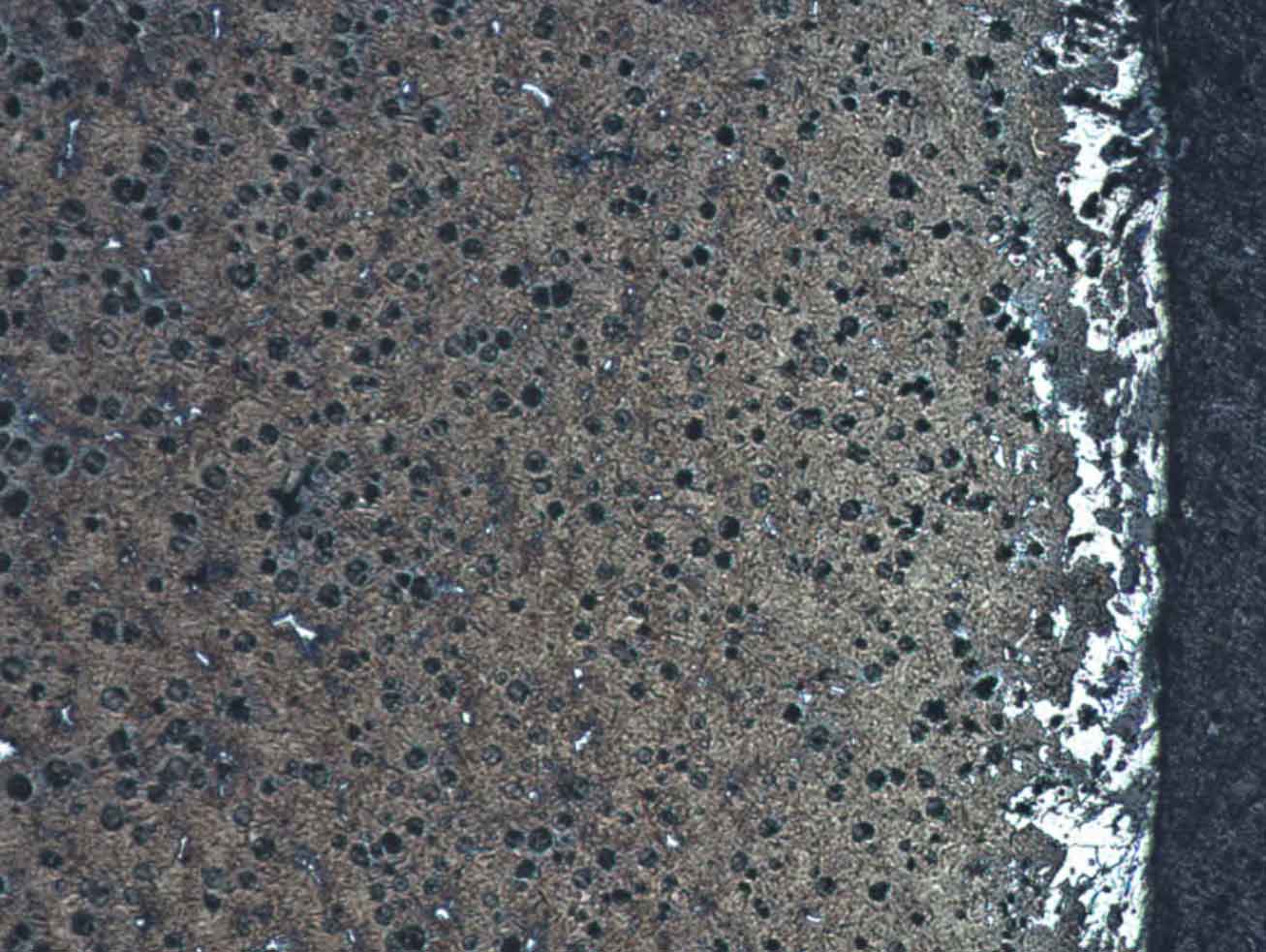
To do a good job of Si-Mn alloyed nodular cast iron grinding ball, first of all, spheroidize the nodular cast iron grinding ball well. The size and quantity of graphite balls are uniform. The spheroidization grade should be I-II, as shown in Figure 1 and Figure 2. The whole heat treatment process is combined with the chemical composition of the grinding ball to formulate a scientific heat treatment process and reasonably control the quantity, morphology and distribution of matrix martensite, bainite, carbide and residual austenite.
