Casting defects pose significant challenges in the production process, often leading to compromised product quality, increased costs, and delays in delivery. However, with a systematic approach to identifying, understanding, and addressing these defects, it is possible to maintain high quality in cast products. This article provides insights on reducing the occurrence of casting defects.
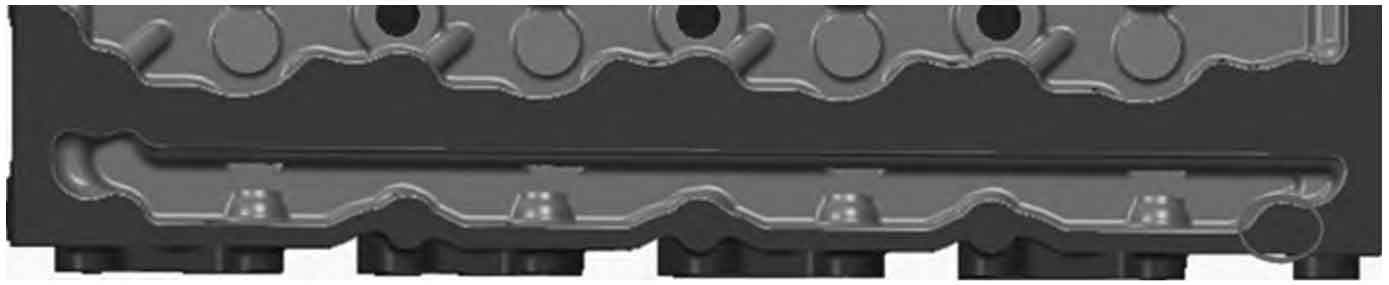
- Meticulous Designing: A well-designed casting and gating system can prevent a wide range of defects. It ensures that the molten metal flows smoothly, solidifies uniformly, and gases escape efficiently. Utilizing modern simulation software can aid in optimizing the design and anticipating possible defects.
- Quality Raw Materials: Using high-quality raw materials is a crucial first step in maintaining the quality of cast products. The molten metal and molding material must be free of contaminants that could lead to defects like inclusions and gas porosity.
- Process Control: Standardizing and closely controlling each step of the casting process can minimize variability and reduce the likelihood of defects. This includes maintaining the correct pouring temperature, ensuring proper filling of the mold, and managing cooling rates.
- Training of Personnel: Well-trained personnel are essential for maintaining quality. They need to understand the casting process, be aware of potential defects, and know how to prevent and correct them. Regular training and updates on best practices can help ensure consistency and quality.
- Regular Inspection: Frequent and thorough inspection of the cast products is key to catching defects early, before they become major issues. Non-destructive testing methods, such as X-ray or ultrasonic testing, can be particularly useful in detecting internal defects.
- Root Cause Analysis: When defects occur, a systematic root cause analysis can help identify the source of the problem. This approach helps focus corrective actions on the root cause, rather than treating the symptoms, leading to more effective prevention of future defects.
- Continuous Improvement: A continuous improvement approach, including regularly reviewing processes, gathering and analyzing data, and making adjustments based on findings, can help reduce casting defects over time.
While it is nearly impossible to completely eliminate casting defects, their occurrence can be significantly reduced by following best practices in design, process control, personnel training, inspection, and continuous improvement. By doing so, foundries can maintain the quality of their cast products, meet their customers’ expectations, and stay competitive in the market.