The main characteristics of the magnetic traces of linear defects detected by MT are mainly linear aggregated magnetic traces with large length width ratio. In ASME standard, the linear defects are defined as the display with the aspect ratio greater than 3. The defect indication position of the intake cylinder line is mainly concentrated on the back of the air inlet side, which belongs to the upper surface of the pouring position, and also belongs to the position with the longest baking time of high-temperature molten iron during the pouring process. According to theoretical analysis, the position is easy to form inclusions and slag inclusion defects, and the defects are evenly distributed in different severity on the whole surface, and the size of defects is irregular.
After cleaning the magnetic mark on the position with linear indication, the defect position is highly cleaned with alcohol. The macroscopic visual observation shows that the defect is linear strip with irregular outline, the boundary is slightly darker than the casting body, and the center of the defect is black hole and non compact. Mechanical sampling method was used to sample the position, and then the microstructure of defects was observed under scanning electron microscope (SEM), as shown in Fig. 1.
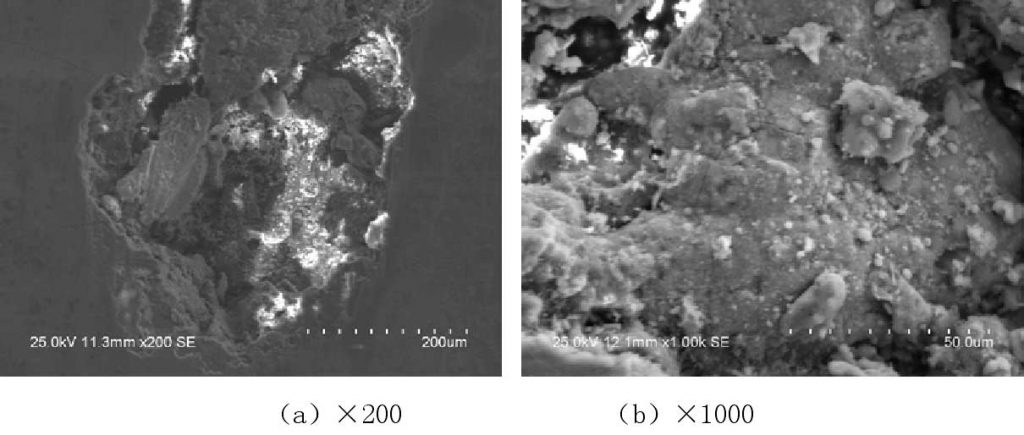
According to the defect morphology, the defects are flocculent, and some parts are rough holes on the surface. The defects are not firmly combined with the casting, and some of them fall off. After falling, they are irregular holes or cracks. There are obvious color differences between all defect positions and the surrounding casting body, and a few defect boundary positions have bright suspected metallic luster color, and show obvious dendrite shape in the process of metal solidification.
For further accurate qualitative analysis of the defect, EDS component analysis was carried out on the position. The analysis results are shown in Fig. 2.
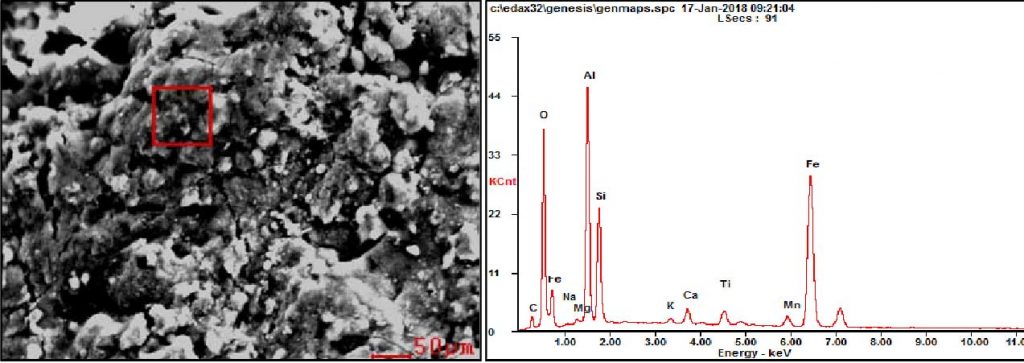
The detection results of the proportion of elements are consistent with the theoretical analysis. The results show that the content of C, O, Al and Si elements in the defect position is relatively high. It can be concluded that the main defects are metal oxides SiO2, MgO and Al2O3. Meanwhile, the bright position in the morphology observation is mainly caused by the composition segregation during inoculation and spheroidization. Because the magnetic properties of the elements and oxides are different from those of the casting body, the accumulation of magnetic marks is formed.