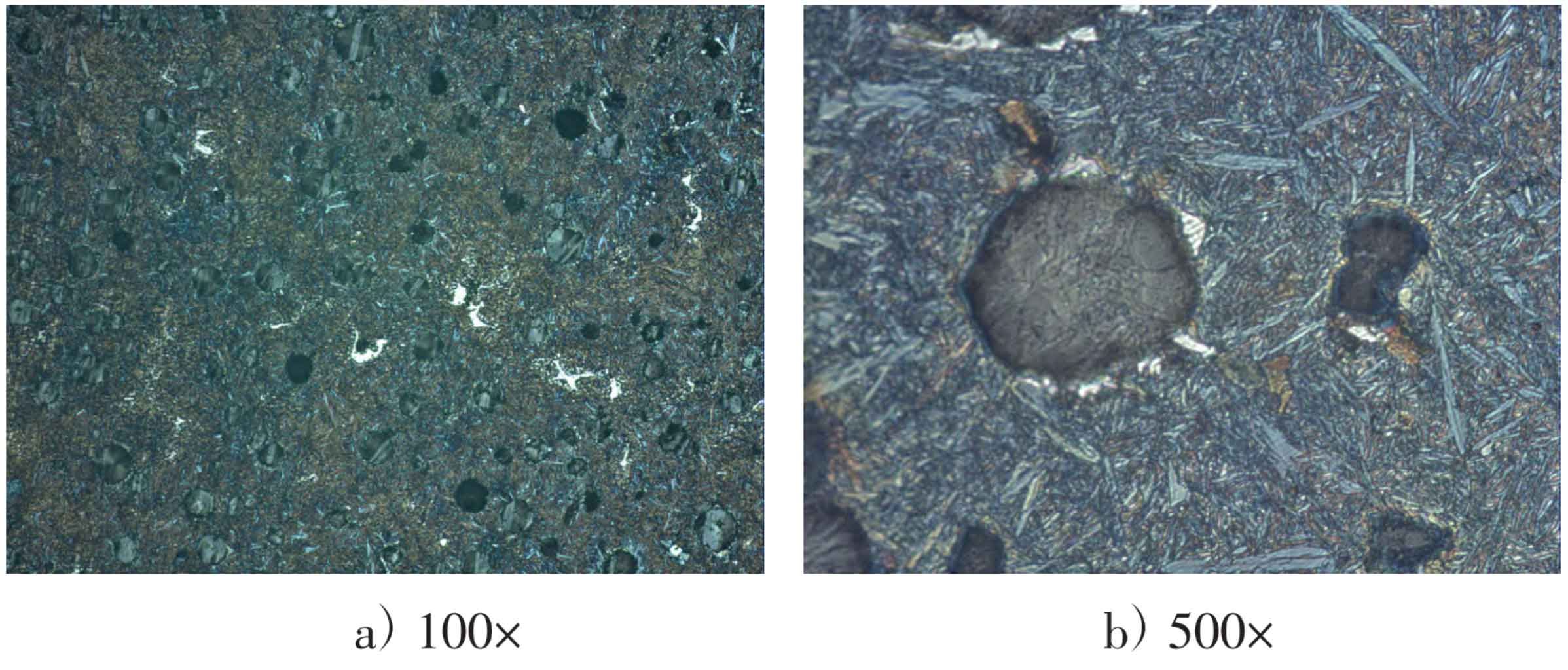
The appropriate metallographic structure can achieve the appropriate grinding ball performance. The ideal metallographic structure of Si Mn alloyed ductile iron grinding ball is martensite and a small amount of bainite as the matrix+an appropriate amount of retained austenite and carbide+graphite ball. The specific metallographic structure is shown in Fig. 3 and Fig. 4.
