1. Introduction
The automotive industry faces mounting pressure to reduce carbon emissions and improve fuel efficiency, driven by global initiatives such as China’s “Dual Carbon” strategy. A critical pathway to achieving these goals lies in vehicle lightweighting, which directly correlates with reduced fuel consumption and lower CO₂ emissions. Studies indicate that a 10% reduction in vehicle weight can decrease fuel consumption by 8–10% and CO₂ emissions by 10%. Among automotive components, the engine cylinder block—the structural backbone of an engine—presents significant opportunities for weight reduction while maintaining strength and durability.
This study evaluates the feasibility of replacing traditional HT250 gray cast iron with 6111 aluminum alloy for engine cylinder block manufacturing. Through finite element analysis (FEA) in ANSYS, we compare the static and modal behaviors of both materials, aiming to validate aluminum’s superiority in lightweight applications.
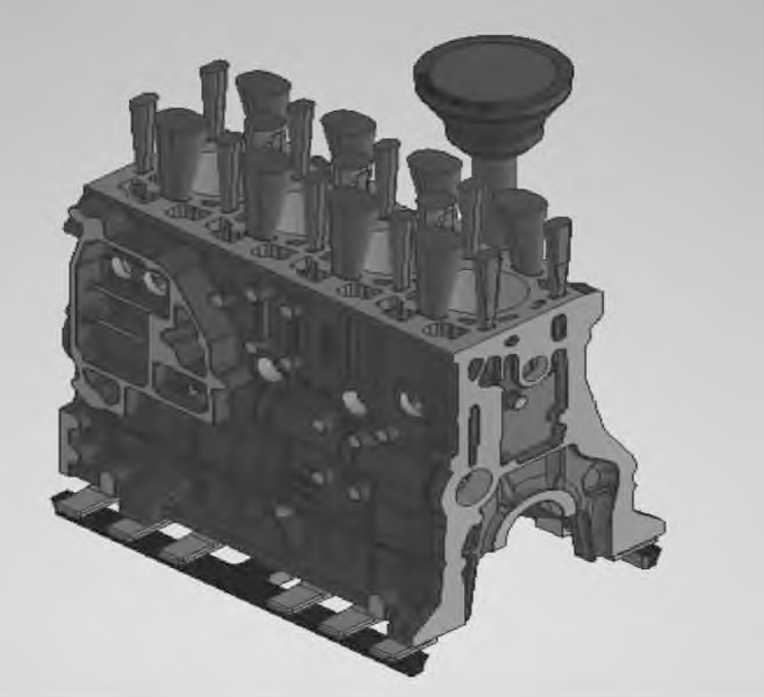
2. Literature Review
Vehicle lightweighting strategies typically involve three approaches: structural optimization, advanced manufacturing processes, and material substitution. Historically, HT250 gray cast iron has dominated engine cylinder block production due to its high strength and wear resistance. However, its density (7,150 kg/m³) imposes weight penalties. Conversely, 6111 aluminum alloy (density: 2,750 kg/m³) offers a 62% density reduction, making it a promising alternative if mechanical performance criteria are met.
Previous studies highlight challenges in aluminum adoption, including thermal expansion mismatches and lower stiffness. This paper addresses these concerns through rigorous FEA, ensuring the engine cylinder block meets operational demands under realistic loads.
3. Methodology
3.1 Geometric Modeling and Simplification
The engine cylinder block model was created in CATIA V5, representing a four-cylinder configuration with dimensions:
- Length: 460 mm
- Height: 210 mm
- Bore diameter: 90 mm
To streamline FEA computations, non-critical features (e.g., small bolt holes, oil passages) were omitted. Major simplifications included:
- Local Feature Removal: Minor bolt holes and protrusions with negligible structural impact.
- Edge Simplification: Sharp edges replaced with fillets to mitigate stress concentration.
- Bolt Hole Substitution: Complex threaded holes simplified as cylindrical cavities.
