The microhardness of lzqt600-3 ductile iron profile was tested under the optimal scheme of nitrocarburizing state in three parts. The effective hardened layer depth of the sample was obtained by hardness distribution gradient and effective hardening depth limit. The figure shows the micro Vickers hardness metallography and hardness gradient diagram of three parts nitrocarburizing sample section of lzqt600-3 ductile iron profile. It can be seen from the figure that under the optimal nitrocarburizing process, the hardness gradient of the three parts of the sample cross-section decreases gradually from the surface to the core, which is due to the formation of strengthening phase on the surface of the sample after nitrocarburizing treatment, and its hardness is greater than that of the matrix, so the hardness value remains higher than that of the matrix at a distance from the surface. Compared with the matrix hardness, the hardness of the nitrided edge sample is 914.4 hv0.25, and the effective depth of the hardened layer is 119.43 μ m; the hardness of the hardened layer of the nitrocarburized 1 / 2R sample is 1025.86 hv0.25, and the effective depth of the hardened layer is 55.5 μ m; the hardness of the hardened layer of the nitrocarburized core sample is 1109.66 hv0.25, and the effective hardening depth is 117.38 μ M.
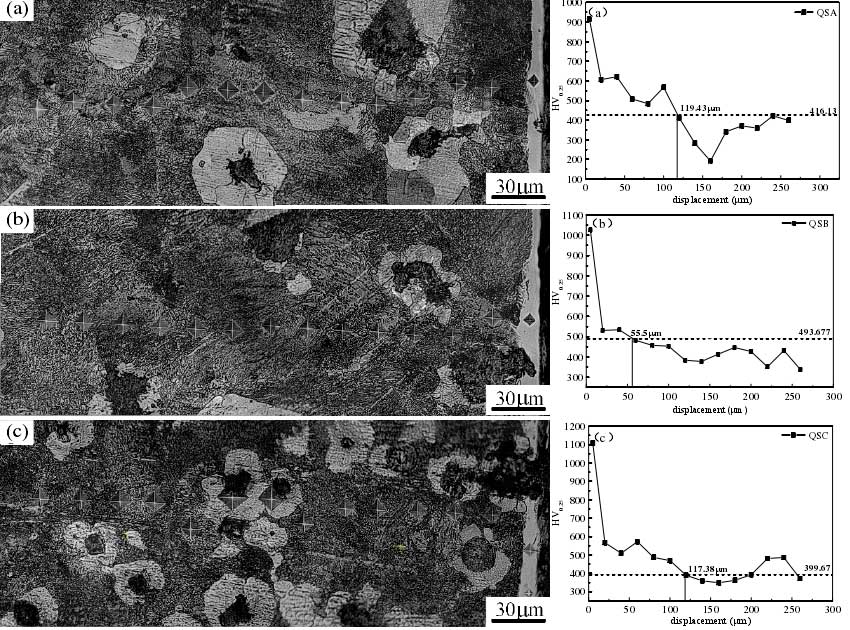
Lzqt600-3 after nitrocarburizing with the optimal scheme The hardness of hardening layer in three parts of ductile iron profile is different from that of effective hardening layer. This is due to the fact that the cooling rate from edge to core gradually decreases when horizontal continuous casting process is used to manufacture profiles. The molten iron forming the core takes the longest time to solidify into the profile, and the carbon in the matrix is easier to diffuse into graphite. Therefore, the content of ferrite in the core is lower and the ferrite content at the edge is higher. However, due to its own gravity, the liquid core is higher during solidification, so the microstructure at 1 / 2R below the profile is smaller than that at the edge, and the ferrite content is the highest. After nitrocarburizing, the carbon element is more difficult to penetrate at the lower 1 / 2R compared with the edge and core, so the effective hardening depth at 1 / 2R is the minimum.
The results show that the surface hardness of the three different parts of the samples treated by the optimal nitrocarburizing scheme is significantly improved compared with that of the as cast samples. Compared with the samples in the orthogonal experiment, the surface hardness and effective hardened layer depth of the samples under the optimal scheme are increased slightly. The analysis may be due to the small range of experimental process parameters selected in this project, and in the process of the experiment Due to the lack of nitrocarburizing treatment in oxygen free environment, slight oxidation occurs on the surface of the layer, which leads to the performance degradation.