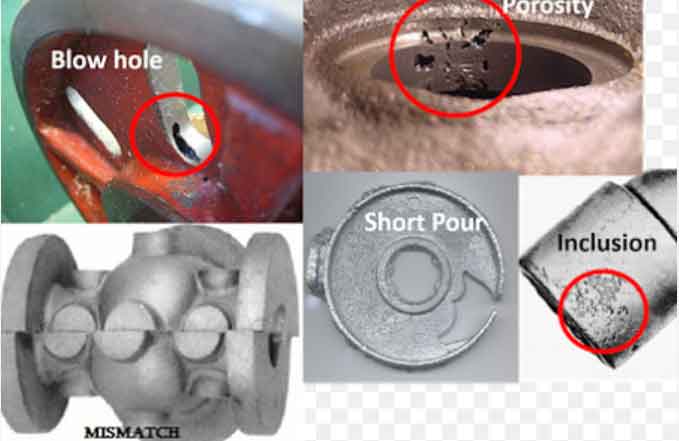
Process optimization plays a crucial role in minimizing casting defects and ensuring high-quality metal castings. By considering various factors from the design stage to the production phase, manufacturers can optimize the casting process and reduce the occurrence of defects. This article explores the key steps involved in process optimization to minimize casting defects and improve overall casting quality.
1.Design Optimization:
a) Design for Manufacturability:
Optimize the casting design to facilitate proper mold filling, solidification, and cooling. Consider factors such as part geometry, wall thickness, fillets, and draft angles to prevent defects like misruns, shrinkage, or porosity.
b) Simulation and Analysis:
Utilize computer-aided design (CAD) and casting simulation software to analyze and optimize the casting process virtually. This helps identify potential defects, optimize gating systems, predict solidification patterns, and improve casting quality before production.
2.Material Selection and Control:
a) Material Compatibility:
Select materials that are suitable for the casting process and exhibit desirable properties. Consider factors such as fluidity, shrinkage characteristics, and thermal conductivity to minimize defects.
b) Material Testing and Verification:
Conduct material testing to ensure the quality and consistency of the selected alloys. Perform chemical analysis, mechanical testing, and microstructural analysis to verify material properties and identify any potential issues that may lead to defects.
3.Process Parameter Optimization:
a) Pouring Temperature and Rate:
Optimize pouring parameters to ensure proper metal flow and filling. Control the pouring temperature and rate to prevent defects such as misruns, cold shuts, or inadequate filling.
b) Cooling and Solidification Control:
Implement controlled cooling techniques to achieve uniform solidification, prevent shrinkage defects, and minimize residual stresses. Consider the use of chills, risers, or cooling channels to optimize solidification patterns.
c) Gating System Design:
Design an efficient gating system that promotes smooth metal flow, minimizes turbulence, and allows for proper mold filling. Optimize gate sizes, shapes, and locations to prevent defects like porosity or incomplete filling.
4.Quality Control and Monitoring:
a) Process Monitoring:
Implement real-time process monitoring techniques to track critical parameters such as temperature, pressure, and cooling rates. This allows for immediate detection of deviations and prompt corrective actions to minimize defects.
b) Inspection and Testing:
Perform thorough inspection and testing at different stages of the casting process. Utilize visual inspection, non-destructive testing (NDT), and dimensional measurements to identify defects, ensure dimensional accuracy, and verify casting quality.
5.Continuous Improvement:
a) Data Analysis and Feedback:
Analyze historical data, defect records, and process parameters to identify trends and patterns. Utilize this information to make data-driven decisions, identify areas for improvement, and implement corrective actions.
b) Collaboration and Knowledge Sharing:
Foster collaboration between design, production, and quality teams to share knowledge, experiences, and best practices. Encourage feedback and communication to facilitate continuous improvement throughout the casting process.
Minimizing casting defects through process optimization requires a holistic approach from design to production. By optimizing the casting design, selecting appropriate materials, controlling process parameters, implementing robust quality control measures, and fostering continuous improvement, manufacturers can significantly reduce casting defects and improve overall casting quality.