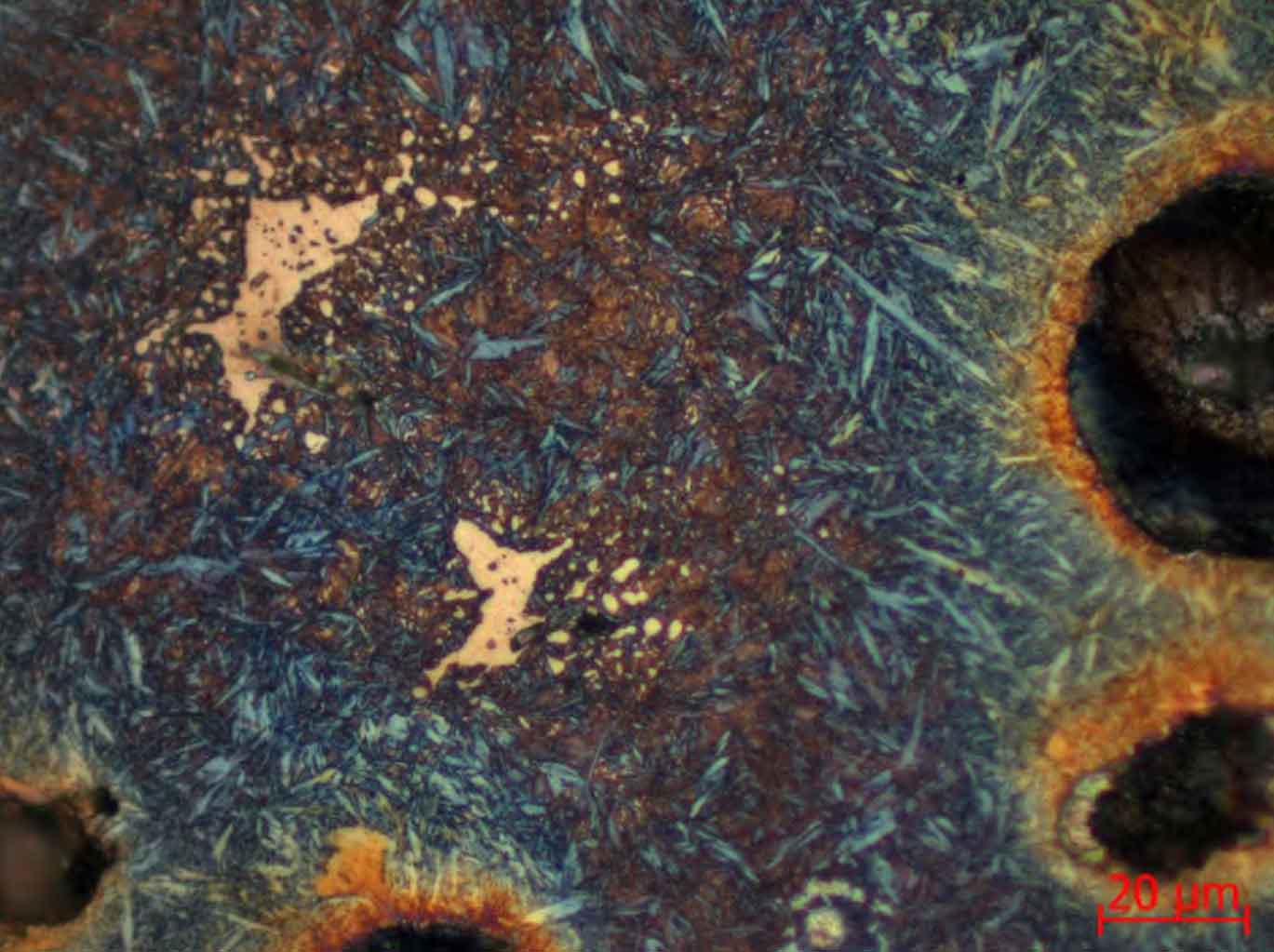
It can be seen from the metallographic analysis that the microstructure from the surface to the interior is composed of graphite ball (with good spheroidizing effect), martensite, austenite and some carbides, with good homogeneity of the structure, which can make the mechanical properties of each part of the cast ball more uniform (such as hardness). Quenched and tempered with water-based quenching medium φ 100 mm ductile iron grinding ball properties. Figure 5 shows the hardness testing position of the grinding ball.
