Abstract
Aluminum alloy castings are widely used in various industries due to their lightweight and corrosion resistance. However, these castings are prone to porosity and shrinkage defects, particularly during the investment casting process. Traditional methods based on empirical knowledge often lead to prolonged development cycles and increased production costs. To address these issues, this study utilized ProCAST software to optimize the investment casting process of an aluminum alloy shell component. The results indicate that the initial casting design suffered from porosity defects in two specific locations. Following optimization, the simulated and experimental results concurred, with no defects observed in the optimized casting, thereby satisfying product quality requirements.
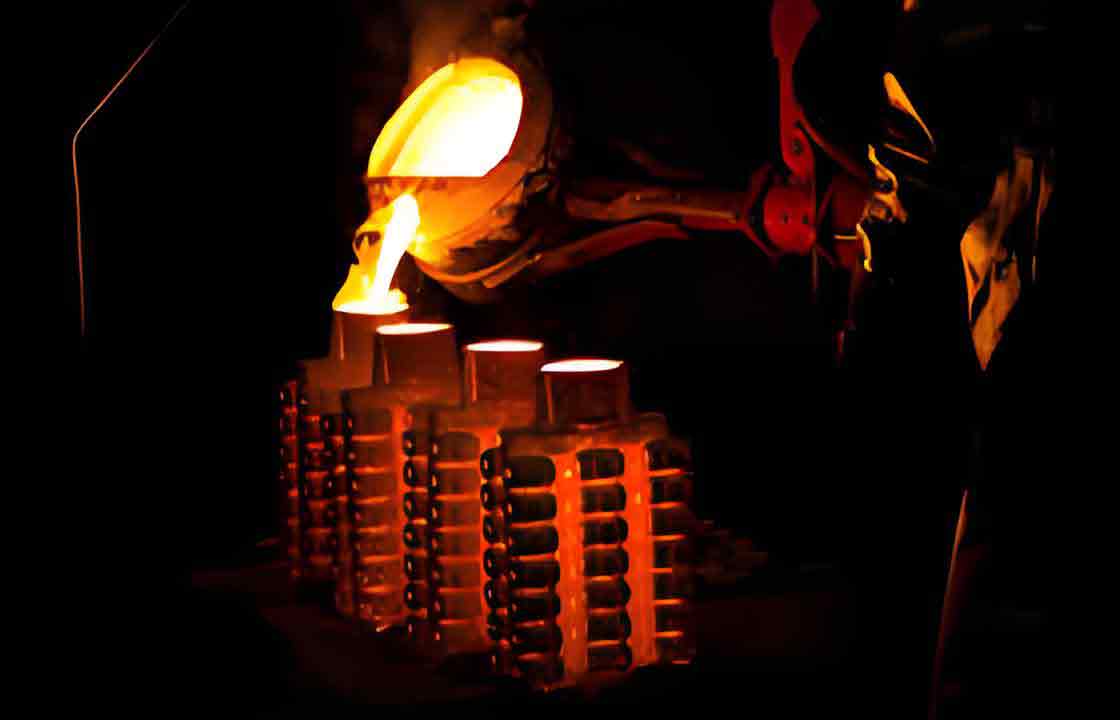
1. Introduction
Investment casting, also known as lost-wax casting, is a near-net shape manufacturing technique used to produce complex and intricate metal parts with high dimensional accuracy and surface finish. This process is particularly suited for aluminum alloy castings due to their low melting points and good fluidity. However, achieving defect-free castings, especially for components with strict metallurgical quality requirements such as the shell component studied herein, remains challenge.
Porosity and shrinkage defects are common issues encountered in aluminum alloy castings. These defects can significantly compromise the mechanical properties and functionality of the castings. Traditional methods of designing the gating system rely heavily on empirical knowledge, which is time-consuming and expensive. Therefore, there is a need to adopt more efficient and cost-effective approaches for optimizing the casting process.
This study focuses on the numerical simulation and optimization of the investment casting process for an aluminum alloy shell component using ProCAST software. The software’s ability to predict casting defects such as porosity and shrinkage enables the development of an optimized casting process that minimizes defects and ensures product quality.
2. Material and Methods
2.1 Material
The aluminum alloy used in this study is ZL101A, a commonly used aluminum-silicon alloy known for its good castability and mechanical properties. The alloy’s chemical composition and mechanical properties are tailored to meet the specific requirements of the shell component.
