On the premise of ensuring the strength and safety performance of the vehicle, reduce the curb weight of the vehicle as much as possible, realize lightweight, so as to improve the power performance of the vehicle, reduce fuel consumption and reduce exhaust pollution. The fuel consumption per 100 km can be reduced by 0.3-0.6 L for every 100 kg reduction of vehicle curb weight. If the vehicle weight is reduced by 10%, the fuel efficiency can be increased by 6% – 8%. With the need of environmental protection and energy saving, the lightweight of automobile has become the trend of automobile development in the world. The lightweight of automobile casting has also become one of the important development directions of automobile casting.
1. Lightweight design of Automobile Casting
Due to the need of overall safety factor of castings, equal thickness design is one of the main design methods of automobile castings. However, the main drawback of equal thickness design is that it can not give full play to the structural properties and lead to the increase of casting weight. CAE analysis and topology optimization are used to optimize the design of parts, so that the stress values of parts are close to each other, i.e. the wall thickness of each part is inconsistent, and the parts with small stress are thinned, so as to reduce the weight of parts. Considering that the casting forming can realize the forming of complex structure castings and various irregular cross sections. During the design, CAE or topology optimization are used to analyze the stress of components. According to the distribution of force, the shape of components and the specific local material thickness are determined. The weight of parts can be greatly reduced by reinforcing the casting, digging holes and changing the section.
Figure 2 is the comparison of casting shape before and after the optimized design of commercial vehicle support by Dongfeng Precision Casting Co., Ltd. [2]. It can be seen that the initial weight of the casting is 6.6kg, which is a typical equal thickness design. After a series of lightweight design methods, such as reinforcement, hole digging and variable section, the weight of the casting is changed to 3.0 kg, and the weight reduction effect can be more than 50%.
2. Light alloy automobile castings
The use of light alloy materials such as aluminum and magnesium is the main weight reduction measure for automobile manufacturers in various countries. The density of aluminum is only 1 / 3 of that of steel, and it has excellent corrosion resistance and ductility. The density of magnesium is smaller, only 2 / 3 of that of aluminum, and it has excellent fluidity in high pressure casting. The specific strength (ratio of strength to mass) of aluminum and magnesium is very high, which plays an important role in reducing self weight and improving fuel efficiency. The competitiveness of American automobile industry has been improved in recent two years, which is closely related to the large-scale use of aluminum magnesium structural casting and integrated casting [3].
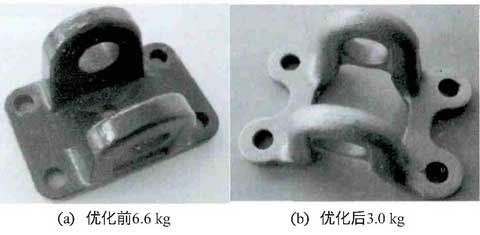
The new 5 Series launched by BMW in Germany, with the latest generation of magnesium aluminum composite in-line six cylinder engine block, has a weight reduction of 10 kg compared with the previous generation, greatly improving performance and fuel economy. However, it should be noted that the price of aluminum magnesium and other light alloys is much higher than that of steel materials, which limits their wider application in the automotive industry. However, despite the high price of raw materials, the single car consumption of magnesium and aluminum castings has increased year by year. On the one hand, it makes up for the cost increase through technological progress; on the other hand, market competition forces automobile manufacturers to reduce profits and adopt more light alloys. However, in order to increase the consumption of light alloy and reduce the purchase price of mg Al ingot, the development of advanced forming technology is one of the keys.
3. High performance of Automobile Casting materials
One of the effective ways to reduce the weight of castings is to improve the properties of materials and make the parts with unit weight bear higher load. Bracket structure castings account for a large proportion of automobile castings, so the development of castings has become one of the focuses. By means of heat treatment and other measures, the microstructure of the material is changed, so as to improve the strength, rigidity or toughness of the parts and effectively reduce the weight of the parts.
The strength of austempered ductile iron is not only higher than that of common cast steel, but also its density is lower than that of steel. Its density is 7.1g/cm3, while that of cast steel is 7.8g/cm3, which is widely recommended in recent years. Using austempered ductile iron, it is 10% lighter than steel casting under the same casting size. Dongfeng Motor Company has carried out the lightweight verification of adopting equal temperature quenched ductile iron instead of steel casting in a commercial vehicle, and redesigned 14 suspension parts according to the high strength characteristics of equal temperature quenched ductile iron. Table 1 shows the light-weight effect of equal temperature quenched nodular cast iron after replacement. The total weight is reduced by nearly 40%, and the effect is significant. It should be noted that the lightweight effect in Table 1 is not only the result of material substitution, but also the contribution of lightweight design. Generally speaking, the material replacement of automobile castings is often accompanied by the lightweight design of parts.
In terms of aluminum alloy and magnesium alloy castings, high-strength and high toughness materials are also used for replacement. On the basis of the original light alloy weight reduction, high-performance materials are used for further weight reduction. General Motors of the United States uses high-performance ae44 alloy to replace the original aluminum alloy, and high-pressure casting method is used to produce the subframe. On the basis of the aluminum alloy weight reduction, the weight is further reduced by 6 kg.