1. Introduction
In modern industrial production, aluminum alloys have become an important material due to their excellent mechanical properties, low density, good electrical conductivity, and corrosion resistance. They are widely used in aerospace, automotive, and other fields. Low-pressure casting is a commonly used casting method for aluminum alloys, which can produce high-quality castings. However, during the low-pressure casting process, various defects may occur, affecting the quality of the castings. Therefore, it is necessary to analyze the defects of low-pressure casting aluminum alloys and study the corresponding heat treatment processes to improve the quality of the castings.
2. Defects of Low Pressure Casting Aluminum Alloys
2.1 Casting Cracks
- Types and Causes: There are two common types of casting cracks. Thermal cracks occur along the grain boundaries and are characterized by black oxides in the cracks and a serrated shape. This is mainly due to uneven cooling rates during solidification, resulting in internal stresses that exceed the maximum tensile strength of the material when the shape of the casting is complex and the thickness is uneven. Cold cracks occur within the crystal and have a shiny silver appearance at the fracture because no oxidation reaction occurs. This is also related to internal stresses caused by uneven cooling.
- Solutions: To address casting cracks, it is necessary to clearly define the chemical composition and strictly control impurities within the standard range. At the same time, avoid the melt being affected by high temperatures. When the temperature exceeds the maximum bearing capacity, control the residence time of the melt in the furnace. Use scientific methods to control the temperature and cooling speed of the casting mold to ensure that the liquid metal has a uniform and stable flow and cooling speed, and prevent debris from falling into the melt. For example, for A356 aluminum alloy, the iron content should be controlled within 0.15% and not exceed 0.2% at most for strength parts such as hubs and frames in low-pressure casting.
2.2 Lace Structures (White Flowers)
- Causes: The lace structure occurs when the composition adjustment before casting is not in place, or the melt is overheated and has a long residence time in the furnace. In addition, a small diameter of the filter tube hole, a high casting temperature, a short crystallizer, or the loss of effectiveness of the modification and refinement agent can also lead to this structure.
- Solutions: Strictly control the chemical composition of the alloy to ensure that the impurity content is within the standard range. Design the filtering system scientifically and optimize the crystallization device.
2.3 Pinholes
- Causes: Pinholes are mainly caused by excessive hydrogen content in the aluminum liquid (the density of the test block is less than 2), resulting in the formation of needle-like densely distributed pores during mold solidification. This may be due to excessive recycled materials, insufficient refining of the aluminum liquid, excessive water content in the compressed air used for low pressure, or a high pouring temperature.
- Solutions: If there are too many recycled materials, control them within 20%. For insufficient refining of the aluminum liquid, use argon or nitrogen with a purity of 99.999% for degassing and adjust the degassing parameters (rotational speed, gas flow rate, degassing time) according to the test results of the vacuum pumping test block, requiring the density of the test block to be not less than 2.3 g/cm³. For excessive water content in the compressed air used for low pressure, the water content is generally expressed by the normal pressure dew point and should be in the range of -60°C – 70°C. The pouring temperature should generally not exceed 740°C.
2.4 Insufficient Pouring
- Causes: Insufficient pouring occurs when the casting product cannot be in a complete state. This is because the pouring temperature is too low, resulting in a fast solidification speed of the casting. Before the casting is filled, it has already solidified, or because the pouring system lacks a wide channel and cannot ensure a large flow of aluminum liquid, resulting in a bottleneck problem, or because the mold has poor exhaust and causes gas resistance.
- Solutions: Design the pouring system to optimize the aluminum liquid flow and optimize the mold exhaust system. During production, preheat the mold to effectively avoid the problem of rapid cooling of the aluminum liquid. Ensure that the coating is distributed reasonably and has a uniform thickness in the cavity. Ensure that the mold has good exhaust conditions to avoid waste of resources due to insufficient pouring. When designing the mold, require the casting wall thickness to be greater than 3 mm and design the exhaust plug reasonably.
2.5 Shrinkage Porosity
- Causes: If the aluminum alloy liquid level is too high or the pouring temperature is too high, resulting in a slow cooling speed and a large shrinkage amount, coarse grains will be formed, and a loose structure will be produced, resulting in shrinkage porosity castings.
- Solutions: Improve the existing process scientifically, precisely control the temperature required for mold heating, insulation, and pouring. Design the riser size scientifically, maintain a normal thickness of the coating, avoid large differences in thickness, and pay attention to the supply amount of the casting shrinkage. The casting should be designed symmetrically.
