The wax mold is made with medium-temperature wax, the gating system scheme is the optimized investment casting process scheme for assembly welding, and the production mode of investment casting is adopted. The shell is made by the silica sol shell making process. The number of shell layers is 8 and a half, and the shell thickness is about 12 mm, which is consistent with the shell thickness set for the simulation software. After dewaxing, the mold shell is baked and poured in a vacuum consumable furnace. The temperature of the mold shell during pouring is about 40 ℃, which is consistent with the mold shell temperature of the simulation software. The pouring method is static pouring, and the material is ZTC4.
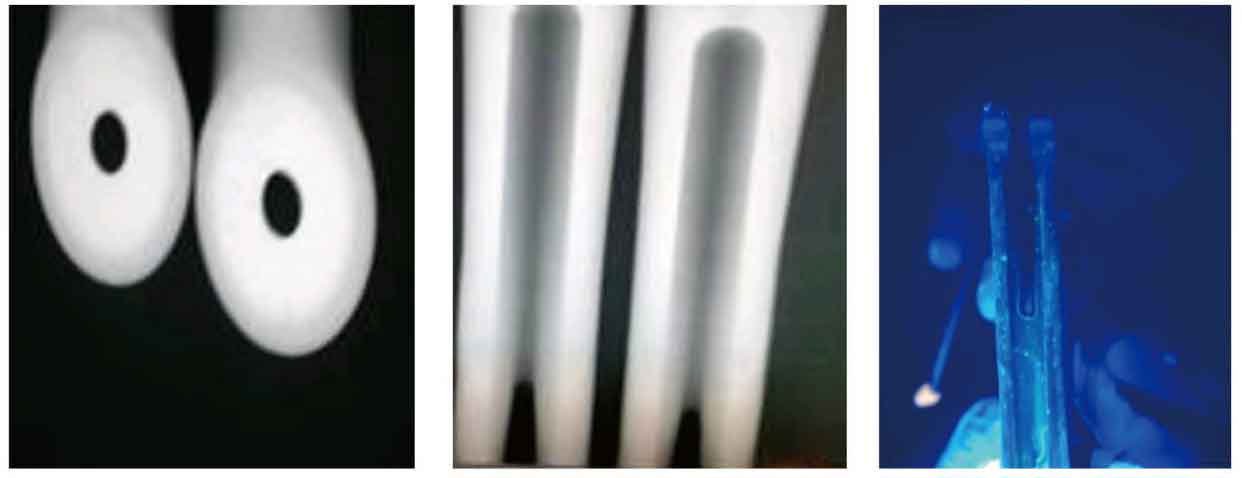
After the shell cleaning and repair of the investment casting, the hot isostatic pressure will not be carried out. The flaw detection will be carried out on the investment casting to check the internal quality. After the flaw detection, the fluorescent inspection will be carried out to check the condition of the fluorescent crack. The flaw detection and fluorescent results are shown in the figure. It can be seen from Figure (a) and Figure (b) that the end of the rod at the key part φ There are no investment casting defects at the 10mm position, and there are no shrinkage defects at the large wall thickness ratio of the rod opening. It can be seen from Fig. (c) that no surface micro-cracks are found in the investment casting through fluorescence inspection. The internal quality and appearance quality meet the customer’s requirements. The dimensional inspection of investment castings meets the tolerance requirements of GB/T 6414-2017 CT6.