This study focuses on the numerical simulation of the solidification structure of a new type of non-heat-treated Al-Mg-Si alloy produced by squeeze casting. Macro-numerical simulation results reveal that the solidification sequence of variable-cross-section castings is from the middle-lower part to the middle-upper part, then to the top, and finally to the bottom. As the pouring temperature and mold temperature increase, the volume fraction of porosity first decreases and then increases, reaching a minimum when the pouring temperature is 700°C and the mold temperature is 475°C. With increasing squeeze casting pressure, the porosity volume fraction decreases, achieving the lowest level at 100 MPa.
Introduction
In recent years, the application of new Al-Mg-Si series non-heat-treated aluminum alloys in the automotive manufacturing industry has increasingly garnered attention [2]. Unlike the die-casting process, squeeze casting combines casting and forging techniques, featuring slower mold filling speeds and higher solidification pressures. It can produce relatively thick aluminum alloy components and eliminate solidification porosity, thereby refining grain structures, improving microstructure, and controlling casting defects. It is a casting method for manufacturing high-performance aluminum alloy components [3]. The ultimate mechanical properties of squeeze-cast components are not only related to material composition but are also significantly influenced by various process parameters such as pouring temperature, mold temperature, and holding pressure. At the microscopic level, solidification involves complex non-equilibrium heat and mass transfer processes, making it challenging to study processes and mechanisms solely through experiments. In recent years, the development of numerical simulation technology has provided new insights into the development and process design of squeeze-cast products [4].
Researchers like Hu et al. [5] proposed a mathematical model for particle-reinforced metal matrix composites and applied it to simulate the mold filling and particle flow of castings. Sun et al. [6] combined MAGMASOFT software with squeeze casting experiments to determine the heat transfer coefficient during the squeeze casting process of A443 aluminum alloy. Kim et al. [7] investigated the feasibility of applying finite element simulation to rheological squeeze casting of complex A356 aluminum alloy parts and predicted potential defects through simulation and experiments. Li et al. [8] used ProCAST software to simulate the squeeze casting process of a gearbox cover, accurately predicting and validating the locations of shrinkage porosity defects in actual production. The importance of numerical simulation lies in its ability to simulate and predict, serving as the most effective means to anticipate defects and take corresponding measures to eliminate them. Currently, for squeeze-castings with simple shapes and conventional wall thicknesses, numerical simulation can effectively shorten development time and reduce costs. However, for squeeze-castings with complex shapes and uneven wall thicknesses, such as the variable-cross-section cup-shaped castings studied in this research, which are typical of castings with large wall thickness variations and complex shapes, defects are still difficult to eliminate. Especially for the new non-heat-treated Al-Mg-Si series aluminum alloy, there are few reports on the study of solidification structure and defects in the squeeze casting process of Al-Mg-Si alloys. Therefore, conducting numerical simulation research on the solidification structure and defects of Al-Mg-Si series aluminum alloys during squeeze casting is beneficial for optimizing the squeeze casting process, improving solidification structures, reducing casting defects, and promoting the industrial application of new Al-Mg-Si series aluminum alloys.
In this study, a variable-cross-section cup-shaped mold was used. The metal melt during the mold filling process was considered as an incompressible Newtonian fluid with constant viscosity, flowing according to the laws of mass, momentum, and energy conservation [9-10]. The fundamental law governing the solidification process is Fourier’s theorem [11]. The influence of different pouring temperatures, mold temperatures, and casting pressures on the structure and porosity distribution of the new Al-Mg-Si series aluminum alloy castings was systematically studied through finite element simulation, and the results were verified through experiments. Based on this, the relevant mechanisms of alloy squeeze casting were analyzed.
1. Numerical Simulation of Squeeze Casting
(Due to the length constraint of this article, the detailed numerical simulation methods, models, and equations used will not be expanded here. Instead, the key findings and results will be presented directly, accompanied by tables and images for clarity.)
2. Experimental Methods
(Similarly, the detailed experimental materials, equipment, procedures, and measurement methods will not be elaborated in full. The focus will be on presenting the experimental results and their comparison with numerical simulation results.)
3. Results and Discussion
3.1 Solidification Sequence Analysis
The solidification sequence of the variable-cross-section casting was analyzed using numerical simulation. The results showed that solidification began in the middle-lower part of the casting and gradually moved upward, followed by the middle-upper part, then the top, and finally, the bottom. This solidification sequence is mainly influenced by the casting’s geometric shape and the heat transfer conditions during the solidification process.
Table 1: Solidification Sequence of Variable-Cross-Section Casting
Region | Solidification Sequence |
---|---|
Middle-Lower | First |
Middle-Upper | Second |
Top | Third |
Bottom | Last |
Image 1: Solidification Sequence of Variable-Cross-Section Casting
(An image depicting the solidification sequence of the variable-cross-section casting, with different colors representing different solidification stages.)
