Large steel castings generally refer to steel castings with a single gross weight of more than 5 t. With China’s vigorous development of power, transportation, petrochemical, basic machinery, national defense and other industries, the demand for large steel castings is increasing. Large steel castings provide blanks for the manufacture of major complete sets of equipment, and also directly provide spare parts for major engineering projects. Therefore, the quality of large steel castings has become a key factor in the reliability of complete sets of equipment, and the manufacturing of large steel castings has also become an important symbol to measure the development level of China’s heavy industry and China’s comprehensive national strength.
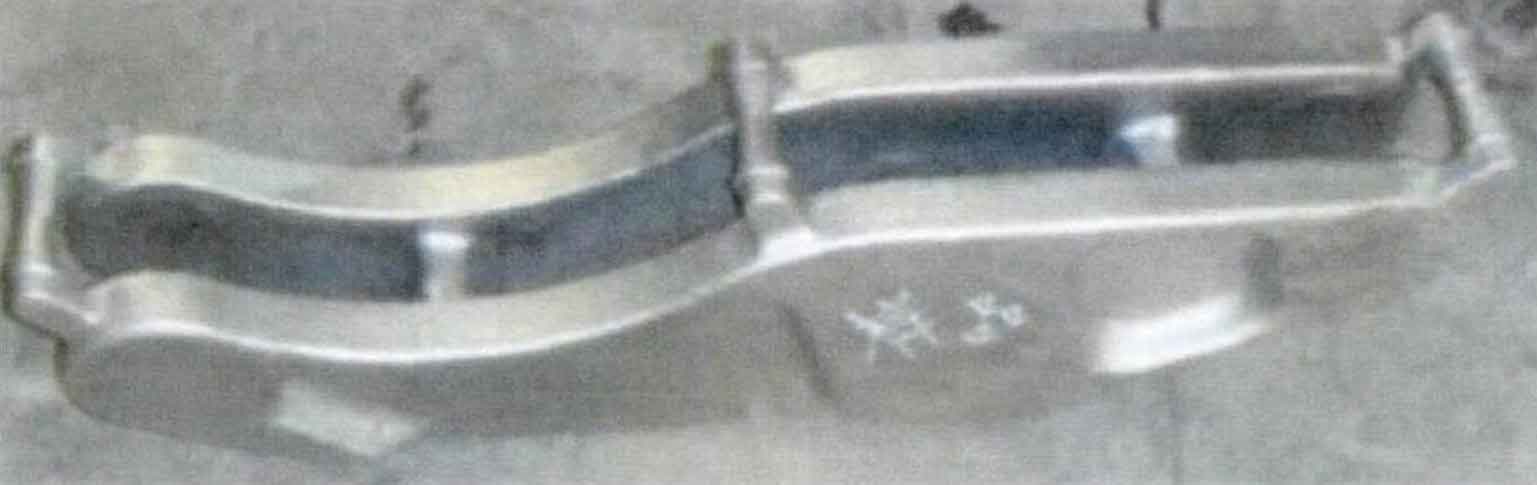
In recent years, Chinese foundry enterprises have continuously increased investment in the construction, expansion or technological transformation of steel casting workshops, and adopted advanced, applicable and reliable new processes and technologies, especially the improvement of large-scale steel casting modeling and core making technology, so as to improve the production level of large-scale high-end steel casting products, so as to meet the growing demand of China’s economic growth for large-scale steel castings.
Molding and core making process play a very important role in casting production. If the process selection is not appropriate, it may have a great impact on the quality, production efficiency and production cost of castings, such as the obvious increase of crack defects of castings, poor collapsibility of old sand, etc. Therefore, choosing the appropriate production process is particularly important for improving the quality of castings, improving production efficiency, reducing production costs and improving labor conditions.
At present, the molding processes available for the production of steel castings, especially large steel castings, mainly include sodium silicate sand process, resin sand process, etc. Sodium silicate sand can be classified into ordinary CO2 hardened sodium silicate sand, organic ester self hardening sodium silicate sand, heating hardened sodium silicate sand, etc. The commonly used resin sand mold can be divided into two categories: furan resin self hardening sand and alkaline phenolic resin self hardening sand.
Furan resin sand, alkaline phenolic resin sand and ester hardened sodium silicate sand processes are used by enterprises in the production field of major steel castings. At present, the furan resin sand process is adopted by China National First Heavy Industry Group Co., Ltd. (which has implemented the four-phase transformation), shared steel casting and Sinovel steel casting, and the furan resin sand process is adopted by China National Second Heavy Industry Group Co., Ltd. (which has implemented the two-phase transformation), Taizhong, Guangzhou Guangzhong Enterprise Group Co., Ltd. (the former Guangzhou heavy machinery factory is referred to as Guangzhong for short) Shanghai Honggang power plant equipment casting and Forging Co., Ltd. (hereinafter referred to as Shanghai Honggang) adopts the alkaline phenolic resin sand process, and Shangzhong and CITIC Heavy Industries adopt the ester hardened sodium silicate sand process; Furan resin sand process is basically used in large steel castings abroad, and all enterprises can successfully produce after using the selected self hardening sand process. Through the above comparison, ester hardened sodium silicate sand, furan resin sand and alkaline phenolic resin sand have their own advantages and disadvantages. When selecting the process plan, we should comprehensively consider the cost (direct and indirect costs), quality and environmental protection factors, and determine it based on the experience of the contract industry.
Through the analysis of the actual application of several manufacturers, it can be seen that the application of resin sand molding technology in the production of large steel castings has become a development trend. However, each company should choose the appropriate production process according to its actual situation and the usage habits of each factory.