The gravity top-pouring casting process is selected. Due to the complex internal structure of the turbine guide casting, hot spots are easy to occur at the wall thickness position, resulting in shrinkage defects in the investment casting of the turbine guide, and the thin-wall position of the investment casting of the turbine guide will hinder the flow of liquid metal, resulting in some parts of the investment casting of the turbine guide cannot be supplemented during solidification. According to the defects of the top-pouring casting system, The riser is reasonably set at the corresponding hot spot. Finally, through the analysis of the temperature field during the filling process and solidification process, the gating system is sufficient to feed the molding casting, which improves the qualification rate and molding quality of the turbine guide investment casting.
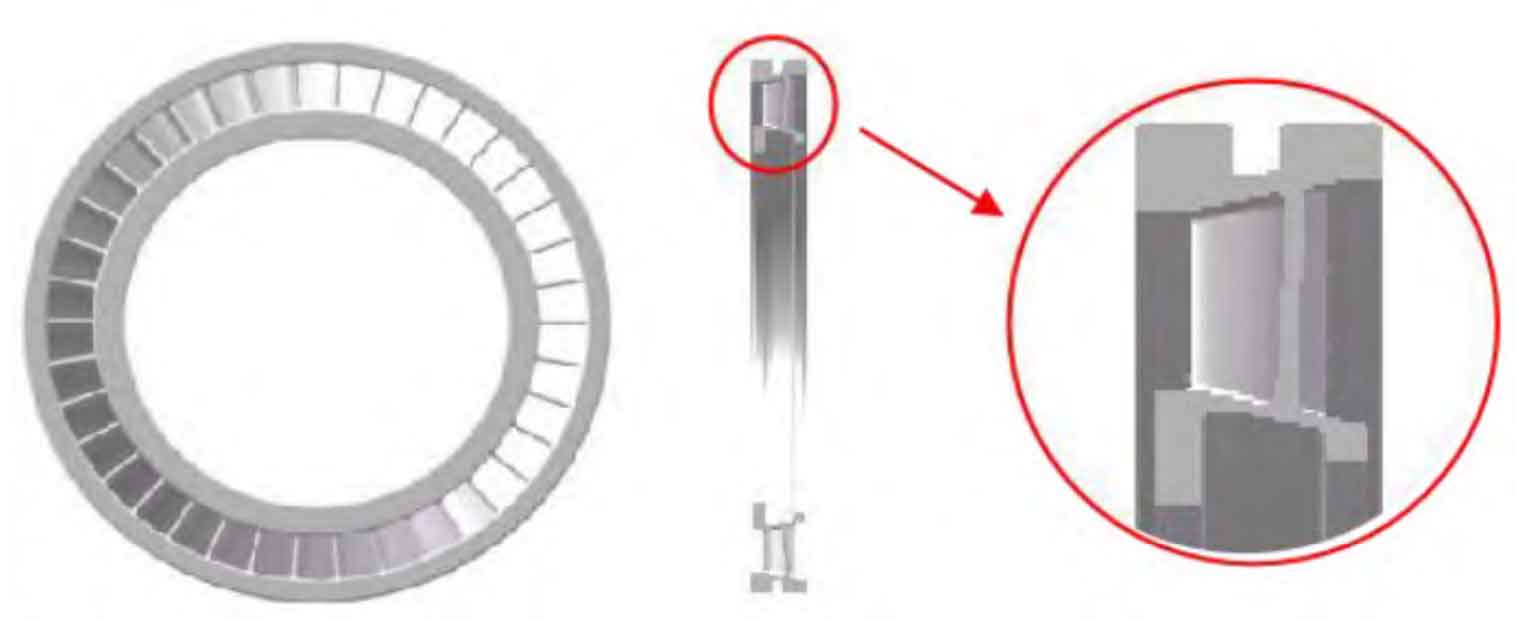
By using the finite element simulation software and analyzing the temperature field of the investment casting of the turbine guide, the mold filling and solidification status of the melt can be mastered. Through the analysis of the shrinkage porosity and shrinkage cavity of the investment casting of the turbine guide and the change of the solid fraction, the location and cause of the defects of the investment casting of the turbine guide can be predicted, and the solidification sequence of the investment casting of the turbine guide can be improved by setting insulating cotton at the pouring system, and the defects of the investment casting of the turbine guide can be eliminated, so as to obtain the products that meet the requirements. The optimized process plan was adopted for trial production, and the X-ray flaw detector was used for X-ray nondestructive testing of the formed complete casting. There were no holes or loose defects in the investment casting of the turbine guide, and the internal metallurgical quality met the casting standard.