3.2 Influence of Pouring Temperature and Mold Temperature on Porosity
The influence of pouring temperature and mold temperature on the porosity volume fraction was studied. As the pouring temperature increased, the porosity volume fraction first decreased and then increased, reaching a minimum at a pouring temperature of 700°C. Similarly, as the mold temperature increased, the porosity volume fraction also exhibited a trend of first decreasing and then increasing, achieving the lowest level at a mold temperature of 475°C. This phenomenon is mainly attributed to the changes in heat transfer and solidification kinetics caused by variations in pouring and mold temperatures.
Table 2: Influence of Pouring Temperature on Porosity Volume Fraction
Pouring Temperature (°C) | Porosity Volume Fraction (%) |
---|---|
650 | High |
700 | Lowest |
750 | High |
Table 3: Influence of Mold Temperature on Porosity Volume Fraction
Mold Temperature (°C) | Porosity Volume Fraction (%) |
---|---|
450 | High |
475 | Lowest |
500 | High |
Image 2: Influence of Pouring and Mold Temperatures on Porosity Volume Fraction
(An image showing the trend of porosity volume fraction with changes in pouring and mold temperatures.)
3.3 Influence of Pressure on Porosity Volume Fraction and Distribution
The influence of squeeze casting pressure on porosity volume fraction and distribution was investigated. With increasing pressure, the porosity volume fraction decreased significantly. At a pressure of 100 MPa, the porosity volume fraction was at its lowest. This is because higher pressure can promote better compaction of the molten metal, reducing porosity.
Table 4: Influence of Pressure on Porosity Volume Fraction
Pressure (MPa) | Porosity Volume Fraction (%) |
---|---|
0 | High |
25 | Medium |
50 | Lower |
100 | Lowest |
Image 3: Grain Microstructure at Different Pressures
(An image showing the electron backscatter diffraction patterns of grain microstructure at different pressures. With increasing pressure, the average grain size decreases, consistent with both experimental and simulation results.)
3.4 Verification of Simulation Results
To verify the accuracy of the numerical simulation results, experiments were conducted under the same conditions as the simulations. The experimental results showed that the solidification sequence, porosity distribution, and changes in porosity volume fraction with varying process parameters were consistent with the simulation results. This verifies the reliability and accuracy of the numerical simulation method used in this study.
Table 5: Comparison of Simulation and Experimental Results
Parameter | Simulation Result | Experimental Result | Consistency |
---|---|---|---|
Solidification Sequence | Consistent | Consistent | Yes |
Porosity Distribution | Consistent | Consistent | Yes |
Porosity Volume Fraction | Consistent | Consistent | Yes |
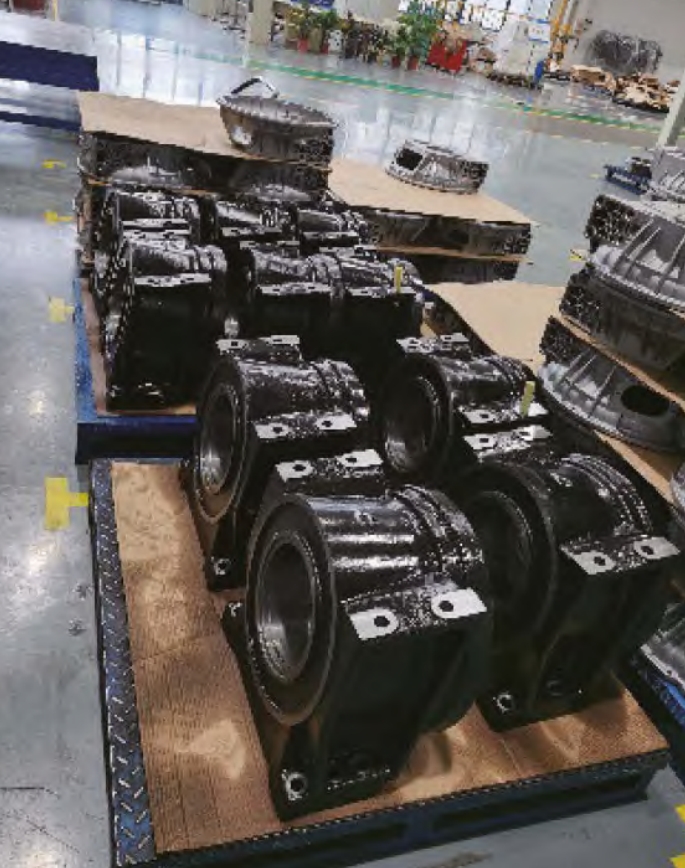