Steel casting offers cost-effective production solutions for a wide range of industries. This article explores the advantages of steel casting in maximizing efficiency and cost-effectiveness, highlighting its application versatility, material properties, and production benefits.
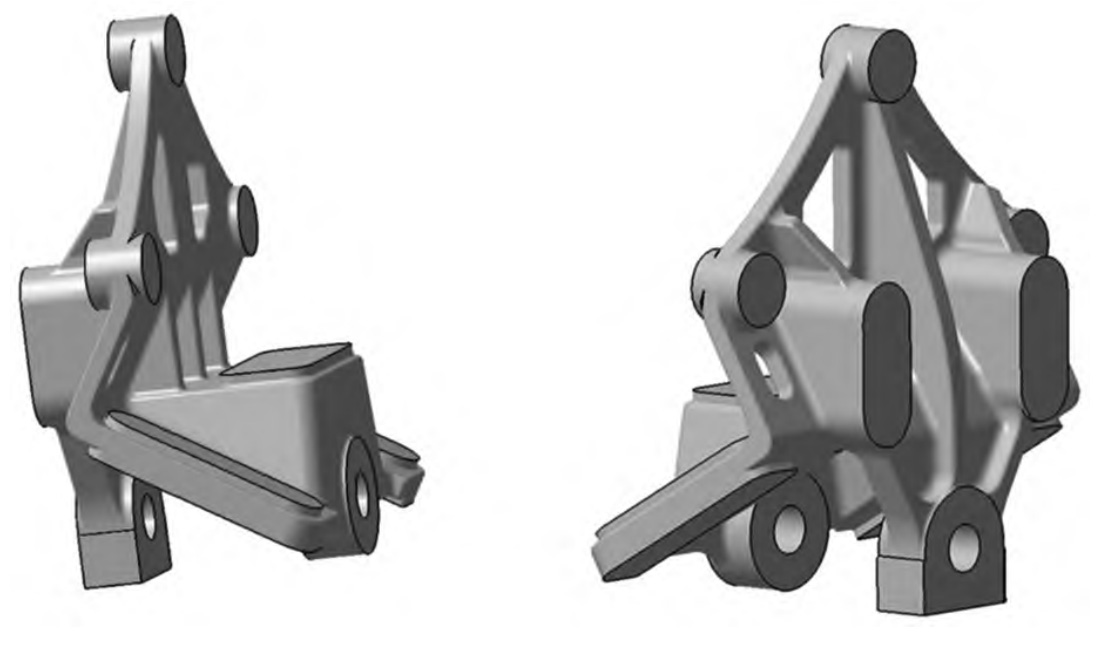
- Versatility in Application: Steel casting provides versatility in meeting the diverse needs of various industries. From automotive and aerospace to construction and energy sectors, steel castings find applications in critical components such as engine parts, turbine blades, structural elements, and machinery components. The adaptability of steel casting allows manufacturers to address different industry requirements efficiently.
- Material Properties: Steel castings exhibit exceptional mechanical properties that contribute to their cost-effectiveness. High strength, toughness, and wear resistance make steel castings suitable for demanding applications, reducing the need for frequent replacements and minimizing downtime. The material properties of steel castings ensure long-lasting performance, resulting in cost savings over the product’s lifespan.
- Complex Geometries and Design Flexibility: Steel casting enables the production of complex geometries and intricate designs. With advanced casting techniques such as investment casting or lost wax casting, manufacturers can achieve precise shapes and intricate details that are difficult to manufacture using other methods. This design flexibility allows for optimized component functionality, reduced assembly requirements, and increased overall efficiency.
- Efficiency in Production Processes: Steel casting offers streamlined production processes that contribute to cost-effectiveness. The ability to create near-net shape castings reduces material waste and machining costs, minimizing overall production expenses. Furthermore, steel casting allows for batch production, enabling efficient manufacturing of multiple components simultaneously, saving time and resources.
- Cost-Efficient Material Utilization: Steel casting optimizes material utilization by using only the necessary amount of metal required for a specific component. This efficient use of raw materials helps minimize material costs and waste, resulting in cost-effective production. Additionally, the ability to recycle and reuse steel casting materials further enhances the sustainability and cost-effectiveness of the manufacturing process.
- Quality Control and Consistency: Steel casting undergoes rigorous quality control measures, ensuring consistent and reliable results. Quality assurance processes such as non-destructive testing, dimensional inspection, and metallurgical analysis guarantee the integrity and performance of the castings. Consistent quality minimizes the risk of defects, rework, and product failures, leading to improved efficiency and cost savings.
Steel casting offers cost-effective production solutions by leveraging its versatility, material properties, and production benefits. From complex geometries and design flexibility to efficient material utilization and streamlined production processes, steel casting maximizes efficiency while reducing costs. By providing reliable, high-quality components that require minimal maintenance and replacements, steel casting contributes to long-term cost savings for industries across the board.