2.6 Oxide Inclusions and Gas Holes
- Causes: If the pressurization parameters are not operated properly, causing the aluminum liquid to splash when injected into the cavity, bubbles cannot be released and are instead wrapped in the casting, resulting in metal oxidation and oxide inclusions. If the aluminum liquid contains a large amount of hydrogen, many irregular holes will be produced, which are common in thick sand mold castings and have a significant impact on the physical and chemical properties of the aluminum alloy. Reaction gas holes are formed when the gas generated by the high-temperature resin combustion of the coated sand core or the gas generated by the high-temperature of the un-dried coating penetrates into the casting.
- Solutions: Improve the operation quality, ensure the smooth pouring of the aluminum liquid, and avoid excessive impact. Select a reasonable inner runner design for the gate and use bottom pouring for a more reasonable pouring method.
3. Heat Treatment Processes of Low Pressure Casting Aluminum Alloys
3.1 Solution Quenching Principles
- Eutectic Type: The typical eutectic type in industrial production is the ZL104 Al – Si – Mg – Mn alloy. In addition to the main chemical elements of Al, Si, Mg, and Mn, it also contains a small amount of Fe, Cu, and Zn elements, and the impurities are controlled within 0.6%. The as-cast structure is composed of α solid solution, α and Si binary eutectic, and compounds doped with AlSiMnFe and Mg₂Si. The quenching temperature promotes the dissolution of Mg₂Si into the solid solution, and the insoluble Si reacts with Al – Si – Mn – Fe to form aggregates. The quenching structure consists of α solid solution, α and Si, and Al – Si – Mn – Fe, and the low-melting eutectic is α, Si, Al – Si – Mn – Fe with an overburning temperature of nearly 560°C.
- Solid Solution Type: The solid solution type does not have the elements related to the insoluble eutectic of the casting. The crystallization or segregation and second-phase components of the casting due to crystallization cooling will be affected by high temperatures during the quenching stage and disappear after the strengthening phase is completely dissolved. Usually, the quenching condition is mainly composed of α solid solution with a relatively wide temperature range. A typical example is the ZL201 Al – Cu – Mn – Ti alloy. In addition to the main elements of Al, Cu, Mn, and Ti, it also contains a small amount of Zn and Mg, and the impurities are required to be within 0.3%. The as-cast structure is composed of α solid solution, Al₂Cu, Al₁₂Mn₂Cu, and Al₃Ti. During the quenching heating stage, Al₂Cu is dissolved in α solid solution and Al solid solution and decomposes into fine particle T phase (Al₁₂Mn₂Cu) under the influence of high temperature. To obtain the optimal structure and performance of the aluminum alloy, a two-stage quenching method can be used for heating: at 530°C with a fluctuation of ±3°C, which is slightly lower than the production-specified temperature, for the first-stage heating, so that the Al₂Cu strengthening phase can be smoothly dissolved with α and α solid solution, and the T phase particles are completely precipitated at the grain boundaries. The second-stage heating should be in accordance with the specified production process temperature, that is, 540°C with a fluctuation of ±3°C error, so that the remaining Al₂Cu phase can be completely dissolved with α solid solution. For this type of alloy, the impurity element Si should be strictly controlled to avoid exceeding the content. If the Si element exceeds the standard, a ternary eutectic of a, Si, and Al₂Cu with a melting point of 525°C will be produced in production, reducing the quenching temperature of the aluminum alloy product and having a negative impact on the physical and chemical properties.
3.2 Quenching Temperature
For casting aluminum alloys, under the premise of not causing tissue overheating, gradually increasing the heating temperature during quenching can assist the strengthening phase to accelerate the dissolution with the Al-based solid solution, thereby reducing the time to reach a saturated state and enhancing the strengthening effect of the aluminum alloy. In general, the quenching temperature of the eutectic type should be controlled 10°C – 15°C below the overburning temperature, and the quenching temperature of the solid solution type should be controlled 5°C – 10°C below the overburning temperature.
3.3 Holding Time
The holding time after quenching is related to the original composition, dissolution speed, and tissue state of the casting aluminum alloy. Generally, the eutectic type has few strengthening components, resulting in a relatively high dissolution speed of Mg₂Si. Therefore, under normal quenching temperature conditions, holding for 1 – 4 hours can meet the tissue performance requirements of the technical conditions. At the same time, during the holding period, the performance of the aluminum alloy is proportional to the holding time. If the holding time is too long, for example, more than 9 hours, the performance of the aluminum alloy will decrease under the influence of the enhanced aggregation effect of the Si element.
3.4 Cooling Speed and Transfer Time
For the cooling speed during the quenching stage, it is necessary to ensure that the strengthening phase dissolved in the solid solution does not precipitate during the quenching stage and strictly control the transfer time of the quenching. The cooling speed is affected by the properties of the quenching medium, such as heat capacity and viscosity. Clean water with a temperature difference should be selected as the quenching cooling medium, which is convenient to obtain, has a low cost, and is easy to control the experimental effect. Different temperatures of clean water can provide different cooling speeds, which have strong applicability to various aluminum alloy products. The cooling speed of the aluminum alloy decreases as the water temperature increases and increases as the water temperature decreases.
