
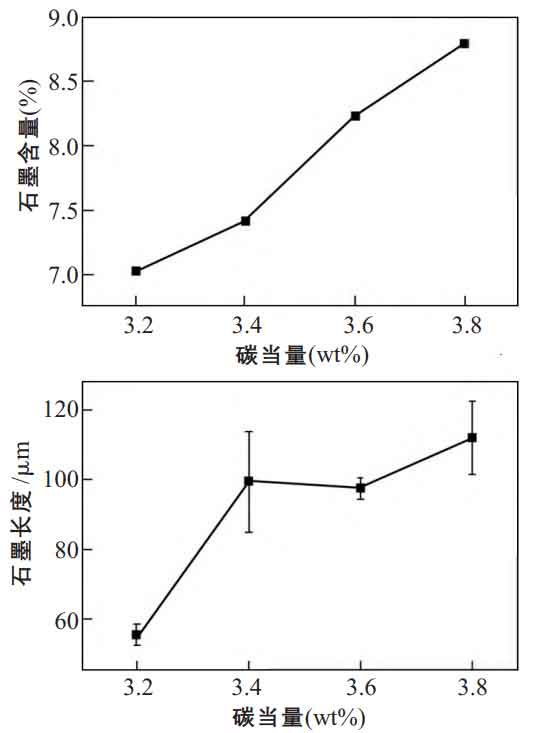
Graphite in gray cast iron is a weak phase, and its strength is close to zero. If there is a large amount of graphite in gray cast iron, the graphite sheet is flat and coarse, and the graphite tip is sharp, the mechanical properties of gray cast iron will be significantly weakened. Therefore, in order to cast high-strength gray cast iron, the graphite morphology should be controlled first. Figure 1 shows the graphite morphology of gray cast iron with different carbon equivalent. Compared with the national standard gb/t7216-2009, it can be concluded that when CE is 3.2%, the graphite of gray cast iron is distributed in the direction of e-type graphite; When CE is 3.4%, the primary coarse straight flake graphite is formed in the graphite of gray cast iron, and the graphite type is e+c; When CE is 3.6%, the graphite is short and coarse, e+c type graphite; When CE is 3.8%, the graphite is directionless and has a certain amount of primary coarse straight flake graphite, which is C-type graphite. It can be seen from Figure 1 that the bending degree of graphite with different carbon equivalent is also gradually changing, and the bending degree of graphite gradually decreases with the gradual increase of carbon equivalent. The influence of different carbon equivalent on graphite content and length of gray cast iron was studied by using software. It can be seen from Figure 2 that when the carbon equivalent is increased from 3.2% to 3.8%, the graphite content and length in gray cast iron gradually increase, and when the carbon equivalent is 3.2%, the graphite length of gray cast iron is 55.38 μ m. When the carbon equivalent is 3.8%, the graphite length is 111.93 μ m. Increased by 102%.

Figure 3 shows the microstructure of gray cast iron with different carbon equivalent after corrosion. It can be seen that the matrix of grey cast iron is mainly graphite and pearlite, and there is no large amount of ferrite precipitation, because ferrite is the weak phase in the cast iron material. If the ferrite content is too much or there is massive precipitation, the mechanical properties of grey cast iron will be greatly weakened, making it unable to meet the actual use requirements. By testing the pearlite content in different grey cast iron, it is found that the pearlite content of grey cast iron with carbon equivalent of 3.2% ~ 3.8% is more than 95%. This is because the addition of copper, molybdenum, tin and other elements promotes the formation of pearlite and improves the strength and toughness of grey cast iron. See the formula for the calculation of grey cast iron quality parameters.
Eutectic SC:
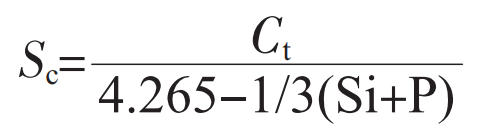
Where: CT is the actual carbon content in cast iron,%; Si is the actual silicon content in cast iron,%; P is the actual phosphorus content in cast iron,%. SC should be controlled within 0.7 ~ 1.0, and the casting performance of gray cast iron is the best.
