Investment casting, also known as lost-wax casting, is a manufacturing process that has been used for centuries to create intricate and complex metal parts. It offers a range of advantages, including the ability to produce lightweight components with intricate geometries and excellent surface finishes. Let’s explore the process and the potential it holds for complex and lightweight metal parts.
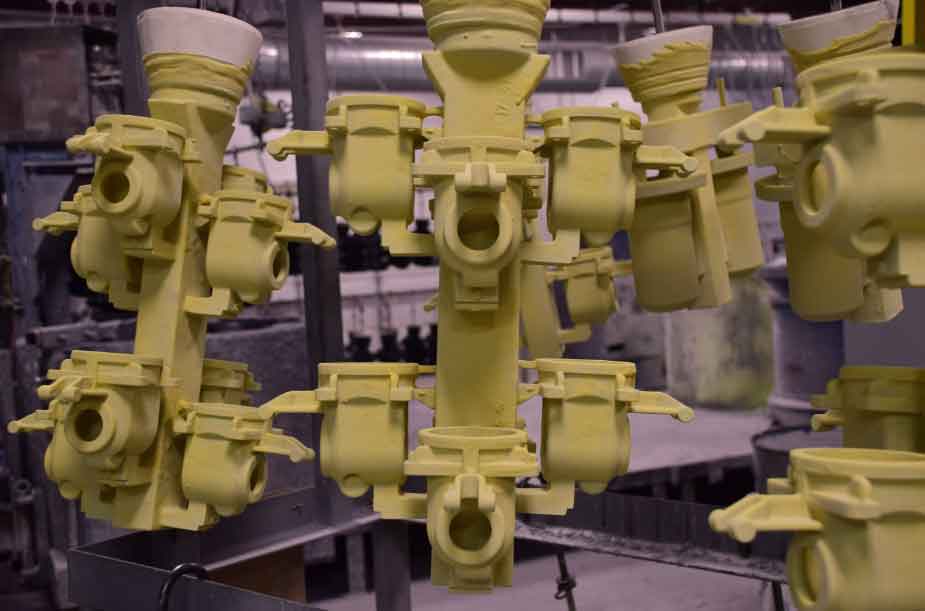
The Investment Casting Process
The investment casting process involves several steps:
- Pattern Creation: The process starts with the creation of a pattern, which can be made from various materials such as wax, plastic, or even metal. The pattern is an exact replica of the desired final part.
- Pattern Assembly: Multiple patterns are attached to a gating system to create a cluster. The gating system consists of channels and gates that allow the flow of molten metal and the escape of air during casting.
- Shell Molding: The cluster of patterns is then coated with a ceramic shell by repeatedly dipping it in a slurry of fine ceramic material and allowing it to dry. This process is repeated several times to build up a thick shell.
- Dewaxing: Once the ceramic shell is dry and hardened, it is placed in an oven or autoclave to melt or vaporize the pattern, leaving behind a hollow cavity in the shell that matches the desired part.
- Preheating: The ceramic shell is preheated to remove any remaining moisture and improve the strength of the mold.
- Casting: Molten metal, often an alloy, is poured into the preheated ceramic shell through the gating system. The metal fills the cavity and takes the shape of the pattern.
- Cooling and Solidification: The filled mold is allowed to cool and the metal solidifies, forming the final shape of the part.
- Shell Removal: Once the metal has solidified, the ceramic shell is broken or chemically dissolved, revealing the cast metal part.
- Finishing: The cast part may require some post-processing, such as removing excess material, surface treatment, machining, or heat treatment, to achieve the desired final specifications.
Advantages of Investment Casting for Complex and Lightweight Metal Parts
Investment casting offers several advantages that make it ideal for the production of complex and lightweight metal parts:
- Intricate Geometries: Investment casting enables the production of parts with intricate and complex geometries, including thin walls, sharp corners, and fine details. This is due to the ability of the wax or other pattern materials to replicate intricate features accurately.
- Design Freedom: The process allows for design freedom, as complex shapes can be achieved without the limitations imposed by traditional manufacturing methods such as machining or forging. It enables the production of parts with internal features, undercuts, and varying wall thicknesses.
- Superior Surface Finish: Investment casting produces parts with excellent surface finishes directly from the mold, reducing the need for additional machining or finishing operations. This is particularly important for parts that require tight tolerances or contact with other components.
- Material Versatility: Investment casting can be used with a wide range of metals and alloys, including aluminum, stainless steel, titanium, and superalloys. This versatility allows for the selection of materials with specific properties to meet the requirements of the application.
- Weight Reduction: Investment casting can achieve lightweight designs by creating thin-walled structures, hollow sections, or integrating features that reduce overall weight while maintaining strength and structural integrity.
- Cost Efficiency: While investment casting may have higher upfront costs compared to some other manufacturing methods, it can provide cost savings in the long run by reducing material waste, minimizing the need for machining, and eliminating the need for assembly of multiple components.
Applications of Investment Casting
Investment casting finds applications in various industries, including aerospace, automotive, defense, medical, and jewelry. Some examples include:
- Aerospace: Investment casting is commonly used in aerospace applications for producing turbine blades, vanes, impellers, and other components with intricate cooling passages, reducing weight while maintaining high-performance characteristics.
- Automotive: Investment casting is employed in the automotive industry to manufacture engine components, transmission parts, and suspension components that require high strength, dimensional accuracy, and complex shapes.
- Medical: Investment casting is used to produce medical implants, surgical instruments, and dental components that require biocompatibility, precise geometries, and intricate features.
- Jewelry: Investment casting is a popular method in the jewelry industry for creating intricate and detailed designs in precious metals.
Conclusion
Investment casting is a versatile manufacturing process that unlocks the potential for complex and lightweight metal parts. With its ability to create intricate geometries, superior surface finishes, and material versatility, investment casting offers a cost-effective solution for producing high-quality components across various industries. The process continues to evolve and adapt to new materials and technologies, expanding its potential in the realm of complex and lightweight metal part production.