1. Introduction
Austenitic gray cast iron with high nickel content has excellent corrosion resistance and thermodynamic stability due to the presence of a large amount of Ni. It can obtain a stable austenitic structure at room temperature and is widely used in pump and valve fields such as steam turbine generators, petroleum machinery, and industrial furnaces. However, with the continuous increase in the speed of industrial pumps in recent years, the low strength, hardness, and poor wear resistance of austenitic gray cast iron have led to the service life of products made of this material not meeting expectations.
Glow ion nitriding technology is an effective method to improve the surface and subsurface properties of steel materials. In the ion nitriding process, the workpiece to be treated is heated by the energy of active ions generated by glow discharge as the cathode, and a nitride layer is formed on the workpiece surface through the sputtering effect of gas. It overcomes the disadvantages of long process cycle and large brittleness of the conventional gas nitriding process and has the characteristics of low energy consumption, fast nitriding speed, and good comprehensive performance.
Although the application of ion nitriding technology on cast iron has high research value, current research mainly focuses on traditional cast iron materials, and there are few in-depth studies on the influence of ion nitriding technology on the microstructure and properties of austenitic gray cast iron. Therefore, this paper uses glow ion nitriding technology to strengthen the surface of Ni15Cu6Cr2 austenitic gray cast iron and discusses the influence of ion nitriding technology on the microstructure and properties of Ni15Cu6Cr2 austenitic gray cast iron by analyzing the microstructure, phase structure, and electrochemical tests, revealing the nitriding mechanism of high-nickel austenitic cast iron.
2. Experimental Materials and Methods
2.1 Sample Preparation
The austenitic gray cast iron used in the experiment is of the Ni15Cu6Cr2 grade, and its chemical composition is shown in Table 1. Samples with dimensions of 10 mm × 10 mm × 15 mm were cut by a wire cutting machine and then ground with 240, 400, 800, 1000, 1500, and 2000 grit water abrasive papers successively to make each surface flat. Subsequently, they were polished with 0.5 μm diamond paste and ultrasonically cleaned with acetone and alcohol for 5 minutes to remove oil and dust, and then dried with a blower for standby. The ion nitriding treatment was carried out in an LDMC – 30F touch – screen pulse control type glow ion nitriding and diffusing furnace, and the process parameters are shown in Table 2. After nitriding, some samples were sectioned, mounted, ground, and polished. The etchant for the austenitic gray cast iron samples was 4% nitric acid alcohol, and the etching time was about 10 seconds. After etching, the samples were washed with alcohol and dried.
Element | C | Si | Mn | Ni | Cr | Cu | Fe |
---|---|---|---|---|---|---|---|
Content | 1.0 – 2.8 | 5.5 – 1.5 | 1.0 – 2.5 | 13.5 – 17.5 | 0.5 – 3.0 | ≤ 7.5 | Bal. |
Table 1: Chemical composition of Ni15Cu6Cr2 austenitic gray cast iron (wt.%)
Temperature (℃) | Time (h) | V(N₂)∶V(H₂) | Pressure (Pa) | Voltage (V) |
---|---|---|---|---|
380 | 10 | 1∶3 | 0.4 | 300 |
540 | 10 | 1∶3 | 0.4 | 300 |
Table 2: Ion nitriding process parameters
2.2 Microstructure Observation and Property Testing
The cross – sectional microstructure of the nitrided layer was observed using an intelligent fully automatic Axio Image ZEISS metallurgical microscope. The wear scar morphology characteristics of the samples were observed using a QUATA FEG450 field emission scanning electron microscope. The surface phase composition of the samples was analyzed using a DX – 2700A X – ray diffractometer with a Cu target, a tube voltage of 40 kV, a current of 30 mA, a scanning range of 30° – 80°, and a scanning step of 0.03°. The element distribution in the nitrided layer of the samples was collected using an EPMA – 1600. The surface hardness and cross – sectional hardness of the nitrided samples were tested using an MVC – 1000JMT1 Vickers microhardness tester. The tribological properties of the sample surface were tested using an MS – M9000 multifunctional friction tester. The selected grinding ball was a ϕ5 mm zirconia ceramic ball, and the grinding ball and the substrate were subjected to cyclic reciprocating dry friction. The specific parameters are shown in Table 3.
