1. Introduction
Aluminum alloy castings have gained significant popularity in various industries due to their favorable properties such as low density, high strength, good electrical and thermal conductivity, and excellent corrosion resistance. Among these, the aluminum alloy cabin, a large-scale casting component, has crucial applications in aerospace and other fields where high precision and quality are required. This article focuses on the low pressure casting process of aluminum alloy cabins, exploring its various aspects from design to defect analysis and solutions.
1.1 Significance of Aluminum Alloy Cabin Casting
The aluminum alloy cabin serves as a critical component in many systems, especially in aerospace applications where it houses various control system components. The integrity and quality of the cabin are of utmost importance as any defect could lead to catastrophic consequences. Therefore, a thorough understanding of the casting process is essential to ensure the production of high-quality cabins.
1.2 Overview of Low Pressure Casting
Low pressure casting is a widely used casting method that offers several advantages over other techniques. It involves the use of a lower pressure to force the molten metal into the mold cavity, resulting in a more controlled filling process. This method is suitable for producing complex-shaped castings with good mechanical properties and reduced porosity. In the case of aluminum alloy cabins, low pressure casting can provide a balance between cost and quality, making it an attractive option for manufacturers.
2. Product Structure and Technical Requirements
2.1 Structure of the Aluminum Alloy Cabin
The aluminum alloy cabin typically has a complex structure. It is a revolving barrel wall casting with uneven wall thickness. As shown in Figure 1, the product has an outer dimension of , a minimum wall thickness of , and a maximum wall thickness of . It also features several windows, including 4 circular windows of and 2 square windows. The product design mass is . The uneven wall thickness and the presence of these features contribute to the challenges in the casting process, as it can lead to the formation of hot spots and potential defects.
2.2 Technical Requirements
The cabin is a fully processed product, and strict technical requirements must be met. All processed surfaces should be free of casting defects. Before processing, the casting blank needs to undergo 100% X-ray inspection according to the ASTM E155 standard, with all regions meeting the I level standard. The internal of the casting should not contain any defects such as pores, cracks, shrinkage porosity, or inclusions. Linear dimensions follow the GB/T1804 – m tolerance standard for unmarked dimensions, unmarked form and position tolerances are according to GB/T1184 – H, and the remaining casting dimension tolerances are in accordance with GB/T6414 – 1999 CT9 level.
3. Low Pressure Casting Process Design
3.1 Casting System Design
3.1.1 Selection of Casting Method
Based on the product structure and requirements, low pressure casting was selected as the appropriate casting method. The product’s internal cavity has a semi-closed structure, making it difficult for a metal core to be demolded. Therefore, a combination of a coated sand core and a metal mold was used for trial production. After the product is demolded, the coated sand core is removed to obtain the casting blank.
3.1.2 Design of Pouring System
The pouring system was designed as a stepped feeding internal gate, with feeding from the upper, middle, and lower parts. The runner was designed inside the sand core, allowing the aluminum liquid to pass through the sand core while the sand core provides insulation for the aluminum liquid. Numerical simulation using ProCAST software showed that this design enables a smooth filling process without turbulence. The melt enters the cavity from the gate and fills the cavity from bottom to top in a stable manner. The temperature field during solidification also meets the requirements of the casting solidification sequence, ensuring sufficient feeding to the hot spots of the casting and preventing shrinkage porosity and shrinkage cavity defects.
3.2 Metal Mold Structure Design
3.2.1 Mold Opening Structure
The metal mold for this product has an upper, lower, left, and right four-opening structure. During production, the left and right cavities are opened first, followed by the upper and lower cavities. To ensure smooth demolding, a reasonable draft angle needs to be set for the metal mold.
3.2.2 Draft Angle and Ejection Rod Layout
The upper cavity has a depth of , and the lower cavity has a depth of . To ensure sufficient holding force for the upper cavity to carry the blank and sand core when the upper cavity is opened and to reduce the resistance for the lower cavity during mold opening, different draft angles were set for the upper and lower cavities. The upper cavity has a draft angle of with a draft depth of , while the lower cavity has a draft angle of with a draft depth of . The ejection rod layout is designed symmetrically according to the product’s revolving structure to ensure balanced ejection of the blank.
3.3 Process Parameter Determination
3.3.1 Importance of Process Parameters
The process parameters play a crucial role in ensuring the quality of the casting. Due to the uneven wall thickness of the product blank and the flow of aluminum liquid from the middle to the outer circle during filling, it is necessary to set appropriate pouring parameters to ensure a stable filling process without turbulence.
