Disc braking is one of the key technologies for high-speed train braking and an important guarantee for the safe and reliable operation of high-speed trains. The most important function of the brake disc is to absorb braking kinetic energy and convert it into heat energy to dissipate into the air. Therefore, during the braking process, the brake disc material should have a stable organizational structure and good mechanical properties. With the rapid development of high-speed trains, cast steel brake discs and forged steel brake discs have been widely used in various types of high-speed trains. France used Cr Mo-V series low alloy forged steel brake discs on TGV-A trains, which showed good comprehensive performance during the braking service of high-speed trains at a speed of 300 km/h. Japan widely uses Ni Cr Mo low alloy forged steel brake discs on high-speed trains on the Shinkansen, which can meet the braking requirements of trains at a speed level of 260 km/h. The Ni Cr Mo low alloy forged steel brake disc material was applied in the early Harmony high-speed trains in China, and currently, the brake discs used in high-speed trains in China are generally made of Ci Ni Mo V low alloy steel material. Scholars have conducted experimental research on the microstructure and mechanical properties of cast steel brake discs and forged steel brake disc materials for rail vehicles. The research shows that brake disc materials have excellent plasticity, strength, and toughness, and the mechanical properties of brake disc materials are closely related to their microstructure characteristics.
During service, brake discs are subjected to complex thermal mechanical loads, and repeated cold and hot cycles may cause changes in the microstructure of brake discs, further leading to performance changes. Research has shown that during high-speed emergency braking, the temperature rise of the friction surface of the brake disc can exceed the phase transition temperature of the material, which can cause the initial tempered martensite structure of the brake disc material to undergo transformation during the braking heating and subsequent cooling processes. When the microstructure transformation products on the friction surface of the brake disc cause uneven distribution of the mechanical properties of the disc material, and