Fig. 1 shows the microstructure of high silicon molybdenum ductile iron after different thermal cycles at the upper temperature of 850 C.It can be seen from the diagram that the degree of oxidation of the sample surface increases with the number of thermal cycles under this high temperature environment.Compared with the as-cast structure in Figure 1a, Figures 1b, 1c and 5.1dA large area of grey material appears in the ferrite matrix, precipitates at the grain boundaries of the ferrite, and the more cracks there are at the aggregation of the material; and there are some bright particles on the oxidation surface, most of which occur at the disappearance of graphite; furthermore, the deformation of cracks at the carbide is significantly larger than that near the graphite.
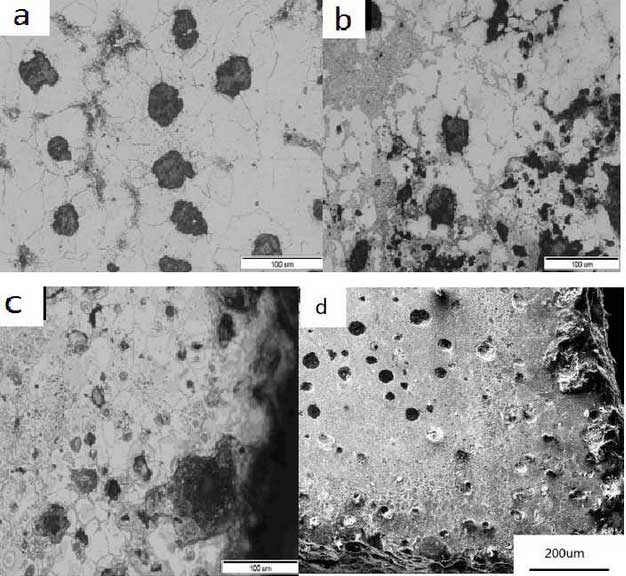
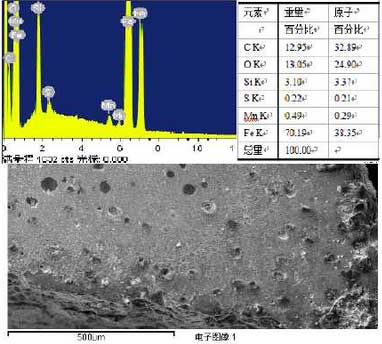
According to the XRD analysis results of ZHY Casting Senior Engineer, it is shown that there are large amounts of iron oxides on the surface of high silicon molybdenum ductile iron samples and high nickel ductile iron samples after several thermal cycles.In order to understand the structure changes after oxidation of the sample surface, the surface of the sample is analyzed by surface scanning electron microscopy and energy spectrum, the results are shown in Fig. 2 and Fig. 3.Figure 2 shows the results of scanning analysis on the surface around the crack. From Figure 2, it can be seen that the surface composition of the sample is mainly composed of C, O, Si, S, Mn, Fe, etc. The content of C, Fe, O and Si is high, and the atomic percentage of oxygen is about 25%.
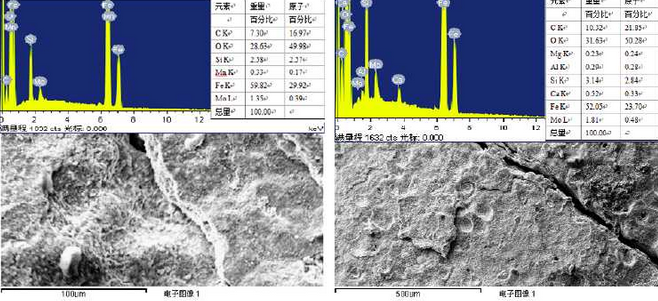
Figure 3 shows the results of surface scanning analysis at the crack fracture. It can be seen from the diagram that the sample composition at the crack fracture is mainly composed of C, O, Si, Mn, Fe, Mo and mg, in which the atomic percentage of oxygen is about 50%.The large-scale oxygen content indicates that both the surface and the fracture of the sample have been strongly oxidized and the main components are basically various oxides.It is found by comparison that the oxidation degree of the sample at the fracture is more intense than that of the undamaged surface of the sample.It also shows that the elements that make up the high silicon-molybdenum ductile iron can improve the oxidation resistance of the material to a certain extent.
