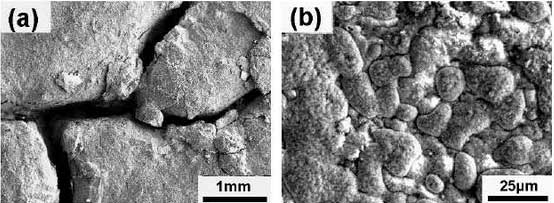
The red oxide layer of high nickel ductile iron covers the surface of the sample while holding for 80 hours at 900 C, but its deformation and oxide layer thickness are significantly smaller than that of high silicon molybdenum ductile iron.Fig. 1 shows the microstructures of 200 thermal cycling samples at 900 C. It can be seen from the diagram that oxidation occurs on the surface of the samples and is more severe at the carbide than at the austenitic matrix. At the same time, the number of graphite decreases considerably.At high temperature, the oxide layer undergoes different thermal deformation due to the difference of expansion coefficient between the oxide layer and the matrix, resulting in separation from the matrix, or even partial shedding, and re-oxidation at the shedding place, resulting in the uneven oxidation surface shown in Fig. 1.Oxygen in air acts together with oxidative corrosion and thermal stress produced by cold and hot cycles, resulting in cracks during thermal fatigue.
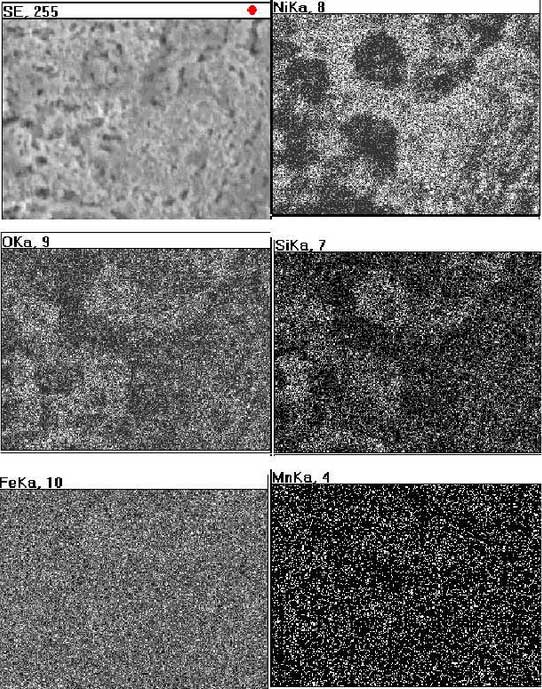
In order to understand the oxidation behavior of high nickel ductile iron, a surface scan analysis near the crack in the sample was selected, the results are shown in Figure 2.It can be seen from the diagrams that the distribution of Fe and Mn is uniform, the distribution of Si and Ni is slightly aggregated, and in most cases oxygen is accompanied by the distribution of silicon, indicating that iron and silicon elements are oxidized on this surface, while intermetallic compound FeN I3 in tissues has the possibility of intermetallic compound FeN I3 without oxidation.
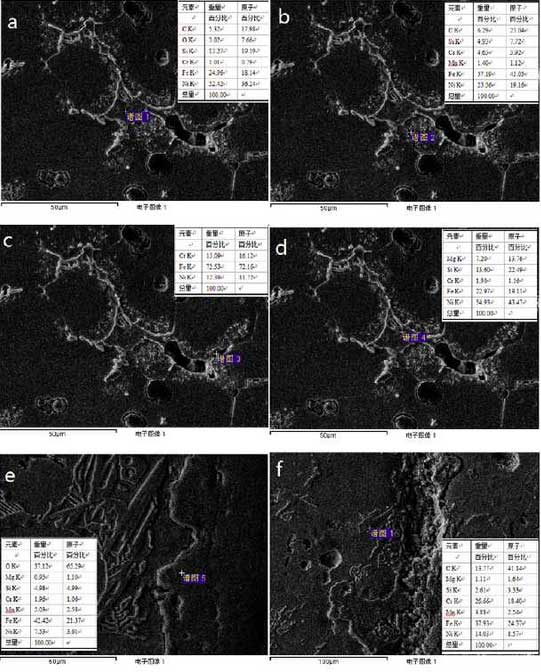
The oxidation of high nickel ductile iron is investigated by point scan analysis of the material around the crack. The test results are shown in Figure 3.According to Figure 3a and Figure 3b, it can be judged that Si and Cr are enriched in the oxide layer. According to literature, silicon is Fe2S, silicon is Fe2S, silicon is Fe2SiO4, chromium is Fe2C, chromium is Fe2CrO4, chromium is Fe2CrO4. With the increase of oxidation degree, Fe2S exists, Fe2S exists, Fe2SiO4 and Fe2C and F exist. With the increase of oxidation degree, Fe2S exists.Increasing e2CrO4 content increases the tightness and protection of the oxide layer
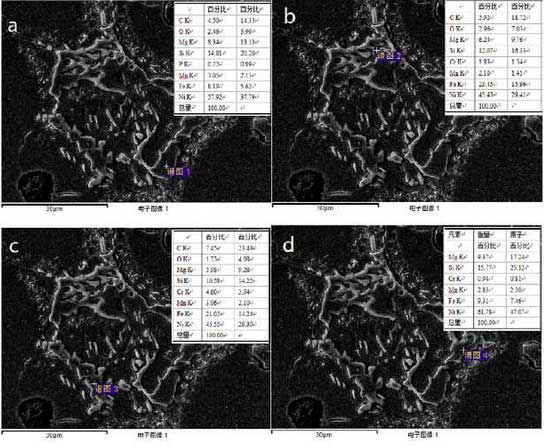