3.3.2 Determination of Optimal Parameters
Through numerical simulation by setting different filling parameters and comparing the flow fields, the optimal process parameters were determined. As shown in Table 1, when the aluminum liquid temperature is , the mold temperature is , and the filling pressurization speed is , the aluminum liquid filling is the most stable.
Process Parameter | Pressure /MPa | 增压速度 /(MPa・s) | Time /s | Aluminum Liquid Temperature /°C |
---|---|---|---|---|
升液 | 0.0200 | 0.0020 | 10 | |
充型 | 0.0360 | 0.0008 | 20 | |
增压 | 0.0024 | 10 | ||
0.0600 | 700 | |||
保压 | 0.0600 | 360 | ||
冷却 | 260 | |||
出型及下一阶段 | 240 |
4. Defect Analysis and Solutions
4.1 Defect Analysis
4.1.1 Local Shrinkage Porosity
100% X-ray inspection of the aluminum alloy cabin revealed local shrinkage porosity in certain areas. The affected area is located at the middle waist of the product, where the wall thickness is thicker than the upper and lower parts, making it a hot spot. Although a “one” -shaped runner was designed as a feeder in the numerical simulation, local shrinkage porosity still occurred in the symmetric position away from the internal gate of the “one” -shaped runner due to the large diameter of the middle waist.
4.1.2 Local Black Skin on Inner Wall after Machining
After heat treatment and machining of the casting, local black skin was observed on the inner wall of the casting. This indicates that the inner diameter of the product in some areas is larger than expected, and some blank dimensions do not meet the machining requirements. The main cause of this problem is the cracking and bulging of the sand core during the mold closing process, which is due to the large difference in thermal expansion coefficients between the metal mold and the sand core.
4.2 Solutions to Defects
4.2.1 Solution for Local Shrinkage Porosity
To address the local shrinkage porosity problem, the “one” -shaped runner was changed to a “cross” -shaped runner. This modification enhances the feeding of the annular hot spot of the product and effectively solves the shrinkage porosity defect caused by insufficient feeding.
4.2.2 Solution for Local Black Skin on Inner Wall
To solve the problem of local black skin on the inner wall, the size of the upper cavity of the metal mold was reduced by during the hot state of the metal mold. This increases the mold closing gap between the upper and lower molds, ensuring that the sand core is not crushed during the mold closing process and solving the problem of oversized inner wall dimensions caused by the crushing of the sand core.
5. Conclusion
5.1 Key Findings
- The proper design of the draft angle for the upper and lower cavities of the metal mold ( for the upper cavity with a draft depth of and for the lower cavity with a draft depth of ) enables smooth demolding and continuous production.
- The optimal low pressure casting process parameters for the aluminum alloy cabin are an aluminum liquid temperature of , a mold temperature of , and a filling pressurization speed of , which ensure a stable filling process.
- Measuring the dimensions of the metal mold in the hot state can accurately reflect the 配合间隙 between the mold and the sand core, avoiding product inner wall dimension errors caused by mold expansion and sand core cracking.
5.2 Implications for Future Research and Production
The research on the low pressure casting process of the aluminum alloy cabin provides valuable insights for future production. It emphasizes the importance of considering the product structure and characteristics during the design process and the need for continuous optimization of the casting process through defect analysis and solution implementation. Future research could focus on further improving the casting process to enhance the quality and performance of aluminum alloy cabins, exploring new materials and techniques to meet the increasing demands of various industries.
In conclusion, the low pressure casting process of aluminum alloy cabins is a complex but crucial manufacturing process. By understanding and addressing the various challenges and requirements, manufacturers can produce high-quality aluminum alloy cabins that meet the strict standards of modern industries.
6. Discussion on the Influence of Different Factors on the Casting Process
6.1 The Impact of Mold Temperature on Casting Quality
The mold temperature plays a vital role in the low pressure casting process of aluminum alloy cabins. A suitable mold temperature can affect the fluidity of the molten aluminum and the solidification rate of the casting. When the mold temperature is too low, the molten aluminum may solidify too quickly, resulting in incomplete filling of the mold cavity and potential defects such as cold shuts and misruns. On the other hand, if the mold temperature is too high, it may cause excessive expansion of the sand core and the metal mold, leading to dimensional inaccuracies and potential cracking of the casting.