even reduce the mechanical properties, micro cracks are easily formed on the disc surface and fatigue propagation occurs in the subsequent process, seriously affecting the service life of the brake disc and the safety of train operation. Therefore, the author of this article measured the CCT curves of low alloy steel materials for cast steel brake discs and forged steel brake discs used in high-speed trains, and obtained the continuous cooling transformation curves of low alloy steel materials for brake discs. This not only clarifies the critical transformation temperature and critical cooling rate of each structure of cast steel brake disc and forged steel brake disc materials, but also provides a basis for analyzing and determining the microstructure transformation products of brake disc materials.
1.Test materials and methods
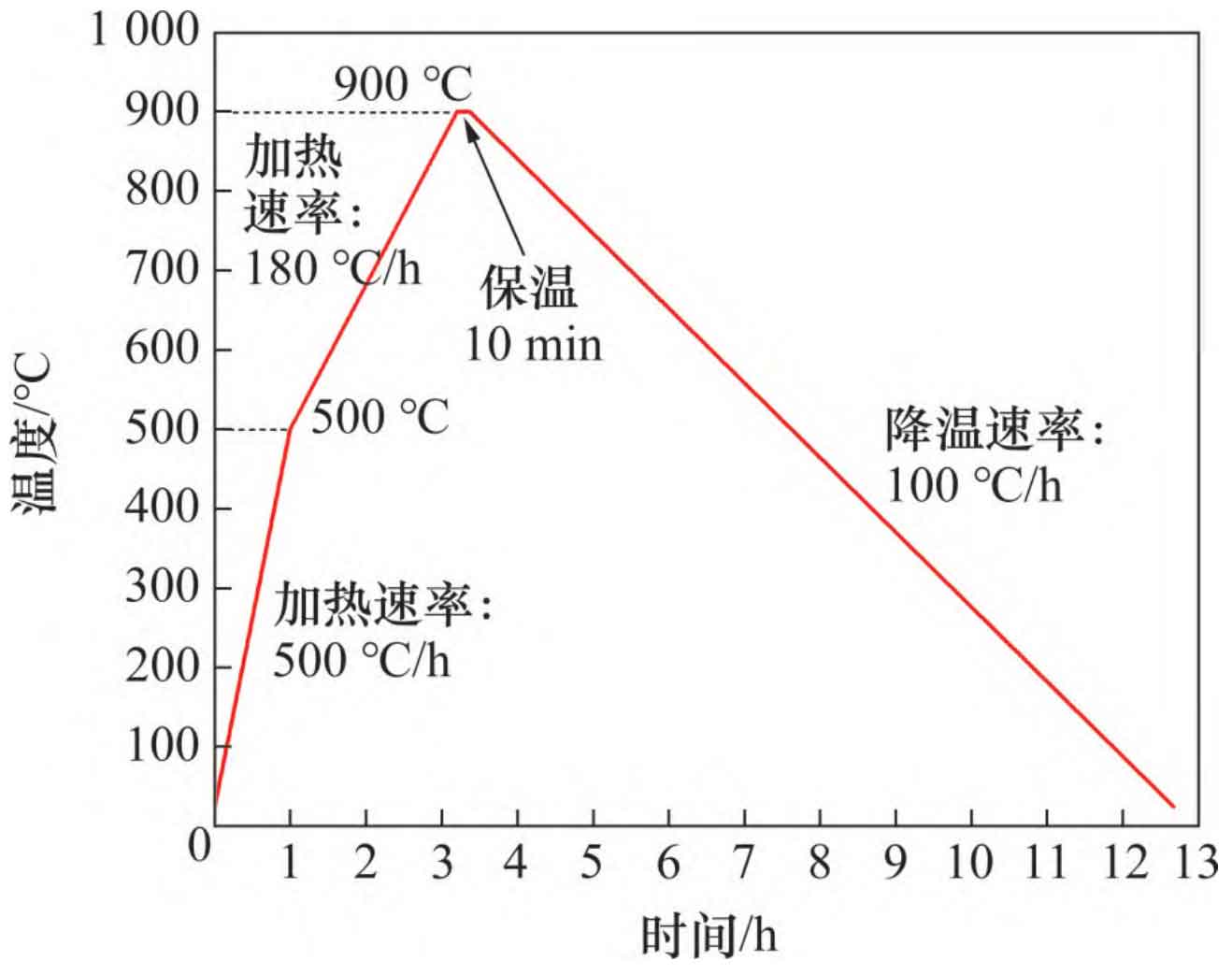
The experimental materials are cast steel brake discs and forged steel brake discs made of low alloy steel for high-speed trains. The chemical composition of the materials is shown in Table. The continuous cooling transformation curve of brake disc materials was tested using the thermal expansion method. Firstly, the sample was installed on a DIL 805L thermal expansion instrument for static critical point determination. Referring to the standard YB/T 5127-2018, the sample was heated from room temperature to 500 ℃ at a heating rate of 500 ℃/h, and then changed to a heating rate of 180 ℃/h to 900 ℃. The sample was kept for 10 minutes to achieve complete austenitization, Cool the sample to room temperature at a cooling rate of 100 ℃/s, measure the expansion curve of temperature rise and fall, and determine the critical temperature point. The temperature control curve is shown in Figure 1. Subsequently, reference standard YB/T 5128-2018 was used to determine the CCT curve. The sample was heated at a heating rate of 10 ℃/s to 900 ℃ and held for 10 minutes. Then, the sample was cooled to room temperature at cooling rates of 0.2, 0.5, 1.0, 2.0, 5.0, 10.0, 20.0, and 50.0 ℃/s or higher. The temperature control curve is shown in Figure 2. The expansion curve of the sample was tested and recorded on the testing machine under different cooling rate conditions, Obtain the temperature of the critical transition point using the tangent method.
