Using ProCAST software to numerically simulate the precision casting process of turbine guide vanes, deeply analyze the potential risks and shortcomings of the filling and solidification processes, as well as the reasons for the formation of shrinkage porosity and porosity defects in precision castings. By adjusting the pouring method and the shape of the gate cup, optimizing the size and quantity of risers, and adding iron sand, optimization and simulation iterations are carried out to obtain a more reasonable precision casting process plan.
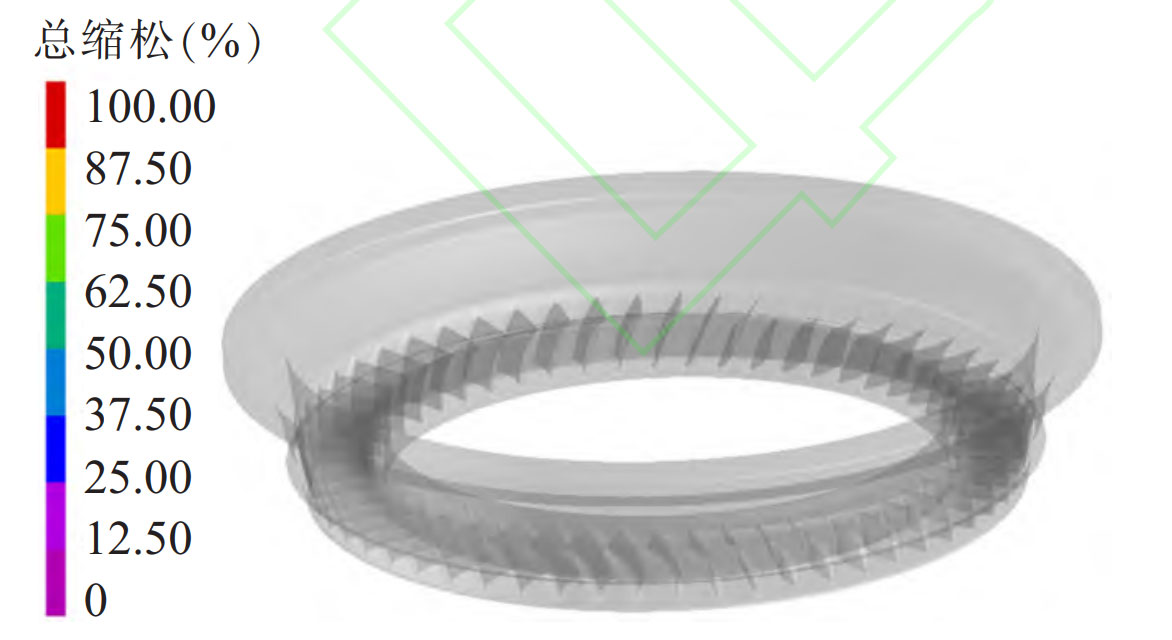
(1) Based on the concept of excellent metallurgical quality and engineering cost control, the optimization of the casting system for the precision casting process of the turbine guide was carried out. The mass of the optimized casting system was reduced by 42.98 kg compared to the initial process, and the metal utilization rate was as high as 43.18%, about 3.6 times that of the initial process.
(2) The first batch of trial production and small-scale production were carried out using the optimized precision casting process plan for the turbine guide. At the same time, all castings were tested according to the ASTME1742 radiographic inspection standard, and the results met the EMS52301/2 inspection specification, confirming the accuracy of numerical simulation results and analysis, as well as the feasibility of the process plan.