Non-destructive testing (NDT) methods are invaluable tools in the casting industry, used to detect and evaluate defects in materials without causing damage to the inspected parts. This article explores some commonly used NDT methods in detecting casting defects.
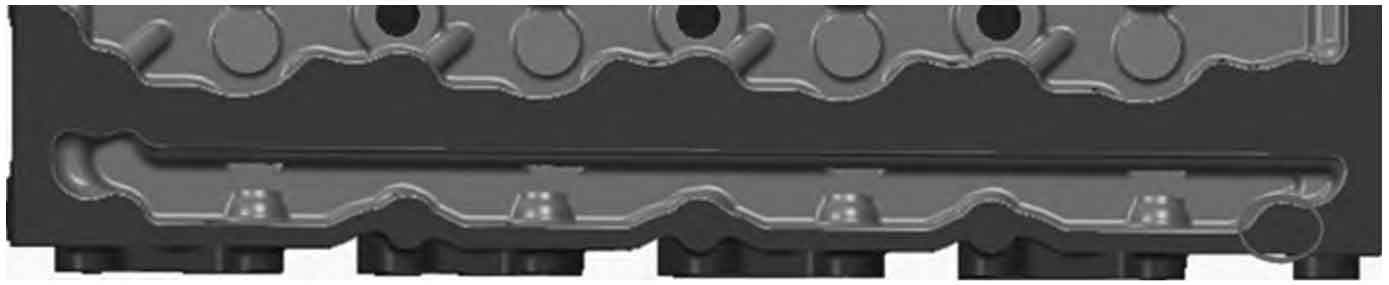
- Visual Inspection: Visual inspection is the simplest form of NDT and involves looking at the casting to identify any visible defects such as cracks, porosity, and misruns. This method often involves the use of magnifying glasses, mirrors, or borescopes to inspect hard-to-see areas.
- Radiographic Testing (RT): Radiographic testing uses X-rays or gamma rays to examine the internal structure of a casting. The radiation penetrates the casting and creates an image on a detector, showing the internal features of the part. Variations in material density, such as those caused by voids or inclusions, appear as contrast variations on the radiograph.
- Ultrasonic Testing (UT): Ultrasonic testing uses high-frequency sound waves to detect internal and surface defects. The sound waves travel through the casting and are reflected back when they hit a defect. The reflected wave is then detected and analyzed to determine the location and size of the defect.
- Magnetic Particle Testing (MT): This method is used for detecting surface and near-surface defects in ferromagnetic materials. The part is magnetized, and then iron particles are applied to it. If a surface or near-surface defect is present, the magnetic field will be distorted, causing the particles to accumulate at the defect location.
- Dye Penetrant Testing (PT): Dye penetrant testing is used for finding surface-breaking defects. The casting is coated with a visible or fluorescent dye solution. After a pre-determined time, the excess dye is removed, and a developer is applied that draws out the dye from any defects, making them visible.
- Eddy Current Testing (ET): Eddy current testing uses electromagnetic fields to detect surface and near-surface defects in conductive materials. The presence of a defect alters the path of the eddy currents, which can be detected and measured.
Non-destructive testing methods are essential tools in maintaining the quality of castings. By using these methods, foundries can detect casting defects early in the production process, allowing for timely corrective actions and preventing costly rework or failures in service. Each NDT method has its strengths and suitable applications, and often multiple methods are used in combination to ensure comprehensive inspection.