Temperature (℃) | Time (min) | Frequency (Hz) | Displacement (mm) | Load (N) |
---|---|---|---|---|
10 | 25 | 30 | 2 | 5 |
Table 3: Friction test parameters
The corrosion resistance of the samples was tested using a VersaSTAT4 electrochemical workstation. The corrosion solution was 3.5% NaCl solution, and the reference electrode was a saturated calomel electrode. The ambient temperature was 25 °C, and the effective area of the sample was 1 cm², and the other surfaces were sealed with silicone resin.
3. Experimental Results and Analysis
3.1 Nitrided Layer Microstructure and Element Distribution
Figure 1 shows the cross – sectional metallographic photos of Ni15Cu6Cr2 austenitic gray cast iron after ion nitriding at 380 °C and 540 °C for 10 hours. It can be seen that the nitrided layer of austenitic gray cast iron after ion nitriding mainly consists of a bright white compound layer and a diffusion layer. However, due to the similar microstructure of the diffusion layer and the matrix, it is impossible to distinguish them only from the microstructure. After etching with 4% nitric acid alcohol, it can be seen that there are bright white chromium – rich carbide hard phases with high hardness embedded in the matrix microstructure of austenitic gray cast iron. The area near the flake graphite is severely corroded, indicating that the presence of graphite will affect the corrosion process of austenitic gray cast iron. During the nitriding process, a large number of active atoms generated by gas sputtering react with the Fe atoms on the surface of the cast iron to form nitride FeₓN (x = 1, 2, 3, 4). The increase in nitriding temperature increases the sputtering amount on the surface of the cast iron and the diffusion rate of nitrogen. Nitrogen atoms diffuse along the grains, grain boundaries, and graphite boundaries to form a diffusion layer. As shown in Figure 1(a), after nitriding at 380 °C, the surface compound layer is relatively thin, only about 2 μm, and the distribution is uneven, and no compound layer is formed in some areas. After nitriding at 540 °C, as shown in Figure 1(b), the thickness of the compound layer of the sample is significantly increased, and the thickness of the compound layer is about 10 μm at this time. A layer of black substance can also be observed below the compound layer, which may be a small amount of CrN precipitation. It can also be seen from Figure 1 that due to the cleavage effect of flake graphite, the compound layer will be interrupted at the graphite, and the compound layer near the flake graphite will also be significantly thickened. Compared with other materials and processes, the diffusion blocking caused by flake graphite is a key factor affecting the nitriding reaction. During the nitriding process, flake graphite acts as a diffusion barrier and only allows diffusion to the positions above them. Therefore, the diffusion of nitrogen atoms will take the voids between the flake graphite and the matrix as a shortcut, promoting the formation of a bright white layer on both sides of the near – surface graphite.
From the surface scanning image in Figure 2, it can be seen that the nitrogen concentration gradually decreases along the depth direction of the cross – section. Nitrogen atoms diffuse into the matrix by pushing the carbon atoms in the matrix to the outer surface, enriching the carbon atoms on the outer surface. Therefore, the high nitrogen content in the carbon – depleted region can be explained by the pushing effect of nitrogen. In addition to the aggregation of nitrogen elements only in the nitrided layer region, it can also be observed from Figure 2 that the Cr element is highly enriched in the bright white carbide hard phase. The Ni element is evenly distributed without clustering or enrichment. By comparing the nitrogen and carbon element line scanning graphs of the two temperature nitriding treatments, it can be seen that the thickness of the nitrided layer of the 380 °C nitriding sample is about 15 μm, and the thickness of the nitrided layer of the 540 °C nitriding sample is about 45 μm. The carbon element on the outer surface of the 380 °C nitriding treatment sample is less enriched, mainly because the nitriding temperature is low. According to the Arrhenius formula (K = K₀ exp(-Q/RT)), the higher the temperature, the greater the atomic activity and the diffusion coefficient. Therefore, the nitrogen concentration distribution depth of the 540 °C nitriding sample is large, and the carbon element enriched on the outer surface is also more.
