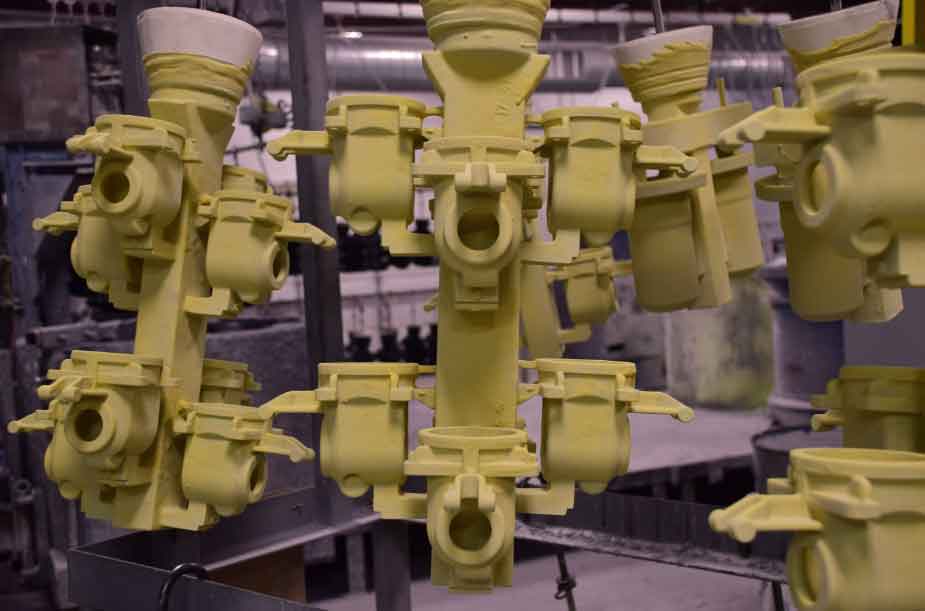
Investment casting, also known as lost-wax casting, has revolutionized the production of turbine components in the aerospace, power generation, and industrial sectors. Here’s how investment casting contributes to the production of turbine components and drives innovation in this field:
1. Complex Geometry:
Investment casting enables the production of turbine components with complex geometries, including intricate cooling passages, thin walls, and intricate shapes. This capability is crucial for turbine blades, vanes, and other critical components that require optimal aerodynamics and efficient heat transfer.
2. High-Temperature Alloys:
Investment casting supports the use of high-temperature alloys such as nickel-based superalloys, cobalt-based alloys, and titanium alloys. These alloys exhibit excellent strength, creep resistance, and corrosion resistance at high temperatures, making them ideal for turbine applications. Investment casting ensures the precise casting of these alloys to achieve the required mechanical properties and performance in extreme operating conditions.
3. Near-Net Shape Manufacturing:
Investment casting produces turbine components that are close to the final desired shape, reducing the need for extensive machining. This near-net shape manufacturing approach minimizes material waste, machining time, and costs associated with additional operations. It also allows for the production of complex, near-finished components with intricate internal features, optimizing component performance and reducing post-casting processing.
4. Cooling Channel Design:
Turbine components, especially blades and vanes, require efficient cooling to withstand high temperatures. Investment casting enables the integration of intricate cooling channels directly into the component design. This design freedom allows for precise control over cooling air flow, leading to improved component durability, thermal efficiency, and overall turbine performance.
5. Design Optimization for Efficiency:
Investment casting allows for design optimization to enhance the efficiency of turbine components. Engineers can optimize designs to reduce weight, improve aerodynamics, and enhance mechanical properties, leading to increased turbine efficiency and performance. By reducing weight and optimizing cooling, investment casting contributes to enhanced fuel efficiency and reduced emissions.
6. Consistency and Quality:
Investment casting ensures consistent and high-quality turbine components. The casting process allows for tight dimensional tolerances, precise control over material composition, and excellent surface finish. These factors are crucial for turbine components to perform reliably, ensuring safe and efficient turbine operation.
7. Rapid Prototyping and Iteration:
Investment casting facilitates rapid prototyping and iterative design refinement in the development of turbine components. By using the same investment casting process for prototyping and production, manufacturers can quickly produce functional prototypes for testing and evaluation. This iterative approach enables design optimization, reduces development time, and accelerates the introduction of new turbine components.
8. Collaboration and Expertise:
Investment casting often involves collaboration between turbine manufacturers, casting experts, and material suppliers. The expertise of casting professionals ensures the proper execution of the casting process, material selection, and quality control. Collaboration between industry experts drives innovation, advancements, and continuous improvement in turbine component design and manufacturing.
Investment casting has revolutionized the production of turbine components by enabling complex geometries, high-temperature alloy utilization, near-net shape manufacturing, cooling channel integration, design optimization, consistent quality, rapid prototyping, and collaborative expertise. These advancements contribute to improved turbine efficiency, durability, and performance, leading to more reliable and efficient turbine systems in various industries.