Sample | C | Si | Mn | P | S | Cr | Ni | Mo | V |
Cast steel brake discs | 0.26 | 0.58 | 1.04 | 0.014 | 0.011 | 0.90 | 1.00 | 0.55 | 0.10 |
Forged steel brake discs | 0.30 | 0.40 | 0.75 | 0.009 | 0.007 | 1.20 | 0.40 | 0.65 | 0.30 |
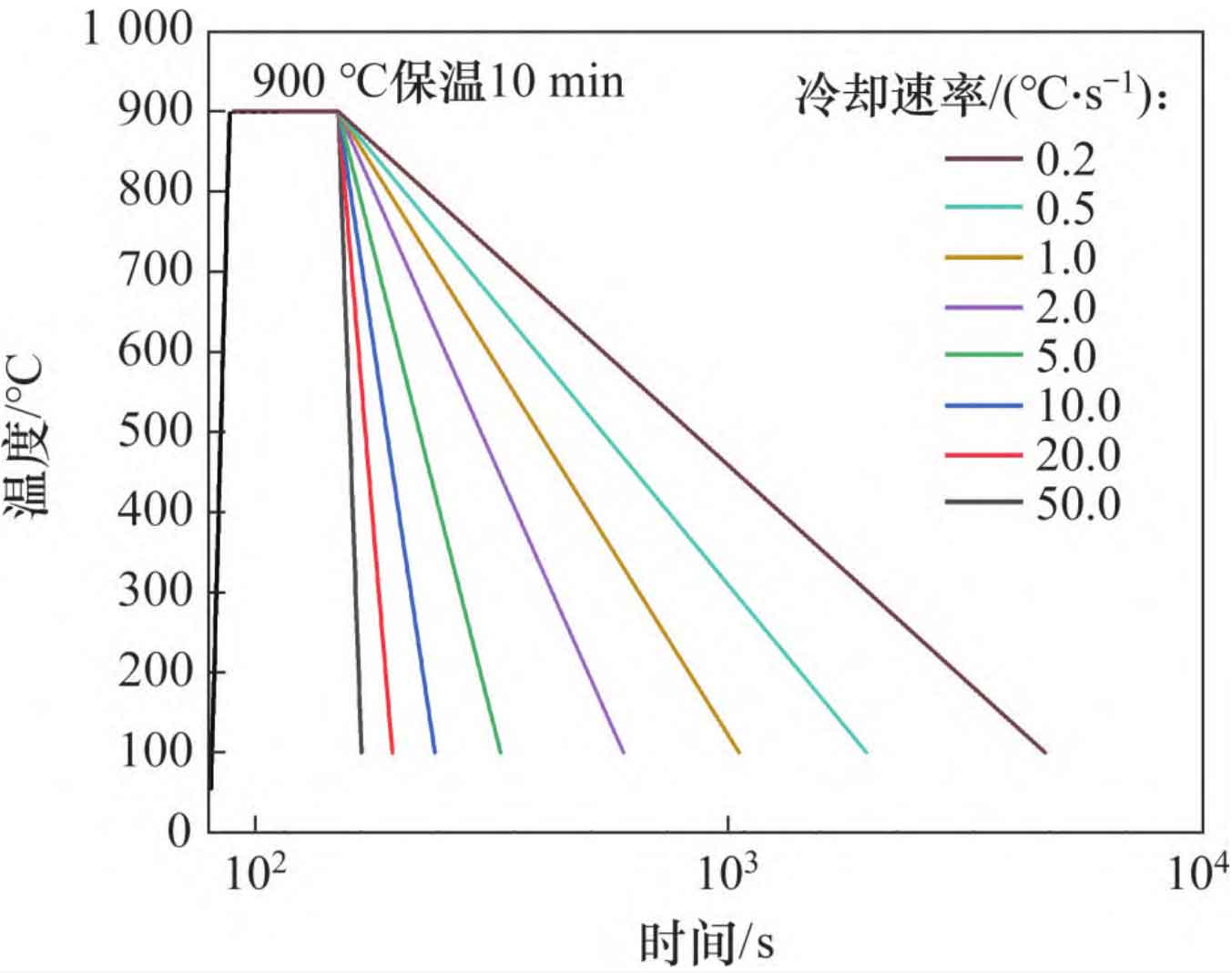
A cylindrical specimen with a diameter x length of 4 mm x 10 mm was used in the experiment. When the cooling rate was greater than 10 ℃/s, a through-hole with a diameter of 2 mm was machined in the center of the specimen to achieve rapid cooling. The specimen size is shown in Figure 3. After the thermal expansion test is completed, the
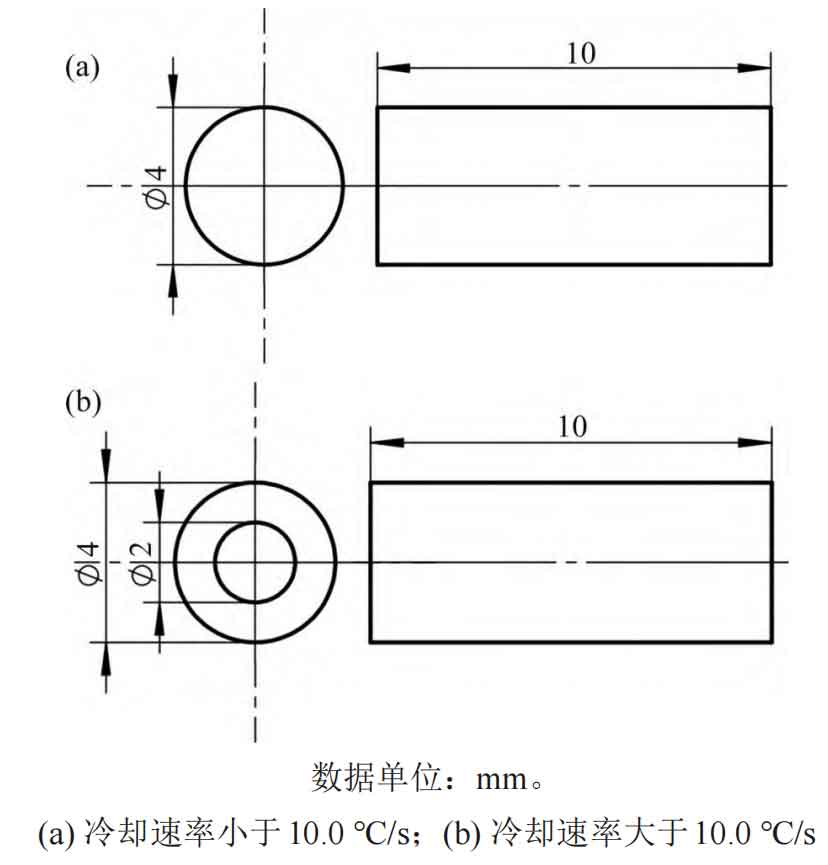