As shown in Fig. 3C, intermetallic compound FeN I3 does not oxidize during high temperature operation; magnesium metal is introduced during the spheroidizing process of casting, and its oxidized MgO particles are dispersed in the carbides of graphite or manganese, and remain there when graphite oxidation disappears.
Compounds of other shapes also exist in high nickel ductile iron and are analyzed by point scanning. The test results are shown in Fig. 4.Manganese-rich oxides are present here, which are often reported as granular but are non-protective oxides.
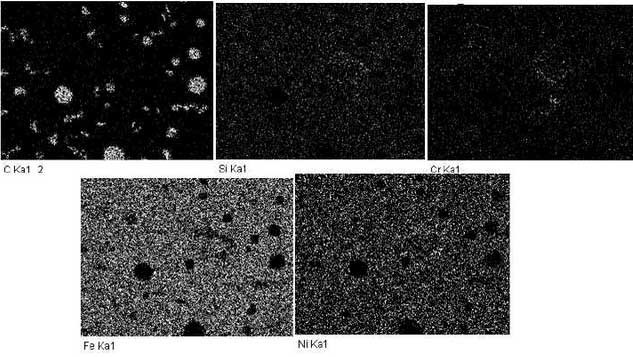
In addition to the unoxidized intermetallic compound FeN i3, there is also a small amount of nickel oxide in the substance according to the measured proportion.Oxygen mainly enters through oxidation reaction with iron, silicon, chromium and other elements. Oxygen accelerates the oxidation process due to thermal fatigue and promotes crack formation at the same time, but no nitrogen element has been found. The discussion about precipitation of nitride proposed by F. Tholence to promote oxidation cannot be reflected in this study.
In order to understand the surface changes of the sample at the initial stage of oxidation, the surface of the sample is selected for surface scanning analysis and the results are shown in Fig. 5.At the beginning of oxidation, the size of graphite decreases and carbides are often formed with the precipitated metals around it; silicon is uniformly distributed, chromium still exists at austenitic grain boundaries in the form of carbides, iron and nickel exist together, and oxygen intrusion is very small, which can hardly be observed. This also indicates that high nickel ductile iron is better than high silicon molybdenum ductile iron in oxidation resistance.During the oxidation process, the formation of each product is determined by its thermodynamic relationship, which is shown in Fig. 6 according to literature.
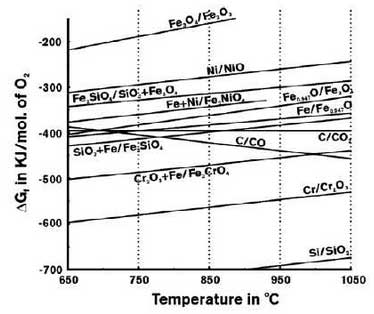
The more negative the value, the greater the tendency to oxidize. As Si, Cr, Fe and other elements are easier to form oxides, and the content of the material is larger, while nickel is less prone to oxidize, the oxidation resistance of high nickel ductile iron is better than that of high silicon molybdenum ductile iron, and a large amount of intermetallic compound FeN i3 still exists in high nickel ductile iron after several thermal cycles.