In order to better analyze the microstructure of the forming alloy, the slurry structure of the alloy was analyzed firstly. Fig. 1a and b show the microstructure of nz30k alloy slurry without EMS and EMS respectively. In the slurry without electromagnetic stirring (Fig. 1a), the primary particles and the solidified particles are connected with each other, which is difficult to distinguish. After the slurry is stirred by electromagnetic stirring (Fig. 1b), the ideal semi-solid structure of fine and round primary particles uniformly suspended in liquid phase can be obtained, and the particles are obviously refined. The particle size less than 30 μ M can be regarded as solidification of liquid phase. In addition, at position B (Fig. 2) of the rheo squeeze casting part, the solidification rate of the slurry is faster and the semi-solid structure is almost maintained. However, during the process of slurry transferring to the mold cavity and filling, the primary particles grow up while the slurry solidifies. At this time, the solid fraction of the alloy is about 50%, which is suitable for rheo squeeze casting.
Figure 3 shows the microstructure of nz30k alloy in rheo squeeze casting under different pressures. When no pressure is applied to the slurry (Fig. 3a), some subgrains can be seen inside the grains, which gradually disappear with the increase of pressure (Fig. 3b, C and D). With the increase of pressure, primary particles gradually connect with each other, and the shape of secondary primary particles becomes irregular. This indicates that plastic deformation occurs in the adjacent particles, and the degree of deformation increases with the increase of pressure. When the pressure increases from 0 MPa to 40 MPa, the average particle size decreases significantly from 58 μ m to 42 μ m, and when the pressure increases to 80 MPa and 120 MPa, the grain size gradually decreases to 41 μ m and 39 μ m, respectively (Fig. 4). The shape coefficient of primary particles first increases and then decreases with the increase of pressure, and its value ranges from 1.11 to 1.26. In addition, the density of the alloy increases from 1.7893 g / cm3 to 1.8066 g / cm3 when the pressure increases from 0 MPa to 40 MPa. When the pressure increased to 80 MPa and 120 MPa, the density remained unchanged, which were 1.8075 g / cm3 and 1.8077 g / cm3, respectively.
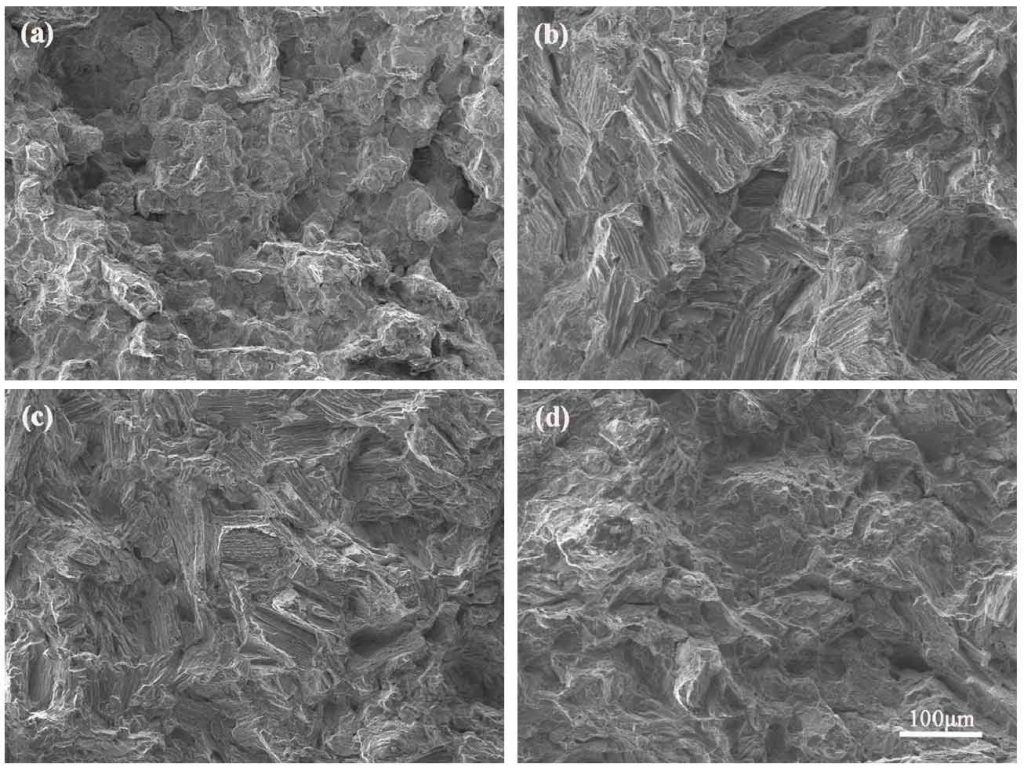
MPa, (b) 40 MPa, (c) 80 MPa and (d) 120 MPa. The insets in (a), (d) are the corresponding high-magnification images by SEM.
