There used to be a saying in the machinery manufacturing factory: “The lathe workers are afraid of the car pole, and the sander is afraid of turning the film”. The latter means that the production of thin-walled and large-area steel castings is prone to quality problems.
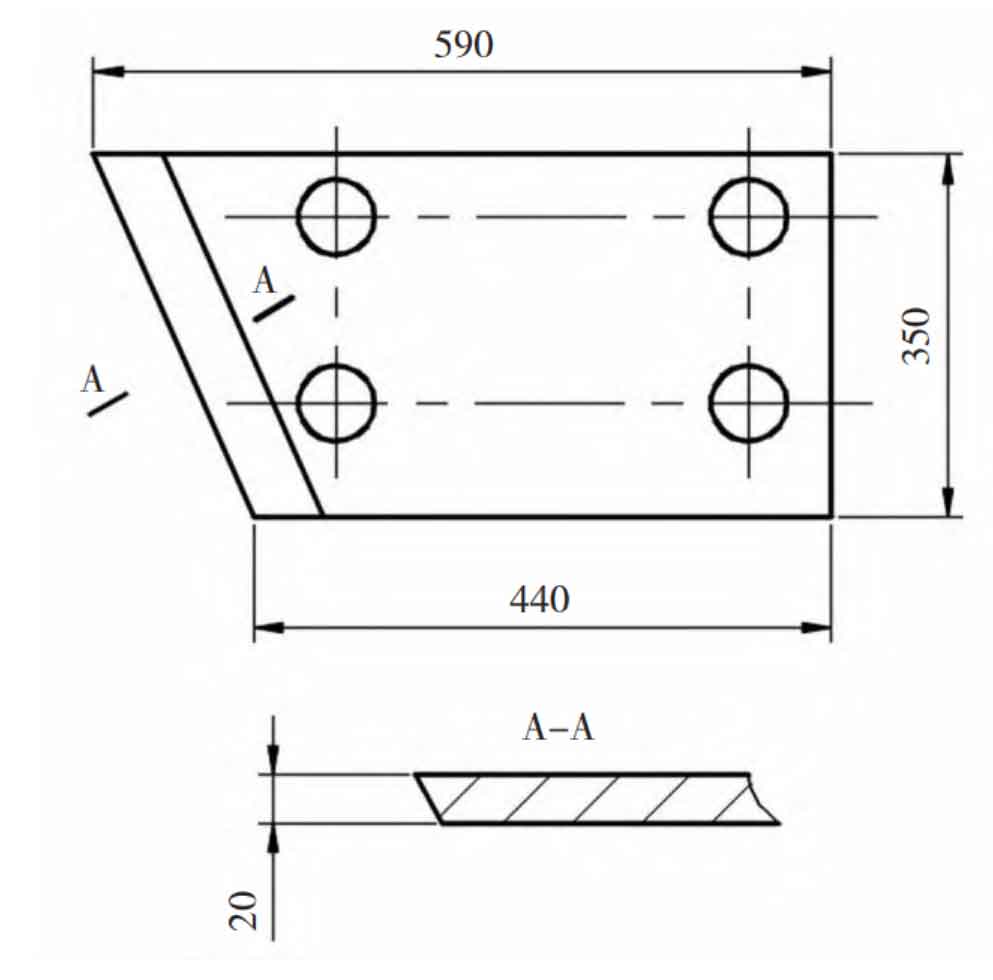
The steel casting of guard plate for mining is made of medium chromium cast steel. During service, the product is required to be resistant to impact wear and high toughness, and cannot be broken during use. The geometric shape of the steel casting is shown in Figure 1, which belongs to the flat type thin-walled structure. During the casting process, cold shut, sand inclusion and other casting defects are easy to occur. According to the structural characteristics of steel castings, the inclined casting molding scheme is adopted to ensure the quality and achieve good results.
The reticulated bottom plate tooling cools the different sides of the steel castings by designing the mold structure to speed up the cooling, reduce the local high hardness or color difference of the steel castings, and thus replace the chill iron chilling. This scheme saves the lower box of the mold, makes the reticulated bottom plate tooling itself replace the lower sand box, reduces the sand-to-iron ratio of the steel castings, and improves the working efficiency. The production verification shows that this method can reduce the casting cost by about 5%.