The metals that are widely used in metal matrix ceramic composites include aluminum alloy, cast iron and alloy steel. For application scenarios such as mining and cement industry, the workpiece is required to have high wear resistance and impact resistance, so cast iron and steel matrix ceramic composites are widely used. Under the condition of coal grinding, the common roll mainly has the following problems: ① the roll surface is washed quickly, the service life is low, the maintenance cost is high, and the repair is difficult; ② The average particle size of coal mill can not meet the production demand; ③ Due to the wear of the roll surface, the running vibration of the whole workpiece is intensified and the stability is reduced. Therefore, it is necessary to explore a new type of metal-based ceramic composite roll. The application practice shows that the service life and performance of the composite roll have been greatly improved compared with the ordinary high chromium roll and surfacing roll, and the advantages are very obvious.
Distance / cm | 0 | 1.0 | 2.0 | 3.0 | 4.0 | 5.0 | 6.0 | 7.0 | 8.0 | 9.0 |
Composite rolls | 64.8 | 63. 5 | 62. 1 | 63. 0 | 61. 9 | 58. 6 | 55. 2 | 52. 3 | 48. 1 | 45. 4 |
Cr12 rolls | 45.3 | 46. 1 | 44. 9 | 45. 3 | 46. 2 | 44. 9 | 45. 8 | 45. 3 | 44. 9 | 45. 0 |
At the beginning of the 20th century, domestic ceramic particle reinforced metal matrix composites became a research hotspot. Feng Peizhong and others proposed to use centrifugal casting technology to prepare WC particle reinforced steel matrix composite roll ring, which has higher hardness, strength and wear resistance as the working layer of the roll. The comparison of surface hardness between WC particle reinforced steel matrix composite roll and traditional material roll is shown in the table. The analysis shows that the hardness of composite roll is significantly higher than that of ordinary Cr12 roll, and the wear resistance is improved more significantly. The volume fraction and size of ceramic particles in the composite have a great impact on the wear resistance of the workpiece, and the ceramic particles are uniformly distributed in the outer layer of the roller ring, as shown in Fig. 1a and 1b.
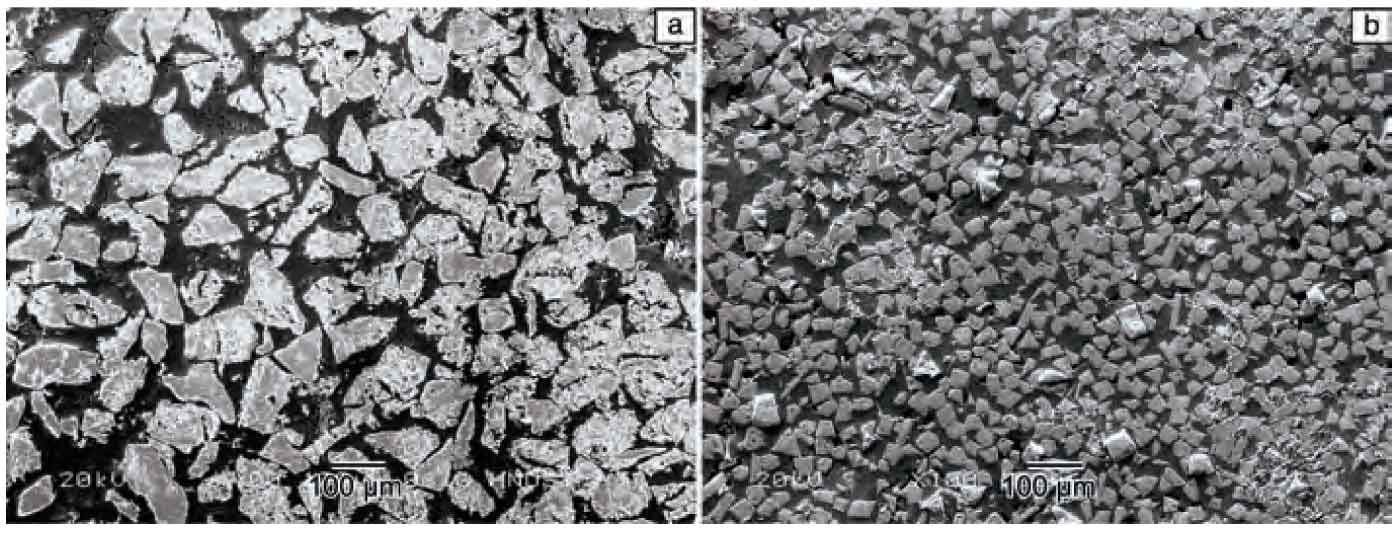
The method of remelting metal can effectively control the distribution and size of ceramic particles, so that the volume fraction of external particles reaches 65%~70%, the number of ceramic particles dissolved in the matrix increases, the undissolved particles are uniformly distributed on the outer surface of the roller ring, and the maximum hardness and impact toughness of the composite materials reach 63 3HRC and 2 8~3.2 J/cm ^ 2, the hardness and impact toughness of the inner substrate are 46HRC~47HRC and 6 7 ~ 6. 9 J/cm ^ 2, the impact toughness of the transition zone is lower than that of the original matrix.
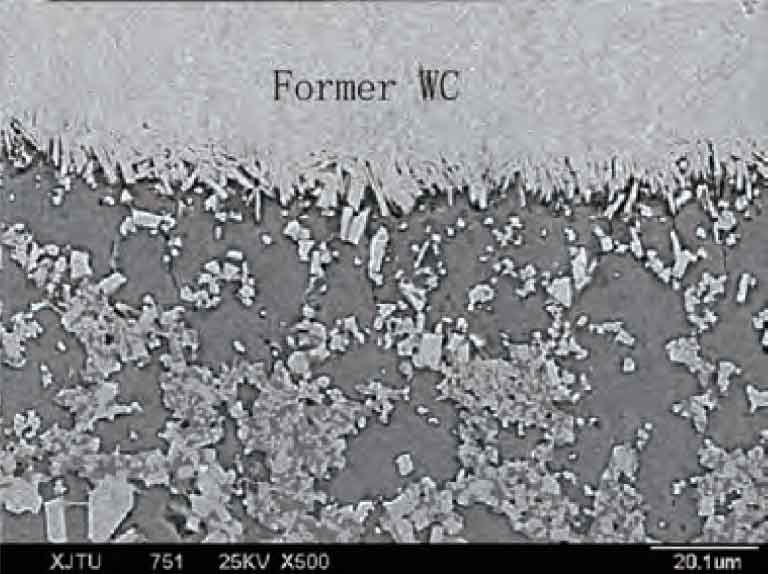
The performance of metal matrix ceramic composites depends to a large extent on the combination of ceramic and matrix interface, and a good metallurgical interface can greatly improve the comprehensive performance of the workpiece. Gao Yimin and others characterized the interface of WC particles reinforced iron matrix composites and found that a good metallurgical bonding interface was formed between WC particles and the matrix (Fig. 2). The composite was free of cracks, pores and other defects, and small carbide particles were formed around the WC particles. The abrasive wear performance of the composite was 7. 5% of that of ordinary high chromium cast iron 23 times. The wear resistance of metal matrix ceramic composites is also greatly improved compared with ordinary alloys. Generally, the wear performance of materials is explored through three-body wear test. Through previous research and application, it is found that the wear resistance of ceramic particle reinforced metal matrix composites is more than three times that of ordinary alloys.