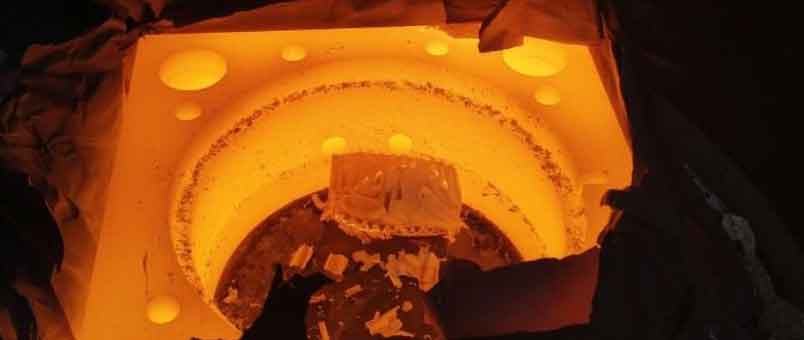
Case Study 1: Cracking in Heat Treated Steel Gears
Problem:
A manufacturer of steel gears for heavy machinery encountered cracking issues during the heat treatment process. The cracks appeared after quenching and caused significant rejection rates.
Solution:
- Analysis: The manufacturer conducted a detailed analysis of the cracking issue, examining factors such as material composition, heat treatment parameters, and component design.
- Material Selection: It was discovered that the steel used for the gears had a higher carbon content, leading to increased hardenability and a higher risk of cracking. The manufacturer decided to switch to a steel grade with lower carbon content and improved hardenability.
- Preheating: Preheating the gears before quenching was introduced to reduce thermal gradients and minimize the risk of cracking. The preheating temperature and time were optimized based on the material properties.
- Quenching Medium: The manufacturer evaluated different quenching media and selected an appropriate one with a controlled cooling rate to prevent rapid and uneven cooling, which can contribute to cracking.
- Stress Relieving: After quenching, the gears underwent a stress-relieving treatment to reduce residual stresses and minimize the risk of cracking. The stress relieving temperature and time were carefully controlled to achieve the desired effect without compromising hardness.
- Process Monitoring: The heat treatment process was closely monitored using temperature sensors and quenching medium analysis to ensure consistent and controlled conditions. Any deviations from the desired parameters were immediately addressed.
- Quality Control: Non-destructive testing, such as ultrasonic testing and magnetic particle inspection, was implemented to detect any potential cracks or defects before the gears were put into service.
Result: By implementing these measures, the manufacturer successfully mitigated the cracking issue. The rejection rates were significantly reduced, and the gears met the required mechanical properties and quality standards.
Case Study 2: Surface Decarburization in Carburized Components
Problem:
A supplier of carburized components for the automotive industry faced issues with surface decarburization during the heat treatment process. The excessive carbon loss resulted in components not meeting the required hardness specifications.
Solution:
- Atmosphere Control: The supplier implemented a controlled gas atmosphere during the carburizing process. The carbon potential of the atmosphere was optimized to ensure sufficient carbon diffusion into the component’s surface without causing excessive carbon loss.
- Case Depth Monitoring: The supplier introduced regular monitoring of case depth using microhardness testing and metallographic examination. This helped ensure that the carburized layer met the required thickness and hardness specifications.
- Protective Coatings: The use of protective coatings on the component surface prior to heat treatment was adopted. These coatings acted as a barrier against oxygen contact, minimizing the risk of surface decarburization.
- Quenching Medium: The selection of an appropriate quenching medium with controlled cooling rates was crucial to prevent further carbon loss and minimize distortion.
- Surface Preparation: Thorough cleaning of the component surface before carburizing was emphasized to remove any contaminants that could accelerate decarburization.
- Process Optimization: The carburizing parameters, such as temperature, time, and carbon potential, were optimized through experimentation and analysis to achieve the desired case depth and hardness while minimizing carbon loss.
- Quality Control: Regular inspection and testing were conducted to detect any signs of surface decarburization or inadequate case depth. This included visual inspection, microhardness testing, and metallographic analysis.
Result: By implementing these measures, the supplier effectively minimized surface decarburization in the carburized components. The components met the required hardness specifications, ensuring their suitability for use in the automotive industry.
These case studies highlight the importance of understanding and addressing heat treatment defects through careful analysis, process optimization, and quality control measures. Each situation requires a thorough investigation and the implementation of specific solutions tailored to the material, component design, and heat treatment process parameters.