2.2 Methodology
The investment casting process involves several steps, including wax pattern creation, shell building, dewaxing, and pouring of molten metal. The key to achieving a defect-free casting lies in the design of the gating system and the control of casting parameters such as pouring temperature and mold cooling conditions.
2.2.1 Initial Process Design
The initial casting process was designed based on traditional empirical methods. A gating system was devised to ensure sufficient metal supply during the casting process and to facilitate the escape of gases and slag. The wax pattern was created using a 3D CAD model, and a ceramic shell was built around it using a plaster-based slurry.
2.2.2 Numerical Simulation
ProCAST software was used to simulate the filling and solidification behavior of the aluminum alloy during the casting process. The software provides detailed insights into the flow of molten metal, temperature distribution, and solidification kinetics.
The simulation model included the wax pattern, ceramic shell, and pouring system. The simulation parameters, including pouring temperature, pouring rate, and interface heat transfer coefficient, were set according to the material properties and process conditions. The solidification process was simulated to identify potential defect zones.
2.2.3 Process Optimization
Based on the simulation results, the initial casting process was optimized to eliminate the identified defects. Adjustments were made to the gating system, including the placement and size of risers and gates. The optimized design aimed to improve metal flow and ensure complete filling of the mold cavity, while facilitating proper solidification and reducing the likelihood of porosity and shrinkage defects.
2.2.4 Experimental Validation
To verify the simulation results and evaluate the effectiveness of the optimized process, castings were produced using both the initial and optimized process designs. The castings were subjected to non-destructive testing methods, such as X-ray radiography, to detect any defects. Additionally, microstructural analysis was performed to evaluate the quality of the castings.
3. Numerical Simulation Results
3.1 Initial Process Simulation
The initial casting process simulation revealed the presence of porosity defects in two specific locations within the casting . These defects were attributed to inadequate metal supply during solidification, resulting in the formation of isolated liquid regions within the casting.
3.2 Optimization Simulation
The optimized casting process design included modifications to the gating system, particularly the placement and size of risers and gates. The simulation of the optimized process showed no porosity defects, indicating that the changes made to the gating system effectively addressed the issues identified in the initial process.
Table 1: Comparison of Initial and Optimized Process Parameters
Parameter | Initial Process | Optimized Process |
---|---|---|
Pouring Temperature (°C) | 710 | 710 |
Pouring Rate (kg/s) | 0.2 | 0.2 |
Interface Heat Transfer Coefficient (W/m²·K) | 200 | 200 |
Riser Location | Original | Modified |
Riser Size (mm) | – | Increased |
Gate Size (mm) | Standard | Adjusted |
4. Experimental Results
4.1 Initial Process Casting
The initial casting process resulted in the production of castings with porosity defects in the predicted locations. Non-destructive testing confirmed the presence of defects, which were consistent with the simulation results.
4.2 Optimized Process Casting
In contrast, the optimized casting process yielded defect-free castings. Non-destructive testing and microstructural analysis confirmed the absence of porosity and shrinkage defects, verifying the effectiveness of the optimized process design.
5. Discussion
The successful optimization of the investment casting process for the aluminum alloy shell component demonstrates the value of numerical simulation in predicting and eliminating casting defects. By leveraging ProCAST software, it was possible to identify the sources of porosity defects in the initial process design and implement targeted modifications to the gating system.
The placement and size of risers and gates played a crucial role in the optimization process. By strategically positioning risers closer to potential defect zones and increasing their size, it was possible to ensure adequate metal supply during solidification and prevent the formation of isolated liquid regions.
The experimental validation of the optimized process design provided confirmation of the simulation results and underscored the reliability of the numerical approach. The defect-free castings produced using the optimized process met the strict quality requirements of the shell component, demonstrating the potential for widespread application of this methodology in the casting industry.
6. Conclusion
This study demonstrates the effectiveness of numerical simulation in optimizing the investment casting process for an aluminum alloy shell component. By utilizing ProCAST software, it was possible to identify and eliminate porosity defects in the initial casting process design. The optimized process design, which included strategic modifications to the gating system, yielded defect-free castings that met product quality requirements.
The results of this study have important implications for the casting industry, where traditional empirical methods of casting process design often lead to prolonged development cycles and increased production costs. By adopting numerical simulation techniques, it is possible to streamline the casting process design process, reduce defect rates, and improve product quality.