Maturity:
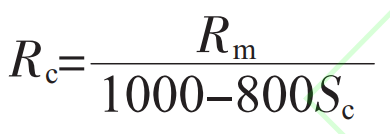
Where, RM is the measured tensile strength, MPa. The RC value should be controlled within 0.9 ~ 1.20 as far as possible. At this time, under the relatively high eutectic degree, the strength will be increased by further optimizing the smelting and casting technology.
Hardness:
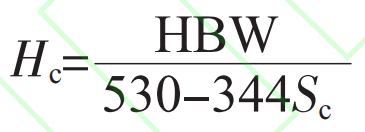
Where: HBW is Brinell hardness, MPa. When the hardening degree is controlled between 0.8 and 1.2, the cutting performance of gray cast iron is the best.
Quality coefficient:
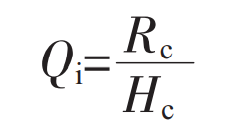
Qi=1.0 ~ 1.4 is the most ideal value range. The higher the quality coefficient is, the higher the material strength is. At the same time, the casting performance and cutting performance are also ideal.
By testing the quality of casting samples, the actual parameters measured are brought into the formula to obtain the table. It can be seen that the eutectic degree (SC) of gray cast iron increases with the increase of carbon equivalent; The maturity (RC) and hardness (HC) also increased gradually when the carbon equivalent was 3.2% to 3.6%, but decreased when the carbon equivalent was 3.8%; The quality coefficient (QI) is always 1.05 when the carbon equivalent is 3.2% ~ 3.6%, and the quality is relatively stable. When the carbon equivalent is 3.8%, the quality of gray cast iron decreases. It can be seen from the formula that this is because the high carbon content of 3.8% carbon equivalent grey cast iron significantly reduces the mechanical properties of the material, especially the tensile strength decreases from 351.6mpa to 251.1mpa, which leads to the decline of the maturity (RC) of grey cast iron and affects the quality coefficient of 3.8% carbon equivalent grey cast iron.
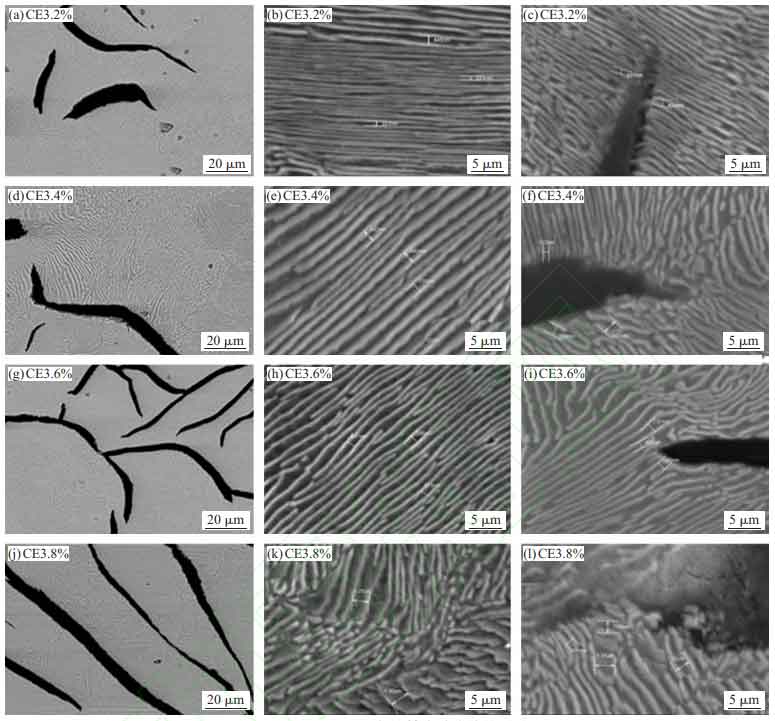
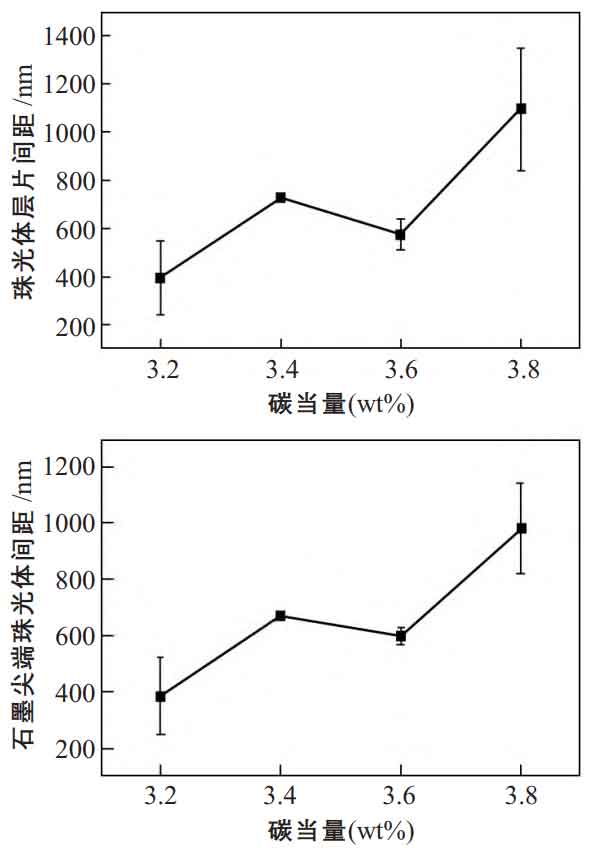
Pearlite, as a strengthening material in gray cast iron, plays a significant role in improving the properties of the material. The results show that the continuous and uniform distribution of pearlite can effectively improve the properties of gray cast iron. Figure 4 shows the scanning photos of gray cast iron with different carbon equivalent. It can be seen from Fig. 4 (a), (d), (g) and (J) that when the carbon equivalent is 3.2%, the