1.Casting system model of double hydraulic valve body
The design method of the valve body gating system is similar to that of a hydraulic valve body. The gating system uses two internal sprues to introduce the liquid metal into the casting cavity. Finally, it is calculated that the cross-sectional area of the internal sprue is 11cm2, with a length of 7.4CM, the cross-sectional area of Aru is 13.44cm2, with a length of 30cm, and the cross-sectional area of as is 15.68cm2, with a height of H, with a straightness of 22cm. The hydraulic valve body casting system model is shown in the figure.
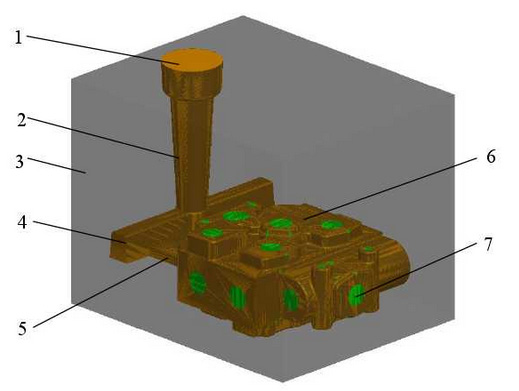
2.Grid generation and calculation conditions
The mesh generation method is the same as the previous one. During the mesh generation, the casting mesh is divided in detail, and the mesh of other parts is divided sparsely. The final mesh generation unit is 5.67 million, and the mesh generation result is shown in the figure.
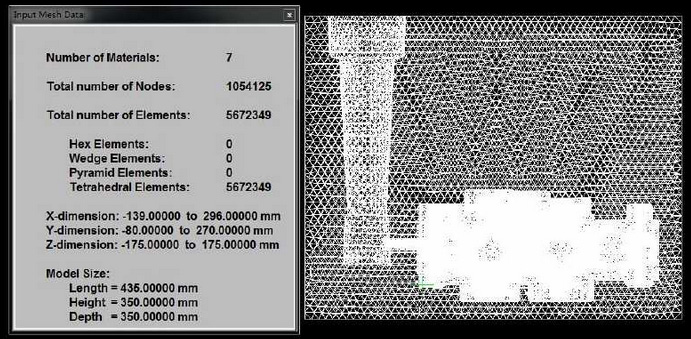
When the casting material is nodular cast iron, the casting defect volume of the casting is small, so the casting material is set as nodular cast iron QT500-7; and when the pouring temperature is 1360 ℃, the porosity of the casting is small, so the pouring temperature is set as 1360 ℃; the pouring time is 9.2s.
The casting mold and sand core material is silicon sand, the density is 1520kg / m3, the pouring temperature is 1360 ℃, and the pouring time is 9.2s. The material of mold and sand core is silicon sand with density of 1520kg / m3, 3 and initial temperature of 25 ℃. The heat transfer coefficient between the casting and the sand core and the mold is 500W / (M2 · K), and the heat transfer coefficient between the mold and the sand core is 200W / (M2 · K). The heat transfer boundary condition is set to air cooling.