In the case of the aluminum alloy cabin studied, a mold temperature of was determined to be optimal. This temperature allows for a proper balance between the fluidity of the aluminum liquid and the solidification process. At this temperature, the aluminum liquid can fill the mold cavity smoothly, and the solidification sequence is in accordance with the design requirements, ensuring the formation of a high-quality casting without significant defects related to mold temperature.
6.2 The Role of Pouring System Design in Feeding Hot Spots
The design of the pouring system is crucial for ensuring proper feeding of hot spots in the casting. Hot spots are areas in the casting where the metal solidifies last due to their thicker sections or slower cooling rates. In the aluminum alloy cabin, these hot spots are located in the upper, middle, and lower parts where the wall thickness is relatively thicker.
The stepped feeding internal gate design, with runners located inside the sand core, provides an effective means of feeding these hot spots. The aluminum liquid flowing through the sand core is able to maintain its heat and supply the necessary metal to the hot spots during the solidification process. This design helps to prevent the formation of shrinkage porosity and shrinkage cavities in the hot spot areas, ensuring the integrity and quality of the casting.
6.3 The Significance of Draft Angle and Ejection Rod Layout in Demolding
The draft angle and ejection rod layout are essential factors for successful demolding of the casting from the metal mold. The draft angle allows for easy separation of the casting from the mold by providing a tapered surface that reduces the frictional resistance during ejection. In the case of the aluminum alloy cabin, the different draft angles set for the upper and lower cavities ( for the upper cavity and for the lower cavity) ensure that the casting can be smoothly removed from the mold without causing damage to the casting or the mold.
The symmetric layout of the ejection rods according to the revolving structure of the product provides balanced force during ejection, preventing any uneven stress on the casting that could lead to deformation or cracking. This proper design of the draft angle and ejection rod layout is crucial for maintaining the dimensional accuracy and surface quality of the casting during the demolding process.
7. Comparison with Other Casting Methods
7.1 Low Pressure Casting vs. Gravity Casting
Gravity casting is a traditional casting method that relies on the force of gravity to fill the mold cavity with molten metal. In comparison, low pressure casting offers several advantages. In gravity casting, the filling process is less controlled, and there is a higher risk of defects such as porosity and inclusions due to the free-falling nature of the molten metal. Low pressure casting, on the other hand, uses a controlled pressure to force the molten aluminum into the mold cavity, resulting in a more uniform filling process and better quality castings.
For the aluminum alloy cabin, gravity casting would be challenging due to its large size and complex structure. The high mass of the product would require a significant amount of molten aluminum to be poured in a single operation, increasing the risk of defects. Low pressure casting, with its ability to control the filling process and provide proper feeding to hot spots, is a more suitable option for producing high-quality aluminum alloy cabins.
7.2 Low Pressure Casting vs. Die Casting
Die casting is a high-speed casting method that uses a die cavity to form the casting. While die casting offers high production rates and excellent dimensional accuracy, it also has some limitations. Die casting typically requires high-pressure injection of the molten metal, which can lead to the formation of internal defects such as porosity and cracks in some cases.
Low pressure casting, although slower in production rate compared to die casting, provides a more gentle filling process that is beneficial for complex-shaped castings like the aluminum alloy cabin. It allows for better control of the solidification process and can produce castings with good mechanical properties and fewer internal defects. Additionally, the equipment cost for low pressure casting is generally lower than that for die casting, making it a more cost-effective option for certain applications.
8. Future Trends in Aluminum Alloy Cabin Casting
8.1 Advancements in Materials and Alloys
The development of new aluminum alloys with improved properties is an area of continuous research. These new alloys may offer enhanced strength, better corrosion resistance, and improved thermal conductivity, which are crucial for the performance of aluminum alloy cabins. For example, the addition of certain alloying elements can modify the microstructure of the alloy, resulting in better mechanical properties.
In addition to alloy development, research is also focused on improving the quality of existing alloys. This includes techniques such as grain refinement and impurity control to enhance the overall quality of the casting. The use of advanced materials and alloys in the future will likely lead to the production of higher quality aluminum alloy cabins with improved performance and reliability.
8.2 Integration of Numerical Simulation and Optimization Techniques
Numerical simulation has become an essential tool in the casting process design and optimization. In the future, more advanced simulation techniques will be developed to provide more accurate predictions of the casting process. These simulations will not only consider the fluid flow and solidification of the molten metal but also factors such as heat transfer, stress analysis, and microstructure evolution.
By integrating numerical simulation with optimization algorithms, it will be possible to automatically optimize the casting process parameters to achieve the best possible casting quality. This will significantly reduce the trial-and-error process in casting production and improve the efficiency and quality of the manufacturing process.