pearlite in gray cast iron is evenly distributed without obvious sparse or dense places. With the gradual increase of carbon equivalent, the pearlite in gray cast iron appears dense or sparse places, and the uneven distribution affects the stability of material properties. Figure 5 is obtained through software test. It can be seen that the pearlite lamellar spacing in gray cast iron increases gradually with the increase of carbon equivalent. When the carbon equivalent is 3.2%, the pearlite lamellar spacing is 397 nm; When the carbon equivalent is 3.4%, the pearlite lamellar spacing is 670 nm; When the carbon equivalent is 3.6%, the pearlite lamellar spacing is 723 nm; When the carbon equivalent is 3.8%, the pearlite lamellar spacing distribution is very uneven, and the pearlite length is also uneven. The average pearlite spacing is 1175 nm. The results show that when the carbon equivalent is 3.2%, the pearlite spacing is the smallest, the pearlite distribution is uniform, and the material performance is the best.
In cast iron, because the strength of graphite is close to zero, it will crack before the matrix under external force. Then, the crack propagates into the matrix until the next graphite crack, which eventually leads to the fracture of the casting. Therefore, the higher the carbon content in gray cast iron, the lower the mechanical properties. Pearlite, as a strengthening agent in gray cast iron, is an obstacle to crack propagation. The distribution of pearlite at the graphite tip determines the mechanical properties of gray cast iron. It can be seen from Figure 4 (c), (f), (I) and (L) that with the increase of carbon equivalent, the distribution of pearlite at the graphite tip becomes extremely uneven, and the shape of pearlite also changes from long order to short disorder, which leads to the decline of material properties. By testing the pearlite lamellar spacing around the graphite tip, it is found that with the increase of carbon equivalent, the pearlite at the graphite tip becomes shorter and thinner. When the carbon equivalent increases from 3.2% to 3.8%, the pearlite lamellar spacing around the graphite increases from 385.0nm to 936.3 nm, an increase of 143.1%. This is also the main reason for the decline of mechanical properties of materials.