The gear box is an important part of the power transmission of metro vehicles. During the operation of the vehicle, the stress of the gear box is complex and requires high strength and toughness. In order to ensure the safety of operation, the ductile iron castings are not allowed to have shrinkage holes, cold shuts, cracks and other casting defects. The interior of the ductile iron castings needs X-ray inspection, and the surface of the ductile iron castings needs wet fluorescent magnetic particle inspection. The gearbox box is a moving part product, its material is nodular cast iron, and its main wall thickness is about 10mm. The lightweight design of the box can reduce the energy consumption of vehicle operation, which is economical and in line with the requirements of the national double-carbon policy.
The most direct way to lighten weight is to optimize the box structure and reduce the wall thickness of ductile iron castings on the premise of ensuring the safety of vehicle operation. However, reducing the wall thickness of ductile iron castings will reduce the filling capacity of molten metal. The solidification mode of ductile iron is paste solidification. When the filling capacity of molten metal is insufficient, casting defects such as insufficient pouring and cold shut are easy to occur. With the thinning of the wall thickness of ductile iron castings, the feeding channel of molten metal will become narrow, and casting defects such as shrinkage porosity and shrinkage cavity are easy to occur.
Generally, the metro gear box is made of nodular cast iron, with the material grade of QT450-10, the main wall thickness of 10-12 mm, and the weight of 170 kg. It is a typical thin-walled cast iron. The three-dimensional schematic diagram of the casting is shown in the figure. Furan resin sand molding and medium frequency furnace melting process are used in production. Generally, the melting temperature is about 1500 ℃ and the pouring temperature is about 1400 ℃.
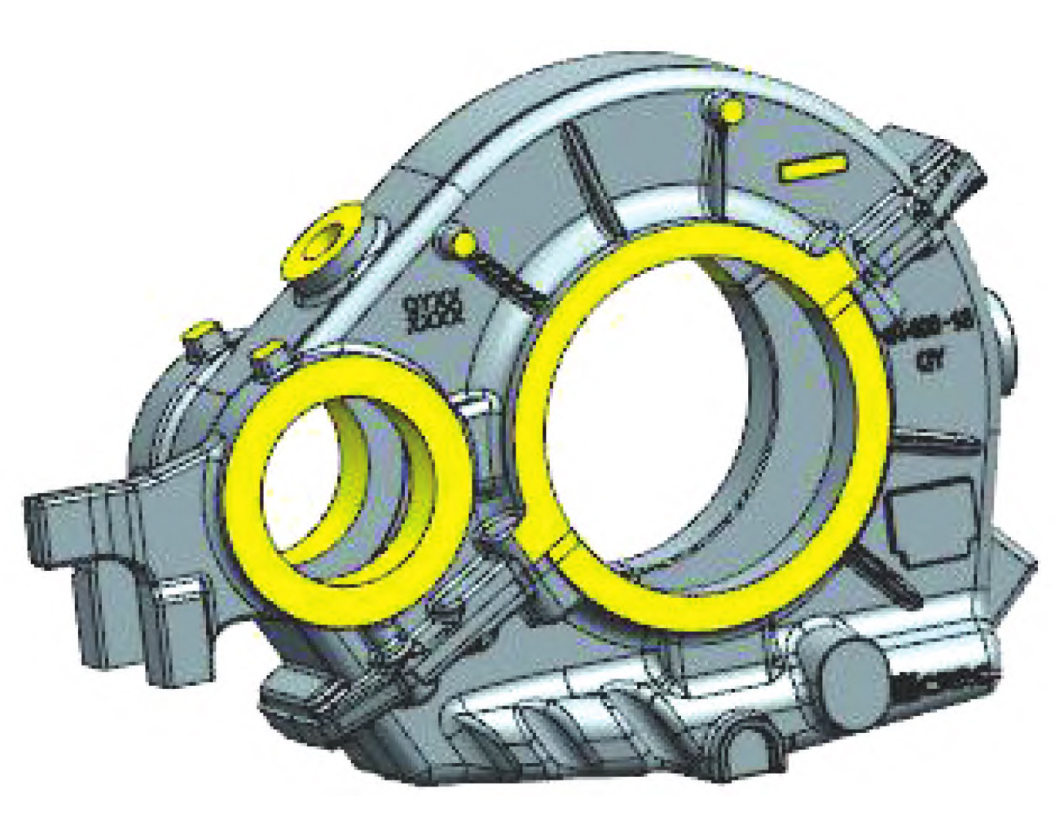
(1) After the lightweight design of the metro gear box, the simulation calculation meets the safety requirements of vehicle operation, and the weight of the box is reduced by about 20%.
(2) In the production of lightweight box ductile iron castings, measures such as adjusting chemical composition, increasing mold temperature, optimizing ductile iron castings process and capping spheroidization method have been taken to ensure the stability of small batch production process, which can be used for mass production, provide reliable basis for the structural design of gear box, and respond to the national energy conservation and emission reduction requirements.
Through simulation calculation, the structural design of gear box is optimized to reduce its wall thickness; The chemical composition ratio, spheroidizing inoculation process, pouring process, casting conditions, etc. are also studied to improve the fluidity of molten iron, reduce casting defects such as “insufficient pouring” and cold shut, and obtain lightweight box to achieve the role of energy conservation and emission reduction.