8.3 Automation and Industry 4.0 in Casting Production
The trend towards automation and Industry 4.0 is also making its way into the casting industry. Automated casting systems can improve production efficiency, reduce labor costs, and increase the consistency and quality of the castings. In the context of aluminum alloy cabin casting, automated pouring systems, robotic handling of molds and castings, and real-time monitoring of the casting process using sensors are some of the potential applications.
Real-time monitoring can provide valuable data on the casting process, allowing for immediate detection and correction of any potential issues. This integration of automation and Industry 4.0 technologies will transform the casting production process, making it more efficient, reliable, and capable of meeting the increasing demands of modern industries.
9. Conclusion
The low pressure casting process of aluminum alloy cabins is a complex and multi-faceted manufacturing process that requires careful consideration of various factors. From the design of the casting system and metal mold to the determination of process parameters and the analysis and solution of defects, each step plays a crucial role in ensuring the production of high-quality castings.
The research presented in this article has provided a comprehensive understanding of the low pressure casting process for aluminum alloy cabins. It has highlighted the importance of factors such as mold temperature, pouring system design, draft angle, and ejection rod layout in determining the quality of the casting. Additionally, comparisons with other casting methods have demonstrated the advantages of low pressure casting for this particular application.
Looking towards the future, advancements in materials, numerical simulation, and automation offer exciting opportunities for further improving the casting process and the quality of aluminum alloy cabins. By embracing these trends and continuously optimizing the manufacturing process, the casting industry can meet the growing demands of modern industries and produce high-quality aluminum alloy cabins that are essential for various applications.
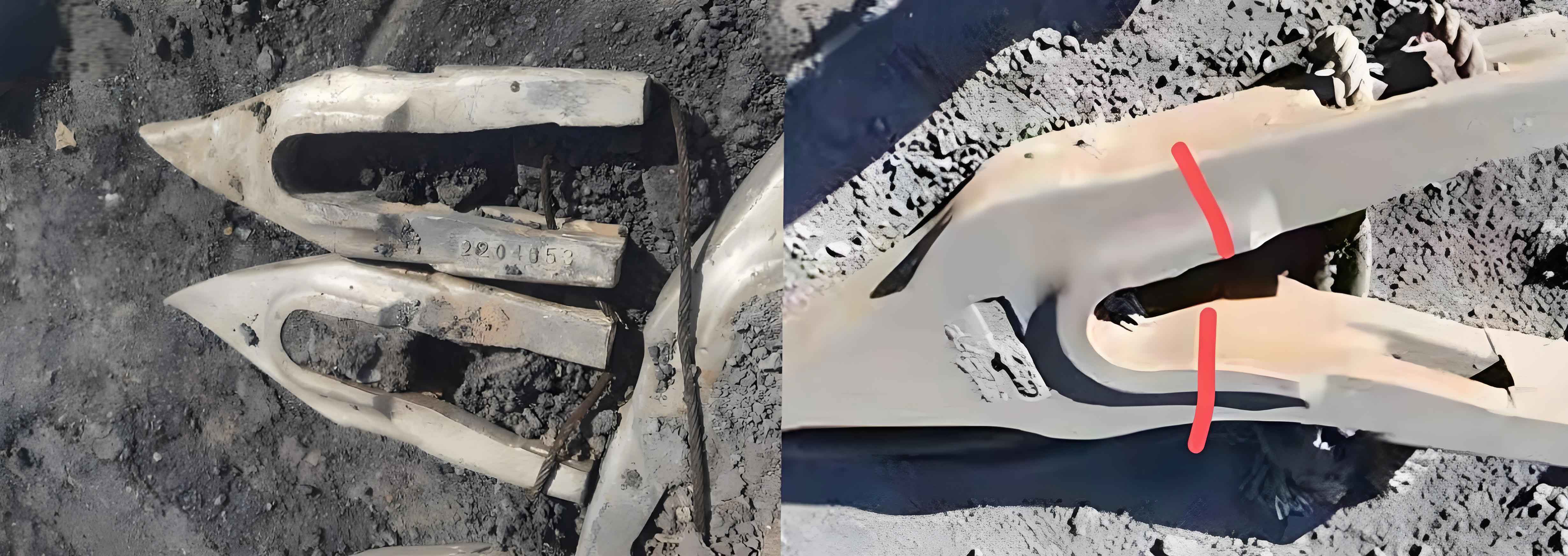