The research object is an A356 aluminum alloy wheel hub of a domestic passenger car brand, with a wheel hub model size of 19 × 8J PCD -5 × 112, its appearance is shown in Figure 1. As a key component, the wheel hub determines the reliability of the car during driving, therefore there are high requirements for the casting quality of this component.
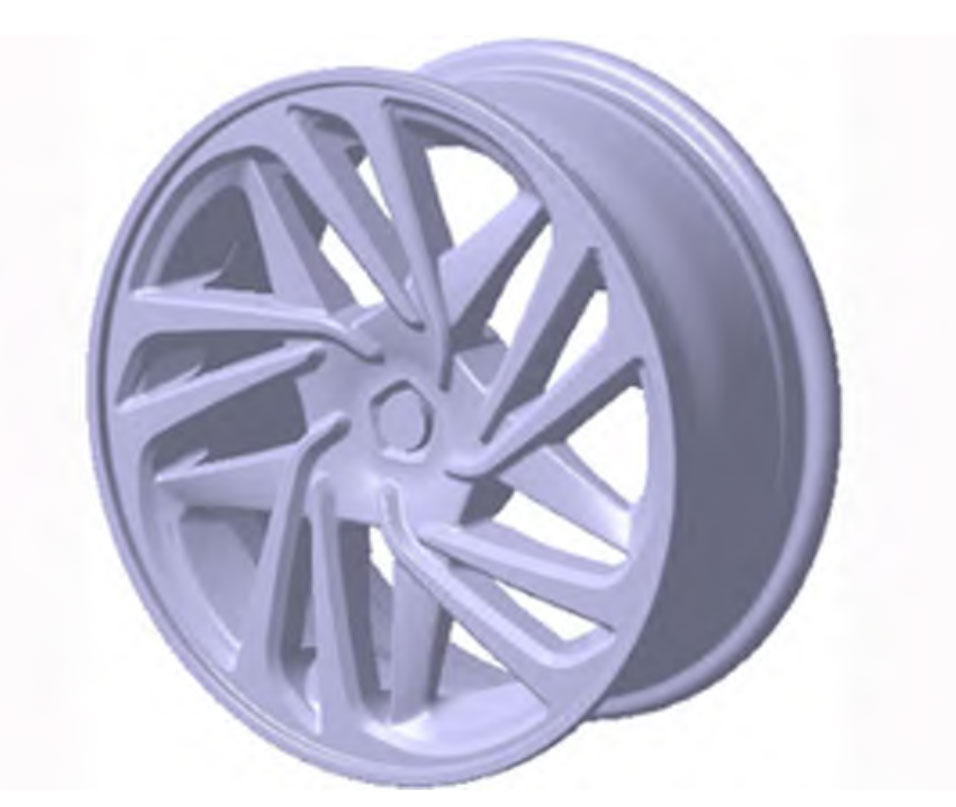
According to the trial production data of the manufacturer, this type of wheel hub is prone to defects at the junction of the spoke and rim, as well as at the end of the rim.
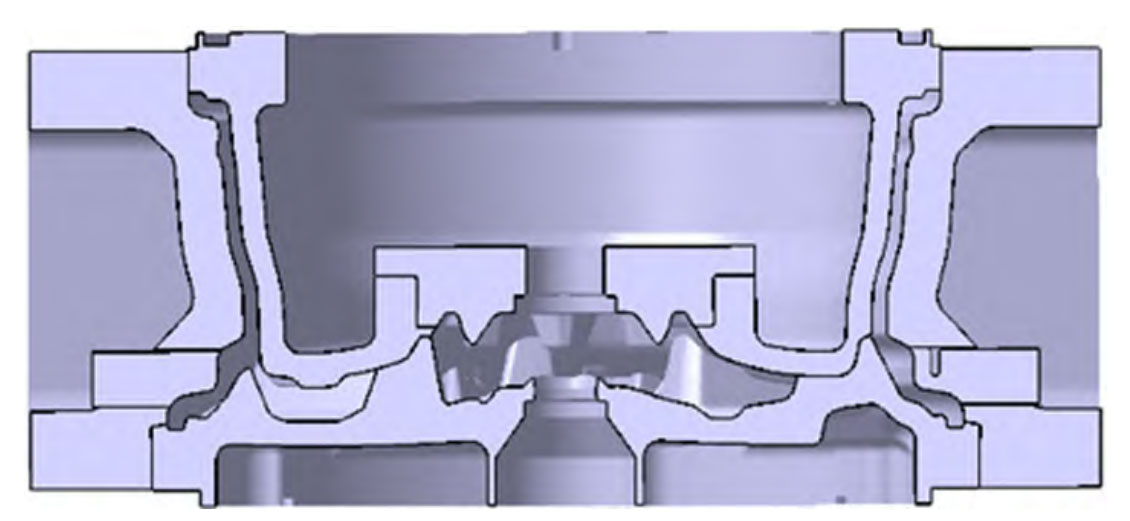
Through the analysis of the mold in Figure 2, it can be seen that the cross-sectional area of the wheel rim between the upper mold and the side mold, as well as the spoke between the upper mold and the lower mold, is relatively small. Early solidification in this area can cause poor shrinkage. Therefore, it is necessary to adjust and optimize the process parameters to improve the quality and yield of the wheel hub.