3.5 Aging of Casting Aluminum Alloys
As a characteristic of the tissue transformation of aluminum alloys during the aging stage, migration and diffusion will cause the supersaturated solid solution to undergo a precipitation decomposition phenomenon. When the solute atoms are in a dissolved state, they will nucleate and precipitate due to supersaturation, and aggregation and accumulation will also occur with the precipitation of micro impurities, resulting in an aggregation phenomenon of undissolved excess phases. In general, the aging principle is as follows: after the alloy completes the quenching process of solid solution, the precipitation phase in the aging period will precipitate and transform in the order of GP zone, θ”(GPⅡ zone), θ’, θ(CuAl₂). For the Al – Cu alloy, its aging precipitation is GP zone, β’, β(Mg₃Al₃), and for the Al – Si – Mg alloy, its aging precipitation is GP zone, β’, β(Mg₂Si). According to the use performance of aluminum alloys, they can be divided into strengthening aging, complete aging, quenching treatment, softening aging, and incomplete aging with quenching treatment. When aluminum alloy products require high strength but have a low plasticity index, strengthening aging treatment can be used for aluminum alloys. From various experimental data, for both eutectic and solid solution types of casting aluminum alloys, if normal quenching is maintained and an aging temperature of 175°C – 185°C and a holding time of 5 – 10 hours are maintained, a good strengthening effect can be obtained. If the aging temperature or time does not meet the production requirements, the production technical requirements cannot be met, and the tissue and performance of the aluminum alloy will also decline accordingly.
4. Tables for Summary
4.1 Defects and Solutions
Defect | Cause | Solution |
---|---|---|
Casting Cracks | Uneven cooling rates due to complex shape and uneven thickness; internal stresses exceeding material strength | Define chemical composition, control impurities, avoid high-temperature melt, control residence time, control mold temperature and cooling speed |
Lace Structures (White Flowers) | Composition adjustment not in place, melt overheated, long residence time in furnace; small diameter of filter tube hole, high casting temperature, short crystallizer, loss of effectiveness of modification and refinement agent | Control chemical composition, design filtering system, optimize crystallization device |
Pinholes | Excessive hydrogen content in aluminum liquid due to various reasons | Control recycled materials, use argon or nitrogen for degassing, control water content in compressed air, control pouring temperature |
Insufficient Pouring | Low pouring temperature, bottleneck in pouring system, poor mold exhaust | Design pouring system, preheat mold, ensure coating distribution and thickness, ensure good mold exhaust |
Shrinkage Porosity | High aluminum alloy liquid level or high… |
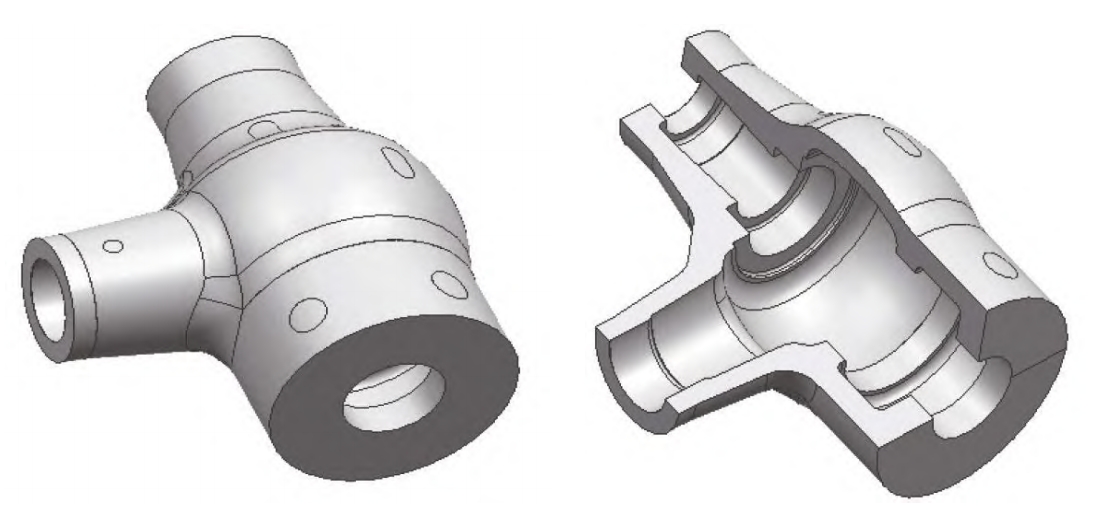