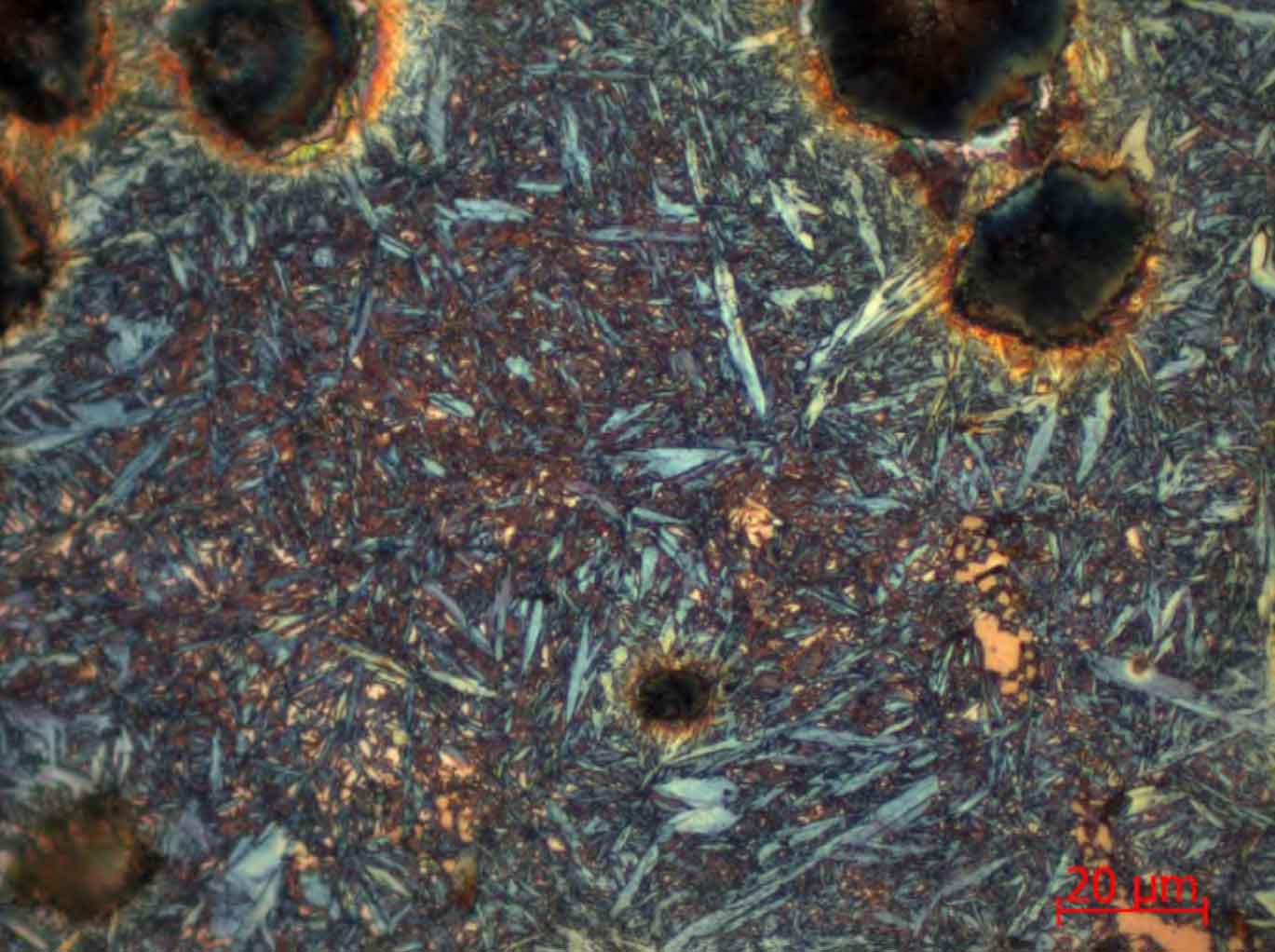
Si-Mn alloyed ductile iron has good hardenability. It can be found that the hardness of the grinding ball center reaches about HRC51, indicating that the center has been hardened. The hardness difference between the ball center and the ball surface is only about 2HRC, indicating that the hardness distribution is relatively uniform. The grinding ball has the function of work hardening. After the grinding ball runs for a period of time, the residual austenite structure on the surface is transformed into martensite structure under the action of external force, and the surface hardness is improved, and the hardness can reach HRC58. Good impact toughness can make the number of ball drops reach 20000 times, which is resistant to breakage.