Prepare the sample into a metallographic sample and corrode it with a volume fraction of 4% nitric acid alcohol solution in ZEISS Axio Vert Observation of the microstructure of brake disc materials under different cooling rates using A1 optical microscope and ZEISS Gemini 500 scanning electron microscope, and testing of the hardness of each sample using VTD-512 microhardness tester.
2. Experimental results and discussion
2.1 Organizational transition temperature
According to the data output from the thermal expansion instrument, the austenite transformation (AC3) temperature of the cast steel brake disc material is 847 ℃, and the initial temperature of martensitic transformation (Ms) is 347 ℃; The AC3 temperature of forged steel brake disc material is 862 ℃, and the Ms temperature is 368 ℃. The AC3 temperature and Ms temperature of forged steel brake disc material are higher than those of cast steel brake disc material.
2.2 Organizational characteristics corresponding to different cooling rates
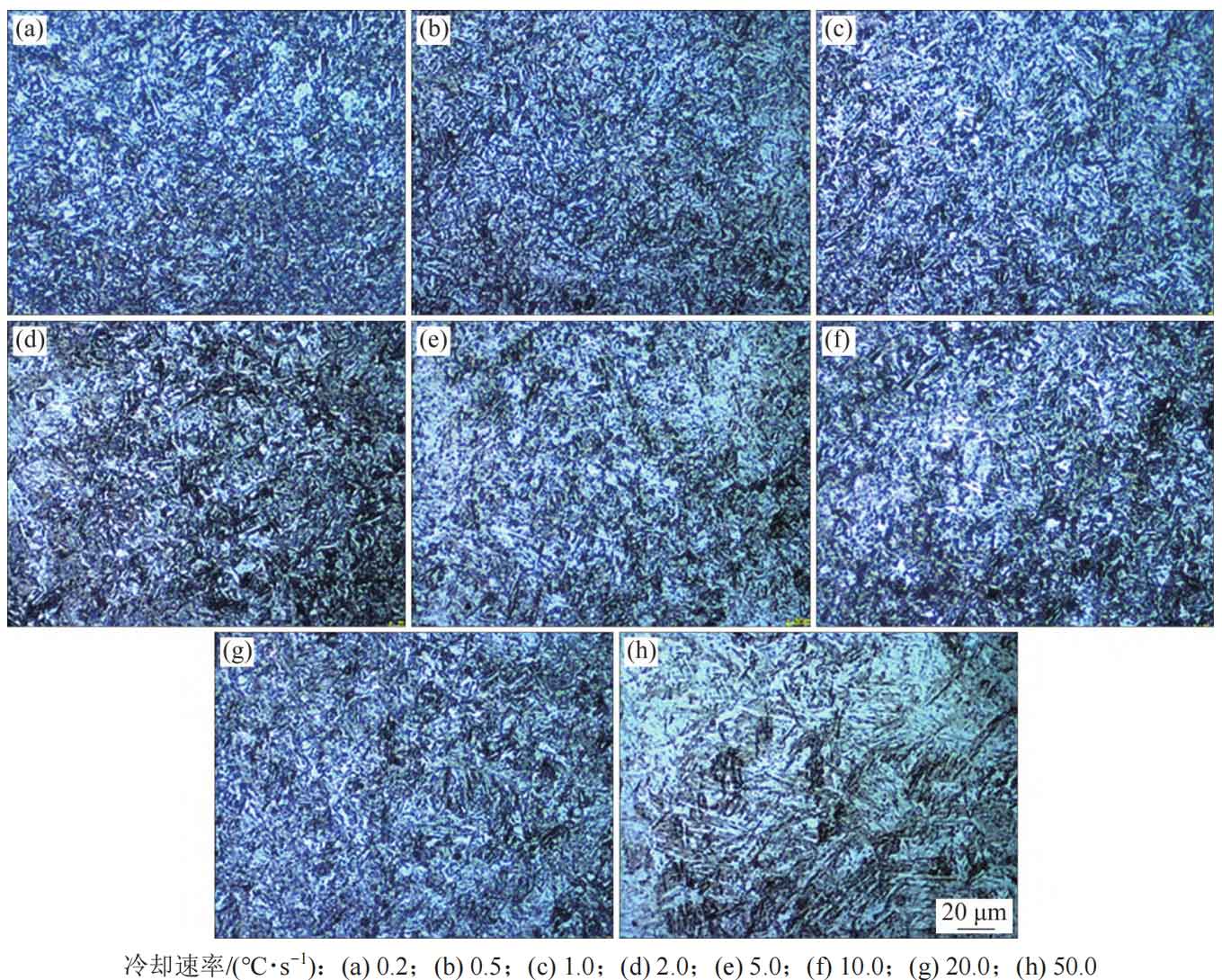
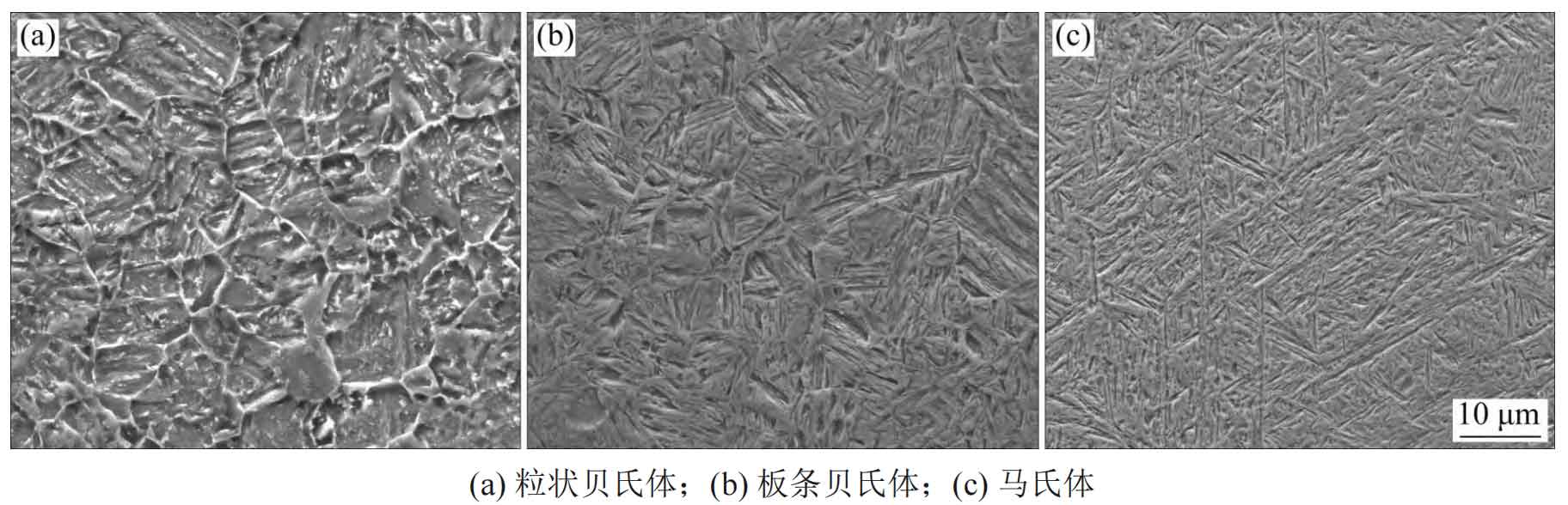
Figure 4 shows metallographic photos of cast steel brake disc materials continuously cooled to room temperature at different rates, while Figure 5 shows scanning electron microscopy photos of different microstructures. From Figures 4 and 5, it can be seen that the cast steel brake disc material mainly undergoes bainite transformation and martensite