Quality assurance plays a vital role in ensuring the production of high-quality castings. Casting defects can negatively impact the performance and reliability of metal components. Implementing effective quality assurance measures is crucial for mitigating and minimizing casting defects. This article focuses on the importance of quality assurance in casting and presents strategies for mitigating and minimizing casting defects.
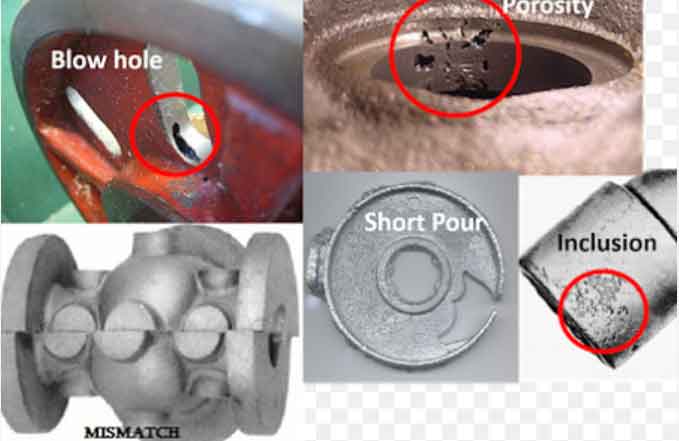
- Robust Process Controls:
- Implement comprehensive process controls to monitor and regulate key parameters such as pouring temperature, pouring rate, mold temperature, and solidification time.
- Utilize advanced process monitoring technologies to detect abnormalities and deviations in real-time, enabling prompt corrective actions.
- Conduct regular process audits and inspections to identify potential issues and ensure adherence to defined procedures.
- Material Selection and Testing:
- Thoroughly evaluate and select suitable casting materials based on the component’s requirements, considering factors such as mechanical properties, fluidity, and shrinkage characteristics.
- Conduct rigorous material testing, including chemical analysis, mechanical testing, and microstructural examination, to verify material quality and consistency.
- Establish a reliable supplier qualification process to ensure a consistent supply of high-quality raw materials.
- Robust Mold Design and Preparation:
- Employ experienced mold designers to optimize gating and riser systems, ensuring proper filling and minimizing turbulence.
- Utilize advanced mold simulation software to analyze and optimize mold design, identify potential defects, and optimize gating and feeding systems.
- Implement effective mold preparation techniques, such as proper mold coating, to enhance mold surface quality and reduce defects.
- Process Optimization and Control:
- Continuously analyze and optimize process parameters to achieve optimal casting conditions.
- Implement appropriate feeding and riser systems to ensure adequate material supply and minimize shrinkage defects.
- Utilize advanced solidification modeling and simulation tools to predict and prevent potential defects caused by solidification issues.
- Inspection and Non-Destructive Testing:
- Conduct thorough inspections of castings using visual inspection, dimensional measurement, and non-destructive testing techniques such as X-ray, ultrasonic, or magnetic particle inspection.
- Establish stringent acceptance criteria and quality standards for casting inspections.
- Implement regular quality checks at various stages of the casting process to detect and address defects early on.
- Continuous Improvement and Training:
- Foster a culture of continuous improvement by encouraging feedback, learning from past defects, and implementing corrective actions.
- Provide regular training and skill development programs for foundry personnel to enhance their knowledge of casting processes, defect recognition, and quality control techniques.
- Implement effective communication channels between design engineers, foundry personnel, and quality assurance teams to facilitate collaboration and address potential issues proactively.
Quality assurance is essential for mitigating and minimizing casting defects in the production of high-quality castings. By implementing robust process controls, conducting thorough material selection and testing, optimizing mold design and preparation, and utilizing inspection and non-destructive testing techniques, manufacturers can enhance quality and reduce defects. Continuous improvement efforts, along with training and collaboration, further contribute to the success of quality assurance in casting. By prioritizing quality at every stage of the casting process, manufacturers can achieve defect-free castings and meet the highest standards of performance and reliability.