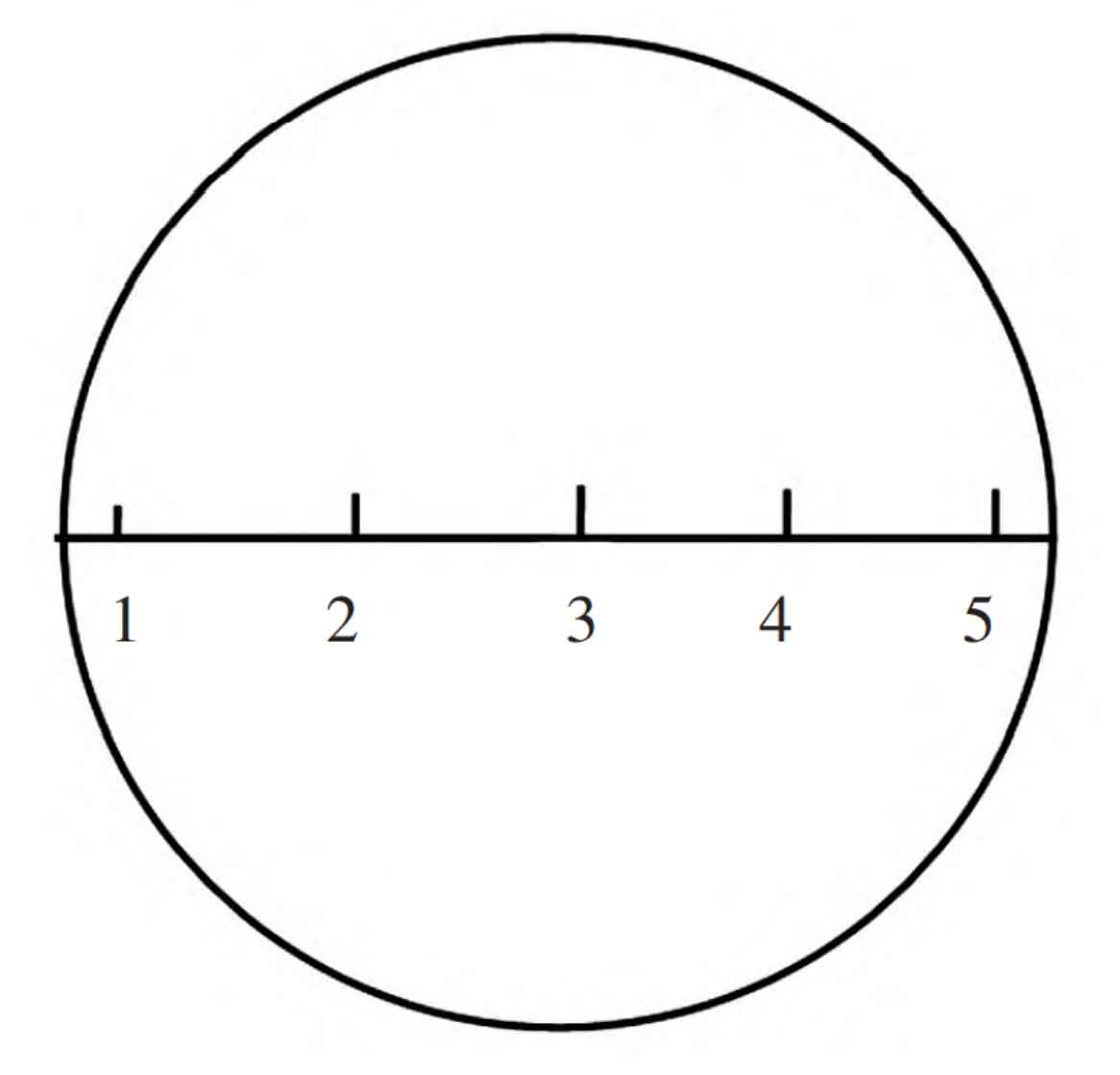
Si-Mn alloyed ductile iron grinding ball has the characteristics of high hardness and high toughness. This kind of grinding ball has been successfully applied to the 8.8M diameter mill in the subordinate mines of China Gold, creating a precedent for the application of casting grinding balls in large SAG mills. This kind of grinding ball is used in the φ 10.37 m × The 5.49m SAG mill has been applied adaptively. According to the report issued by the Mineral Processing Department of Yuanjiacun Mine, the test results meet the expected requirements. The average hardness of the grinding ball is HRC51.3, and the ball crushing rate of 1% is similar to the original grinding ball. During the adaptive application of casting ball, the processing capacity of a series of semi autogenous grinding in Yuanjiacun Mine is stable at 950 t/h, the operating power is between 6065 kW~7985 kW, the stability rate of overflow particle size of primary cyclone is 96.04%, and the production process indicators are normal.