transformation when cooled at different cooling rates. When the cooling rate is 0.2 ℃/s, the microstructure of the cast steel brake disc specimen is granular bainite (GB); When the cooling rate is 1.0~2.0 ℃/s, the microstructure is granular bainite (GB) and lath bainite (LB); When the cooling rate is 5.0~20.0 ℃/s, the metallographic structure is lath bainite (LB) and martensite (M), and the number of Flat noodles martensite gradually increases with the increase of the cooling rate; When the cooling rate is greater than 20.0 ℃/s, the microstructure changes no longer significantly, and the corresponding structure is mainly lath martensite.
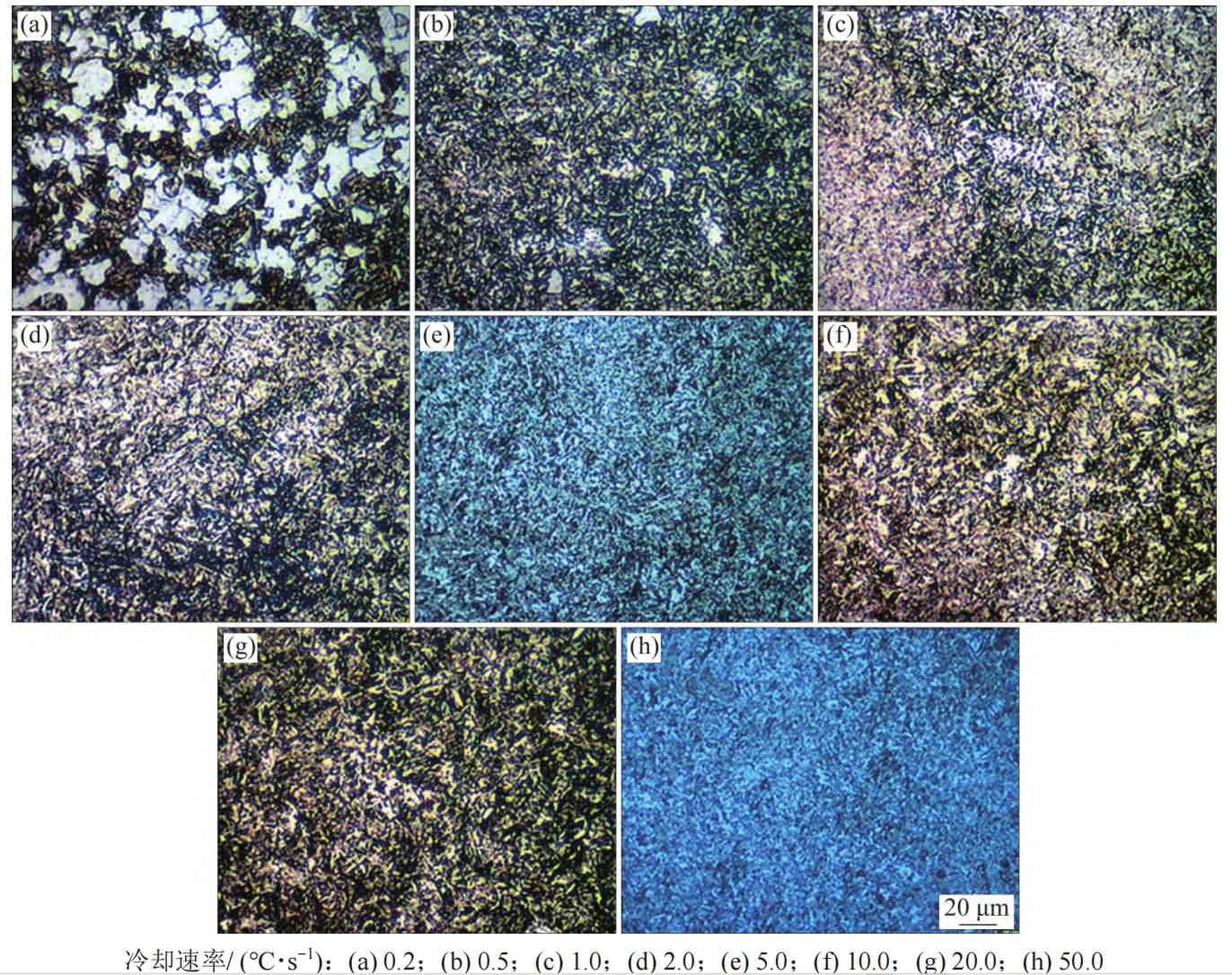
