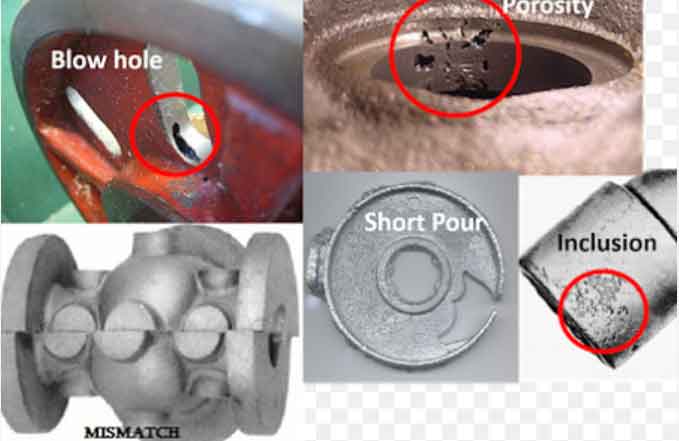
Effective management of casting defects is crucial for ensuring optimal quality assurance in metal casting processes. By implementing robust strategies and practices, manufacturers can minimize defects, improve overall casting quality, and meet customer requirements. This article explores key steps and considerations for managing casting defects to achieve optimal quality assurance.
- Defect Detection and Identification:
- Implement rigorous inspection and testing methods to detect casting defects. This may include visual inspection, non-destructive testing (NDT) techniques like X-ray or ultrasonic testing, and dimensional measurements.
- Train inspectors to recognize different types of defects and their characteristics to accurately identify and categorize them.
- Root Cause Analysis:
- Perform detailed root cause analysis to determine the underlying factors contributing to casting defects. Use tools such as fishbone diagrams, Pareto analysis, or 5 Whys to systematically identify root causes.
- Analyze process parameters, material properties, and environmental conditions to identify potential sources of defects.
- Process Optimization:
- Optimize casting processes to minimize the occurrence of defects. This may involve adjusting process parameters such as pouring temperature, cooling rates, gating system design, and mold or core materials.
- Utilize advanced technologies like computer simulations or predictive modeling to optimize the casting process and reduce defects.
- Material Control and Quality Assurance:
- Establish strict material control practices to ensure the quality of raw materials used in casting. Implement proper material handling, storage, and testing procedures to prevent material-related defects.
- Conduct thorough quality assurance measures, including inspection and testing of incoming materials, in-process inspections, and final inspections to maintain consistent casting quality.
- Continuous Improvement:
- Foster a culture of continuous improvement by actively seeking feedback from customers, analyzing defect trends, and implementing corrective actions.
- Encourage employee involvement and empowerment to contribute ideas for defect prevention and process improvement.
- Regularly review and update standard operating procedures (SOPs) to incorporate best practices and lessons learned.
- Supplier Collaboration:
- Collaborate closely with material suppliers to ensure the quality and consistency of supplied materials. Communicate quality requirements, conduct audits, and establish strong relationships to address any material-related defects.
- Training and Skill Development:
- Provide comprehensive training programs for employees involved in the casting process. This includes training on defect recognition, process optimization, quality control techniques, and proper handling of materials.
- Encourage employees to enhance their skills and knowledge through continuous learning and professional development opportunities.
- Documentation and Data Analysis:
- Maintain detailed documentation of casting processes, defect analysis reports, and corrective actions taken.
- Analyze data on defect occurrences, trends, and root causes to identify areas for improvement and guide decision-making.
Managing casting defects is essential for achieving optimal quality assurance in metal casting processes. By implementing robust defect detection, root cause analysis, process optimization, material control, continuous improvement, and employee training practices, manufacturers can minimize defects and enhance casting quality. Effective management of casting defects not only ensures customer satisfaction but also leads to improved operational efficiency and long-term success in the casting industry.