Metallographic structure and scanning electron microscope observation of the alloy select the parts with serious corrosion and take samples along the direction perpendicular to the axis of the test bar. The results of metallographic analysis, scanning electron microscope analysis and micro zone composition energy spectrum analysis of the structure are shown in the figure.
According to the metallographic photo a, section morphology E and scanning image C and D of metallographic samples of cast parts, there are a large number of cavities in the edge structure, with different diameters and rough inner wall. The contrast difference between the matrix structure inside and around the cavity is obvious, which shows that the cavity and surrounding tissues may contain different components. There are precipitates at the grain boundary and in the crystal of the middle structure (see Fig. b), the structure is relatively uniform, and no serious segregation of impurities at the grain boundary is found. As can be seen from figure C, the cavity and inclusion are located within 5mm from the edge to the inside along the diameter direction. In order to further understand the difference between the internal and external components of the empty hole, the energy spectrum analysis is carried out for the parts a, B, C, D and e shown in Figure D and the points at matrix F. The results are shown in the table.
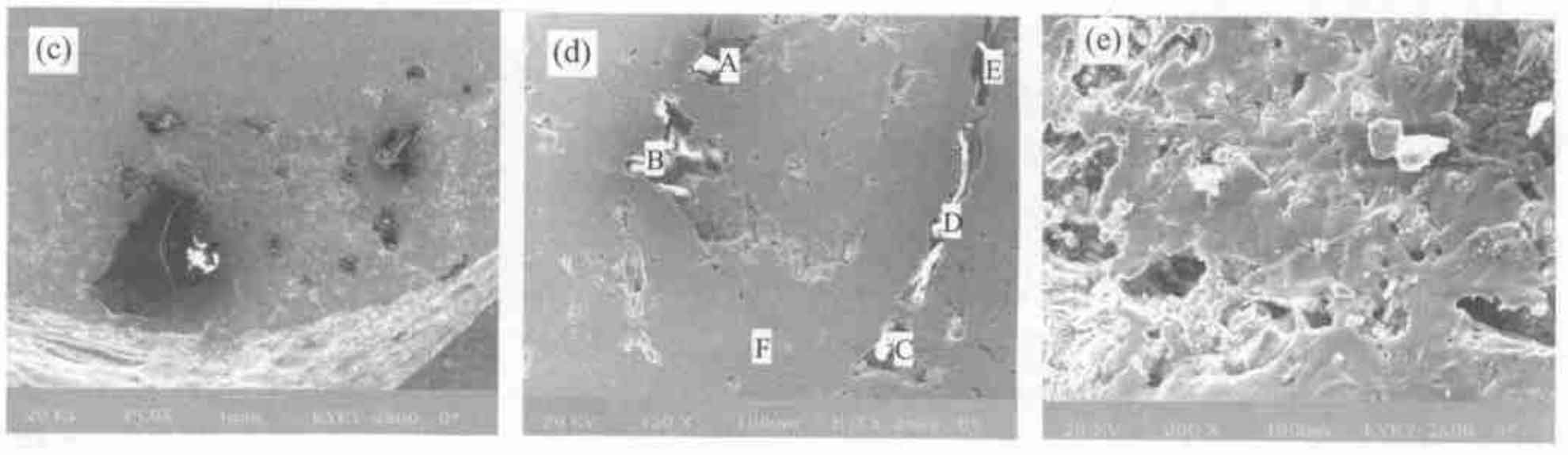
(d) Enlarged image of defect area of casting part
(e) SEM of the section of the test bar after sawing along the diameter direction
The table shows that no other impurity elements are found in the matrix composition. A. The inclusions at B, C, D and e contain impurity elements such as Ca, Cl, s and Si, and the content of Cl and s in these impurity elements is relatively high. The types of impurity elements are consistent with the elements contained in the corrosion products on the surface of cast parts. Therefore, it can be considered that the inclusions in the interior (near the edge) of cast parts and the corrosion products on the surface are the same type of substances, which may be caused by the same reasons. In other words, this defect contains a variety of impurity elements such as Ca, Cl, s and Si, and the defects are distributed within about 5mm near the surface layer.