Introduce the model into ProCast software and divide it into grid. After dividing the grid, check the quality of the grid. If poor quality of the grid occurs or the grid crosses, repair and divide the volume grid first, so as to ensure the quality of the grid dividing.The grid dividing diagram is shown in the figure.
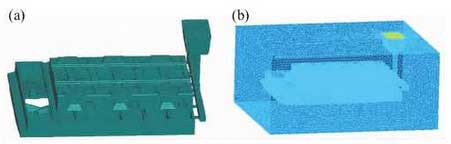
The main parameters during pouring are as follows: setting pouring temperature T=1380 C; initial temperature T sand 1380 C; initial temperature T sand mold=30 C; pouring metal Fe-GG-25 (HT250); sand mold material is resin sand; heat exchange coefficient between sand mold and casting is 500W/(heat exchange coefficient between M2 /(heat exchange coefficient between M2 /(500W/(m2 /).
The casting process of the bed was simulated by ProCast software, and the original casting process with air vent and blank holder riser was optimized according to the simulation results. The final casting process can successfully eliminate casting defects.