In addition, a large eutectic phase can be observed at the grain boundary when the pressure is 0 MPa (Fig. 3a). According to EDs results, the eutectic phase is mainly composed of Mg, Nd and a small amount of Zn. When the pressure increases from 0 MPa to 120 MPa, the eutectic phase transformation becomes smaller and smaller (Fig. 3D), and the content of Nd and Zn in the eutectic phase decreases, and the eutectic phase inside the particles disappears. This indicates that the solid solubility of Nd and Zn in α – Mg particles increases with the increase of pressure.
Figure 5 shows the XRD patterns of nz30k alloy formed under different pressures. It can be seen from the figure that the microstructure of nz30k alloy formed under different pressures is still composed of α – Mg matrix and MG1
Nd eutectic phase. The lattice constant of α – Mg decreases with the increase of pressure. In nz30k alloy, the content of Zn is much lower than that of Nd. Therefore, the lattice constant of α – Mg reflects the solution tendency of Nd.
According to the above analysis, under the existing experimental conditions, the solid solution of Nd atoms will lead to the decrease of the lattice constant of α – mg. This result is consistent with that of Fang et al and Li et al. With the increase of pressure, the solid solubility of rare earth (CE and LA) or SM in α – Mg increases and the lattice constant decreases. In addition, as described above, the alloy slurry is formed under pressure, and the adjacent particles undergo plastic deformation. According to the formula, the dislocation density of the alloy can be calculated. With the increase of pressure from 0 MPa to 120 MPa, the dislocation density in the alloy increases from 6.41 × 1011 m-2 to 2.07 × 1013 m-2.
Figure 6 shows the mechanical properties of nz30k alloy by rheo squeeze casting under different pressures. With the increase of pressure, the yield strength and elongation increase, while the tensile strength first increases and then decreases. When the pressure is 80 MPa, the yield strength, tensile strength and elongation of the alloy can reach 116 MPa, 197 MPa and 6.7% respectively, which are 48.1%, 21.4% and 123.3% higher than those of the alloy formed at 0 MPa.
Figure 7 shows the fracture morphology of nz30k alloy formed under different pressures. When the pressure is 0 MPa, some loose structures can be observed on the fracture surface (Fig. 7a). When the applied pressure is 40 MPa, the fracture surface is composed of some cleavage surfaces and eutectic structure. Because the alloy structure is relatively dense at this time, almost no loose structure can be observed (Fig. 7b). In addition, it can be observed that the cleavage planes are interconnected to form a piece, which indicates that the crack may propagate along the secondary solidified particles. In the process of rheo squeeze casting, the secondary solidification particles solidified from liquid phase often become the weakness of alloys due to their weak feeding ability. Therefore, when the specimen is in tension, the crack usually starts along the secondary solidification particles, and the fracture mechanism is mainly intergranular fracture. When the pressure is 80 MPa (Fig. 7C), some dispersed cleavage surfaces and eutectic structures are observed on the fracture surface. These cleavage surfaces are the morphology of primary particles after fracture, which indicates that the fracture mechanism of the alloy changes from intergranular fracture to intergranular and transgranular fracture. When the pressure increases to 120 MPa, severe plastic deformation occurs between particles, and the residual stress is relatively large. Cracks often propagate along these deformed particles, resulting in the decrease of mechanical properties. At this time, it is difficult to observe the cleavage surface on the fracture surface (Fig. 7D).