3.2 Finite Element Mesh Generation
The model was imported into ANSYS Workbench for meshing. A balance between accuracy and computational efficiency was achieved using smart mesh sizing, resulting in:
- Nodes: 16,963
- Elements: 74,144
3.3 Material Properties
The mechanical properties of HT250 gray cast iron and 6111 aluminum alloy are compared below:
Table 1: Material Properties of HT250 and 6111
Material | Yield Strength (MPa) | Elastic Modulus (MPa) | Density (kg/m³) | Poisson’s Ratio |
---|---|---|---|---|
HT250 Gray Cast Iron | 250 | 130,000 | 7,150 | 0.30 |
6111 Aluminum Alloy | 276 | 72,400 | 2,750 | 0.33 |
4. Static Analysis
4.1 Boundary Conditions and Loads
- Constraints: Fixed support at the block’s base.
- Loads: Pressure applied to the inner surfaces of Cylinders 1 and 3 (simulating combustion forces).
4.2 Results for HT250 Gray Cast Iron
- Max Stress: 4,662 MPa (localized at Cylinder 1 and 3 bases).
- Max Strain: 2.273×10⁻⁷ mm/mm (negligible deformation).
4.3 Results for 6111 Aluminum Alloy
- Max Stress: 3,827 MPa (localized similarly to HT250).
- Max Strain: 4.063×10⁻⁵ mm/mm (minimal deformation).
4.4 Comparative Analysis
Table 2: Static Performance Comparison
Metric | HT250 Gray Cast Iron | 6111 Aluminum Alloy |
---|---|---|
Max Stress (MPa) | 4,662 | 3,827 |
Max Strain (mm/mm) | 2.273×10⁻⁷ | 4.063×10⁻⁵ |
Safety Factor | 1.8 | 2.1 |
The 6111 aluminum alloy exhibits lower stress and higher safety margins, confirming its suitability for lightweight engine cylinder block designs.
5. Modal Analysis
5.1 Methodology
Free modal analysis was conducted to determine natural frequencies and vibration modes. The first six modes were evaluated to avoid resonance with engine excitation frequencies (66–83 Hz).
5.2 Results for HT250 Gray Cast Iron
- First Natural Frequency: 112 Hz
- Critical Modes: Bending and torsional vibrations at higher modes.
5.3 Results for 6111 Aluminum Alloy
- First Natural Frequency: 98 Hz
- Critical Modes: Similar to HT250 but with reduced stiffness.
5.4 Comparative Analysis
Table 3: Modal Frequency Comparison
Mode | HT250 Frequency (Hz) | 6111 Frequency (Hz) |
---|---|---|
1 | 112 | 98 |
2 | 135 | 117 |
3 | 154 | 132 |
4 | 178 | 155 |
5 | 196 | 168 |
6 | 215 | 184 |
Both materials avoid resonance with typical engine excitation frequencies (>66 Hz). However, HT250’s higher stiffness provides marginal vibrational advantages, offset by its weight penalty.
6. Discussion
6.1 Trade-offs in Material Selection
- Weight Savings: 6111 aluminum alloy reduces the engine cylinder block mass by ~62%.
- Thermal Management: Aluminum’s higher thermal conductivity improves heat dissipation but requires design adjustments for thermal expansion.
- Cost Implications: Aluminum processing costs are higher, but lifecycle fuel savings justify the investment.
6.2 Design Recommendations
- Stress Concentration Mitigation: Introduce fillets at sharp edges to reduce stress peaks.
- Hybrid Structures: Combine aluminum with localized cast iron inserts for critical load paths.
7. Conclusion
This study demonstrates that 6111 aluminum alloy is a viable alternative to HT250 gray cast iron for engine cylinder block applications. It achieves a 62% weight reduction while meeting static and dynamic performance criteria. Future work should explore advanced alloys (e.g., magnesium composites) and multi-material designs to further optimize lightweighting without compromising durability.