Lost Foam Casting and Semi-continuous Casting are two distinct methods used in the casting process, each with its own advantages and limitations. Let’s compare them in terms of their principles, process, applications, and benefits:
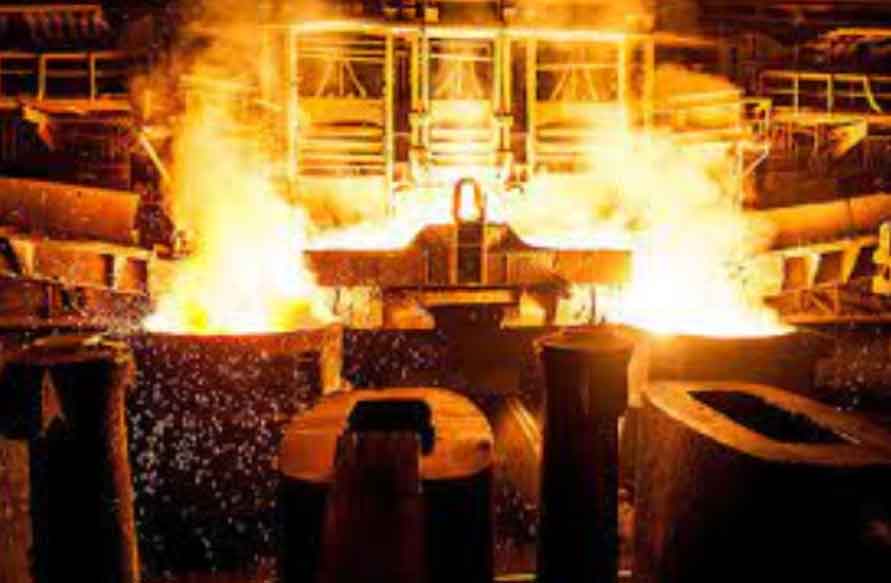
- Principle:
- Lost Foam Casting: This method involves creating a foam pattern of the desired casting shape, which is then embedded in a compacted sand mold. Molten metal is poured into the mold, vaporizing the foam pattern, and filling the void to create the final casting.
- Semi-continuous Casting: This method involves continuously casting the molten metal into a mold or series of molds to produce a continuous solidified shape. The casting is periodically cut into desired lengths.
- Process:
- Lost Foam Casting:
- Pattern Creation: A foam pattern is produced using a polystyrene foam material.
- Pattern Assembly: Multiple foam patterns are assembled to form a cluster.
- Pattern Coating: The foam cluster is coated with a refractory material to enhance surface quality and provide thermal insulation.
- Mold Formation: The coated cluster is embedded in a flask, and sand is tightly compacted around it to create the mold.
- Casting: Molten metal is poured into the mold, replacing the foam pattern, and solidifies to form the final casting.
- Semi-continuous Casting:
- Mold Preparation: The mold is prepared, typically made of metal, with a specific shape and size.
- Continuous Casting: Molten metal is continuously poured into the mold, allowing the solidification process to occur while the casting is continuously withdrawn.
- Cutting: The continuous casting is periodically cut into desired lengths, resulting in individual castings.
- Lost Foam Casting:
- Applications:
- Lost Foam Casting: This method is suitable for complex and intricate castings, especially those with internal cavities and thin walls. It is commonly used in automotive, aerospace, and industrial applications.
- Semi-continuous Casting: This method is commonly used for producing continuous lengths of castings, such as bars, rods, tubes, and beams. It finds application in industries like steel manufacturing, aluminum production, and continuous casting of various metals.
- Benefits:
- Lost Foam Casting:
- Complex Geometries: It enables the production of castings with intricate internal features and complex shapes.
- Reduced Post-processing: The elimination of cores and part consolidation can reduce the need for additional machining and assembly operations.
- Material Efficiency: The foam patterns can be recycled, resulting in less material waste.
- Semi-continuous Casting:
- Cost Efficiency: It allows for the continuous production of castings, reducing labor and setup costs associated with individual casting operations.
- Improved Quality: The continuous solidification process can result in improved casting structure and mechanical properties.
- High Production Rates: The continuous nature of the process enables high-volume production.
- Lost Foam Casting:
Lost Foam Casting is well-suited for complex and intricate castings with internal features, while Semi-continuous Casting is ideal for continuous lengths of castings. The choice between the two methods depends on the specific casting requirements, desired geometry, and production volume.