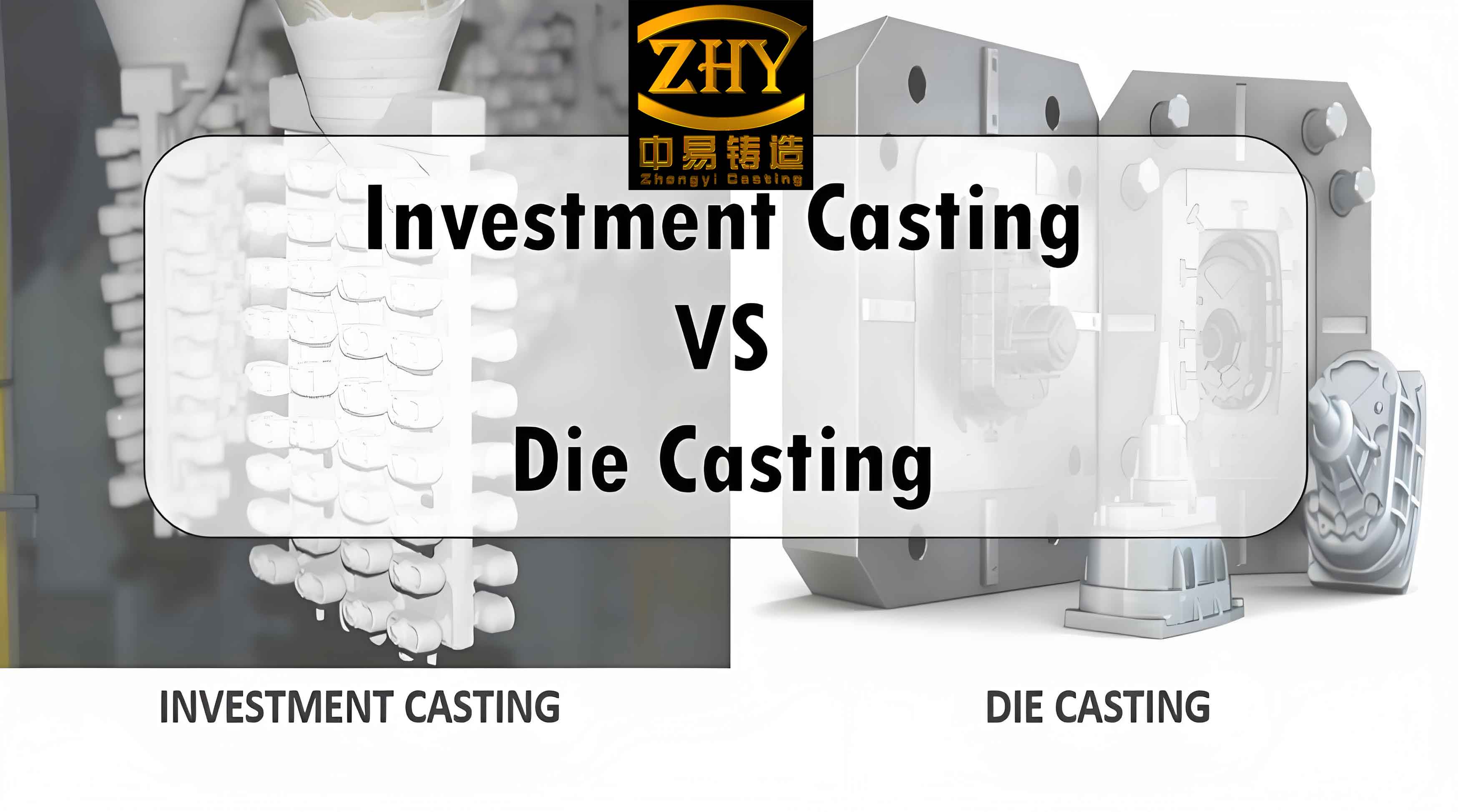
Investment casting and die casting are two prominent manufacturing processes used to create metal parts. Each method has unique advantages, disadvantages, and applications. Understanding the differences between these two processes is essential for selecting the most appropriate method for specific applications. This article provides a detailed comparative analysis of investment casting and die casting, highlighting their processes, advantages, disadvantages, and applications.
Introduction to Investment Casting
Investment casting, also known as precision casting or lost-wax casting, is a process that involves creating a wax pattern, coating it with a ceramic shell, and then casting metal into the shell. The primary steps in investment casting include:
- Pattern Creation: A wax pattern is created to replicate the final part.
