The chemical composition of molten iron is shown in Table 1. The double wire feeding spheroidization process with cover is adopted, the addition amount of fesimg25re3 spheroidizing agent is 0.7%, and the method of compound inoculation with 0.3% pretreatment agent and 0.2% 75fesi is adopted for inoculation in the ladle. Since the spheroidizing agent is wrapped in the steel sheet to avoid oxidation, the wire feeding length and speed are controlled by PLC and directly enter the bottom of molten iron. The alloy absorption rate is high and the spheroidizing effect is good. After spheroidizing, the molten iron is quickly scraped and transported to the pouring station by forklift.
Element | C | Si | Mn | S | P | Mg(incomplete) | Sn |
Content | 3.7 | 2.4 | 0.5 | 0.015 | 0.05 | 0.05 | 0.06 |
In order to reduce the shrinkage cavity or porosity defects of castings, the pouring temperature of molten iron is set at 1430~1450 ℃, and clean chill blocks should be placed on the pouring site to prevent the pouring from being affected when the temperature of molten iron is higher than 1450 ℃. During pouring, the clean chill blocks should be immediately put into the pouring ladle for cooling, and the cavity should be re poured with molten iron after pouring. The vacuum negative pressure on the site should be controlled at -0.05~-0.06 MPa during pouring, and the pressure maintaining time after pouring should be set as 1 h.
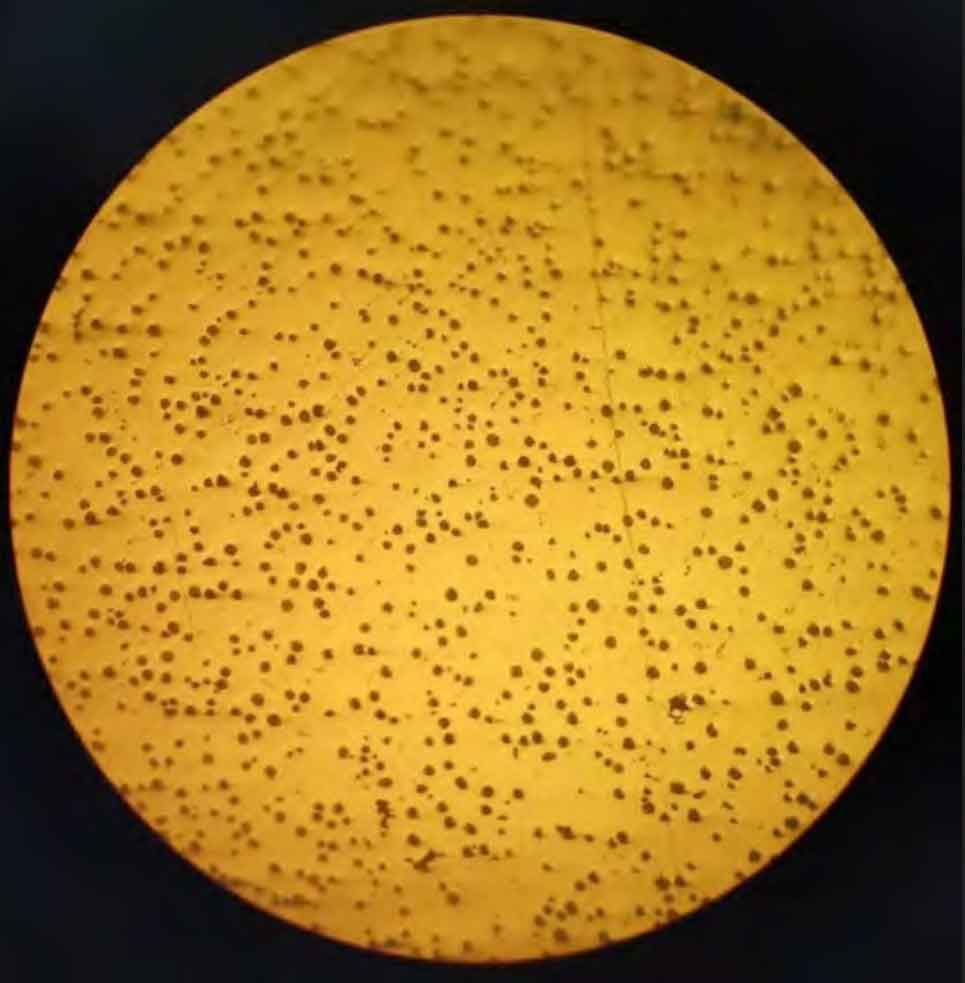
The pilot production is carried out according to the above process. The metallographic structure and mechanical energy test results of the attached cast test bar are shown in Table 2, and the metallographic structure photos are shown in the figure.
Project | Spheroidization level / level | Graphite size / grade | Pearlite volume fraction /% | Cementite volume fraction /% | Phosphorus eutectic volume fraction /% | Tensile strength /mpa | Elongation /% |
Numerical value | 2 | 7 | 65 | ≤1.0 | ≤0.5 | 641 | 3.5 |
The 5810 shot blasting equipment is used to sand the vacuum pump shell castings after sand falling, and the riser and sprue are removed by gas cutting. From the riser neck, the castings are observed without shrinkage cavity or porosity. The overall dimensions of the castings are measured, which meet the dimensional requirements of the designed vacuum pump shell castings. The casting of vacuum pump shell was sent to the processing unit for processing, and no shrinkage cavity and sand slag hole were found on the processing surface, which can meet the use requirements of vacuum pump.