3.2 Nitrided Layer Phase Structure
The XRD patterns of the Ni15Cu6Cr2 austenitic gray cast iron matrix and different temperature ion nitriding samples are shown in Figure 3. The nitrided layer of austenitic gray cast iron is composed of ε phase and γ’ phase. Although the nitriding samples all have diffraction peaks of ε phase and γ’ phase, compared with the 380 °C nitriding sample, the 540 °C nitriding sample can also observe the γ – Fe matrix phase, indicating that the compound layer of the 540 °C nitriding sample is more uniform than that of the 380 °C nitriding sample. At the same time, the increase in temperature makes the diffraction peak of the (111) crystal plane of the γ’ phase stronger, which may be related to the preferential orientation growth of the γ’ phase on the crystal plane. It can also be seen from Figure 3 that the increase in temperature leads to a decrease in the diffraction peak intensity of the ε phase (111) crystal plane. Therefore, it can be inferred that within a certain temperature range, the increase in nitriding temperature promotes the diffusion of nitrogen atoms into the matrix, resulting in the transformation of the ε phase on the surface into the γ’ phase due to the lack of nitrogen atoms.
3.3 Nitrided Layer Hardness
The surface hardness and cross – sectional hardness of the austenitic gray cast iron matrix and different temperature ion nitriding samples are shown in Figure 4. As shown in Figure 4(a), ion nitriding treatment can effectively improve the surface hardness of the material, mainly due to the formation of a nitride layer (composed of a compound layer and a diffusion layer) on the surface. The surface hardness of Ni15Cu6Cr2 austenitic gray cast iron is about 200 HV0.05, the surface hardness of the 380 °C nitriding sample is about 330 HV0.05, and the surface hardness of the 540 °C nitriding sample is about 900 HV0.05, which is about 4.5 times that of the untreated sample. The hardness of the nitrided layer is mainly related to the phase composition and thickness of the nitrided layer. Since the compound layer formed after nitriding at 380 °C is very thin and the thickness is uneven, when measuring the hardness, the matrix also needs to absorb part of the deformation energy generated when the indenter is pressed into the surface, resulting in a relatively low surface hardness. Combined with the microstructure and EPMA analysis, it can be seen that after ion nitriding at 540 °C, a certain thickness of compound layer and diffusion layer are formed. Since the amount of N atoms penetrating decreases stepwise from the surface to the inside, the cross – sectional hardness of the diffusion layer gradually decreases along the depth direction of the nitrided layer.
3.4 Nitrided Layer Tribological Properties
For the wear resistance of Ni15Cu6Cr2 austenitic gray cast iron, the wear scar width and friction coefficient are comprehensively evaluated. Figure 5 shows the change curve of the friction coefficient of the Ni15Cu6Cr2 austenitic gray cast iron matrix and different temperature ion nitriding samples under a 10 N load with time. It can be seen that at the beginning of the friction, the friction coefficient of the matrix and different temperature nitriding samples all shows a downward trend. This may be because the graphite 夹杂 in the material is relatively soft, and when the sample rubs against the grinding ball, the graphite exposed on the surface of the sample will be quickly worn away. Due to the lubricating effect of graphite, the friction coefficient of the sample decreases. When the friction time is about 2 minutes, the friction coefficient of the 380 °C nitriding sample rises sharply. This may be because the compound layer on the surface of the sample is relatively thin and is worn through at about 2 minutes. The hard fragments of the compound layer are embedded in the matrix, resulting in a sharp rise in the friction coefficient. It rises to 0.185 and then gradually stabilizes, with a large fluctuation range, and the maximum friction coefficient is 0.206. When the friction time reaches about 13 minutes, the friction coefficient of the 540 °C nitriding sample begins to rise slowly. The reason may be that the continuously generated wear debris forms an adhesion on the compound layer under the action of the grinding ball, covering the exposed graphite, which causes the friction coefficient to rise slowly. It stabilizes at about 0.125, and the fluctuation range is small, and the maximum friction coefficient is 0.129. Finally, the average friction coefficient of the 380 °C nitriding sample is 0.173, and the average friction coefficient of the 540 °C nitriding sample is 0.088.