In order to understand the distribution of each component element during the oxidation process, the observation area is selected around the cross-crack on the sample by means of element analysis. The specific area is shown in Figure 4a. The scanning results of each element are shown in Figure 4b-4f. The carbon element is mainly concentrated in the graphite embedded in the matrix, while the distribution at the crack is very small, as shown in Figure 4b; from Figure 4CIt is observed that the distribution area of iron element is relatively large and relatively uniform, while the distribution amount at crack is relatively small; according to Fig. 4d, molybdenum metal element mainly deposits at ferrite grain boundary and distributes relatively uniformly; from Fig. 4e, it can be observed that oxygen distributes extensively on the surface of sample, and the proportion of oxygen exists at crack is more than that in other areas and is almost invasive.80% or so; however, the distribution of silicon is relatively dispersed and uniform, as shown in Fig. 4f.
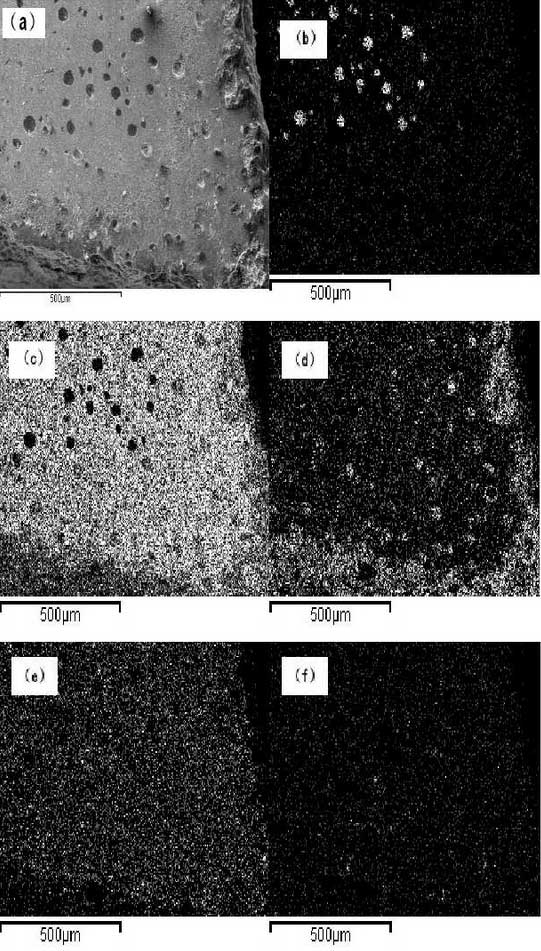
In order to further understand the composition of oxides in the undamaged area, the undamaged area is tested by point sweep method. As shown in Fig. 5, the Si- and Fe-rich oxides are evenly distributed on the surface of the sample, considering that the atomic ratio of iron, silicon and oxygen is close to 41:5:33.It is composed of Fe-Si oxide, SiO 2, Fe-Si oxide, SiO 2, etc., but the distribution of each phase is not continuous; at the same time, there are a few molybdenum oxides and molybdenum silicides on the surface.According to the research of Wang Xuecheng, the following reaction takes place on the surface of high silicon-molybdenum ductile iron.
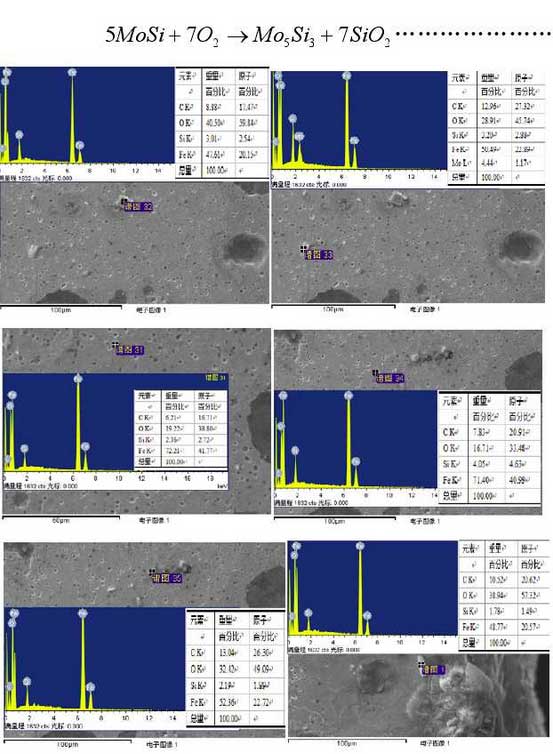
However, no oxides of metallic manganese were found in the test.The dense SiO2 Oxygen 2 oxide film prevents the intrusion of oxygen to some extent, as element analysis shows that the oxygen content in the undamaged area is less than that at the crack.