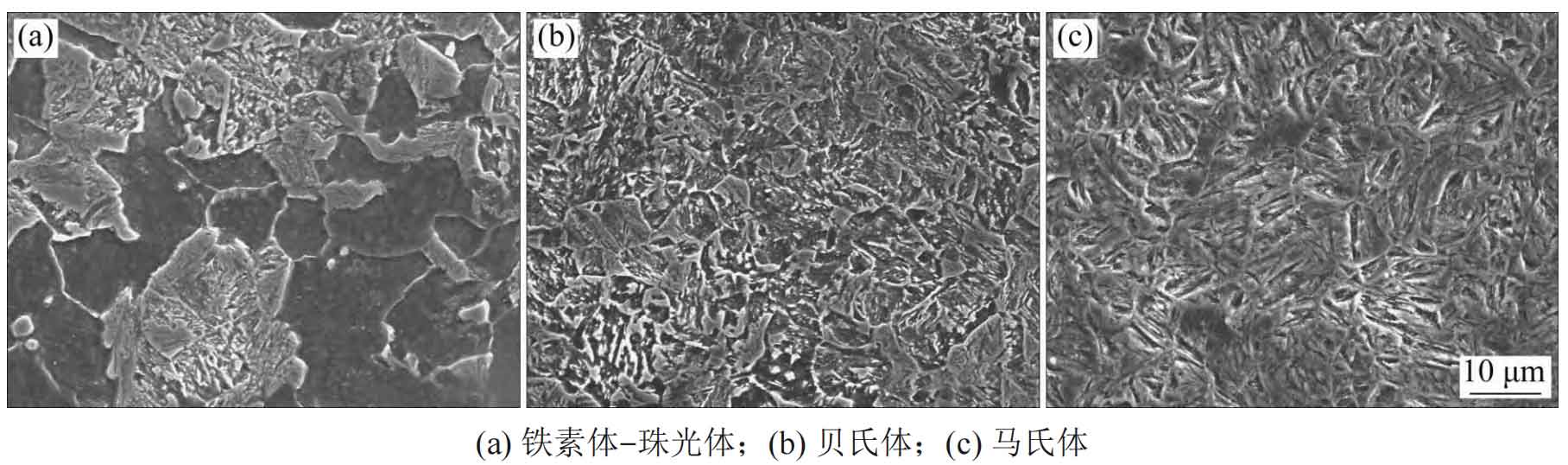
Figure 6 shows metallographic images of forged steel brake discs continuously cooled to room temperature at different rates, and Figure 7 shows scanning electron microscopy images of different microstructures. It can be seen from Fig. 6 and Fig. 7 that the pearlite zone of forged steel brake disc material is small, ferrite pearlite structure will be formed at a cooling rate of 0.2 ℃/s, and a small amount of bainite structure can be seen. When the cooling rate is between 1.0 and 20.0 ℃/s, the metallographic structure is a mixed structure of bainite and Flat noodles martensite, and when the cooling rate is greater than 50.0 ℃/s, martensite structure will be formed.