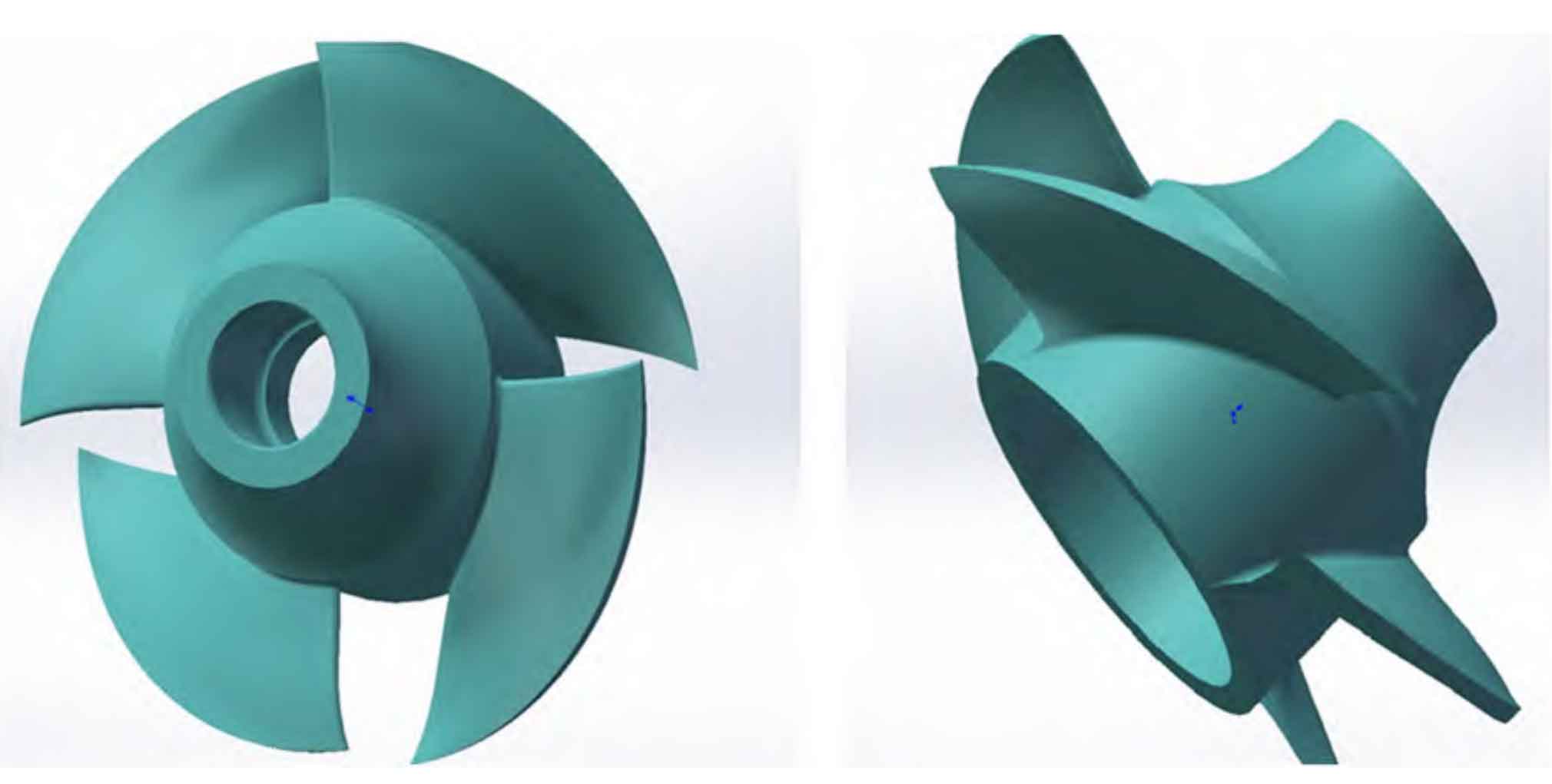
The titanium alloy curved impeller casting is shown in the figure, and its overall dimension is φ 490 mm × 290 mm, mass 39 kg, center hub (small end φ 116 mm/large end φ 186 mm × 290 mm). The blade surface shape is complex, and the flow line shape is irregular and variable cross-section structure. The thinnest part of the wall thickness is only 3.8 mm, the minimum radius of the edge is R1.5 mm, and the material is ZTC4 titanium alloy.
(1) Through wax pattern design and setting of reverse deformation correction, the dimensional accuracy of the model is controlled to ensure the correct shape of the flow line of the impeller with complex curved surface.
(2) The casting mode of vertical top casting+annular gating riser is adopted to achieve stable mold filling and sequential solidification. By opening five internal gates, the floating speed of the alloy liquid is accelerated, and the impurities and gases in the molten metal are rapidly concentrated in the riser, so as to obtain castings with excellent internal quality.
(3) For this type of complex curved impeller casting, investment casting process is adopted to achieve integral casting and forming, and products with high internal quality, surface quality, good dimensional accuracy and surface finish are obtained.
(4) When the vacuum consumable electrode arc shell melting furnace is used for melting, the melting current is maintained at 28~36 kA, the melting voltage is controlled at 34~41 V, the melting vacuum is stabilized at 3.0~5.0 Pa, and the return water temperature of the crucible is not greater than 45 ℃.
The casting is classified as Class III and the quality grade is Class C, and X-ray flaw detection is required. Its internal metallurgical quality meets GJB2896A-2007 Class C requirements; The surface is subject to dye penetrant inspection, and its surface quality meets the requirements of GJB2896A-2007C, and the surface roughness is 6.3 μ m; The dimensional tolerance grade shall comply with the requirements of GB/T 6414-1999CT9.