shows the wear scar morphology of the Ni15Cu6Cr2 austenitic gray cast iron matrix and different temperature ion nitriding samples under a 10 N load. Combined with the previous microstructure and hardness analysis, it can be known that different temperature nitriding treatments will have a certain impact on the microstructure and hardness of the samples, and these impacts will cause differences in the wear resistance of different temperature nitriding samples. As shown in Figure 6(a), the wear scar of the austenitic gray cast iron matrix is relatively wide and the scratch is relatively severe, and the wear scar width is about 345 μm. As shown in Figure 6(b), there are a large number of plow grooves in the wear scar on the matrix surface, and there is also a large amount of metal peeling accompanied by the graphite on the surface. This is because when the sample rubs against the grinding ball, the graphite with a relatively soft texture on the surface will be worn away first, and the hardness of the matrix tissue around the graphite is much greater than that of the graphite. Therefore, after the graphite is worn away, a pit is formed, and the matrix tissue around it is equivalent to forming a sharp corner, which is easy to peel off during the friction process. The wear form is mainly abrasive wear. As shown in Figure 6(c), the wear scar width of the 380 °C nitriding sample is about 316 μm, which is slightly narrower than that of the matrix. As shown…
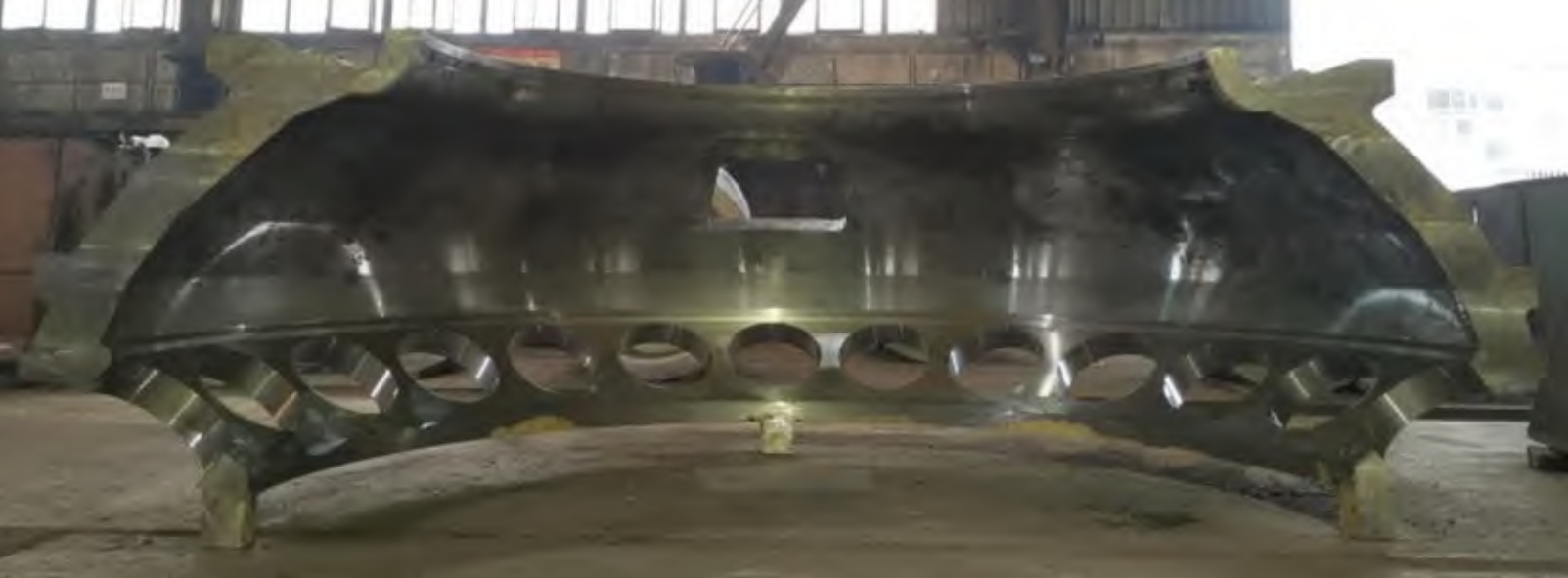