- Assembly: Multiple wax patterns are assembled into a tree-like structure.
- Shell Building: The assembly is dipped into a ceramic slurry and coated with fine sand to form a shell.
- Dewaxing: The ceramic shell is heated to remove the wax, leaving a hollow mold.
- Casting: Molten metal is poured into the ceramic mold.
- Finishing: The ceramic shell is broken away, and the part is cleaned and finished.
Introduction to Die Casting
Die casting is a manufacturing process that involves forcing molten metal into a mold cavity under high pressure. The primary steps in die casting include:
- Mold Preparation: The mold is coated with a lubricant to facilitate part removal and temperature control.
- Metal Injection: Molten metal is injected into the mold cavity at high pressure.
- Cooling: The metal cools and solidifies within the mold.
- Ejection: The mold is opened, and the solidified part is ejected.
- Trimming: Excess material, known as flash, is trimmed away from the part.
Comparative Analysis of Investment Casting and Die Casting
Aspect | Investment Casting | Die Casting |
---|---|---|
Process Complexity | Involves multiple steps, including wax pattern creation and shell building. | Relatively straightforward, involving metal injection into a mold. |
Part Complexity | Capable of producing highly intricate and complex geometries. | Best suited for simpler shapes with limited complexity. |
Material Options | Wide range of materials, including high-temperature alloys. | Limited to lower melting point metals like aluminum, zinc, and magnesium. |
Surface Finish | Excellent surface finish with minimal post-processing required. | Good surface finish, but may require additional finishing. |
Production Volume | Suitable for low to medium production volumes. | Ideal for high-volume production runs. |
Tooling Costs | Higher initial tooling costs due to ceramic shell creation. | Lower initial tooling costs, but molds can wear out faster. |
Dimensional Accuracy | High dimensional accuracy and tight tolerances. | Good dimensional accuracy, but less precise than investment casting. |
Cycle Time | Longer cycle times due to multiple process steps. | Shorter cycle times, allowing for faster production. |
Advantages and Disadvantages
Investment Casting
Advantages:
- High Precision: Produces parts with tight tolerances and high dimensional accuracy.
- Complex Geometries: Capable of creating intricate and complex shapes.
- Material Versatility: Can use a wide range of materials, including high-temperature alloys.
- Superior Surface Finish: Minimal post-processing required due to excellent surface finish.
Disadvantages:
- Higher Tooling Costs: Initial tooling costs are higher due to the need for ceramic shell creation.
- Longer Cycle Times: The process involves multiple steps, leading to longer production times.
- Limited Production Volume: Best suited for low to medium production volumes.
Die Casting
Advantages:
- Fast Production: Shorter cycle times allow for high-volume production runs.
- Lower Tooling Costs: Initial tooling costs are lower compared to investment casting.
- Good Surface Finish: Produces parts with good surface finishes, though additional finishing may be required.
Disadvantages:
- Limited Material Options: Suitable only for lower melting point metals.
- Lower Dimensional Accuracy: Less precise than investment casting, though still acceptable for many applications.
- Simpler Geometries: Best suited for simpler part shapes with less complexity.
Applications of Investment Casting and Die Casting
Application | Investment Casting | Die Casting |
---|---|---|
Automotive Industry | Engine components, turbine blades, exhaust systems | Engine blocks, transmission housings, brackets |
Aerospace Industry | Turbine blades, structural components | Avionics housings, brackets, fittings |
Medical Industry | Surgical instruments, prosthetics | Medical device housings, connectors |
Defense Industry | Weapon components, missile parts | Armament casings, mounting brackets |
Industrial Equipment | Pumps, valves, impellers | Gearboxes, motor housings, structural parts |
Conclusion
Investment casting and die casting are essential manufacturing processes, each offering unique benefits and suitable for different applications. Investment casting is ideal for producing high-precision, complex parts with excellent surface finishes, making it suitable for low to medium production volumes and a wide range of materials. Die casting, on the other hand, excels in high-volume production of simpler parts with good surface finishes, albeit with limited material options.
Selecting the appropriate casting method depends on various factors, including the complexity of the part, production volume, material requirements, and desired surface finish. Understanding the strengths and limitations of each process ensures optimal manufacturing outcomes, enhancing the durability and performance of the final products. As technology advances, both investment casting and die casting will continue to evolve, offering innovative solutions to meet the growing demands of various industries.