According to the above theory, in order to meet the requirements of the sectional area of the sprue, it is necessary to optimize the connection mode between the sprue and the riser, and to change the sprue into a sheet shape to obtain a lower modulus, so as to promote the gate to solidify as soon as possible without affecting the riser feeding. According to the magma simulation and secondary test, it can be seen (Figure) that the lamellar connection is completely solidified within 60s, which cuts off the connection between the riser and the sprue. Finally, the riser forms a top shrinkage pipe after feeding, which maximizes the feeding effect of the riser.
After modifying the runner of the mold, the previous test parameters were repeated to pour 20 types of products, a total of 80 products. The top of the riser all formed shrinkage pipes, which proved that the feeding of the riser was successful. Through X-ray flaw detection of all castings, no shrinkage defects were found.
After the completion of the mold manufacturing, the key features of the mold such as size, material, processing quality (surface finish), gating system design and other key features should be checked. If possible, the molding test should be arranged to check whether the mold has problems such as poor draft, box closing interference, core insertion interference, etc., and confirm whether the fit clearance of the mold meets the design requirements. After all the confirmation is correct, it can be formulated Pouring plan.
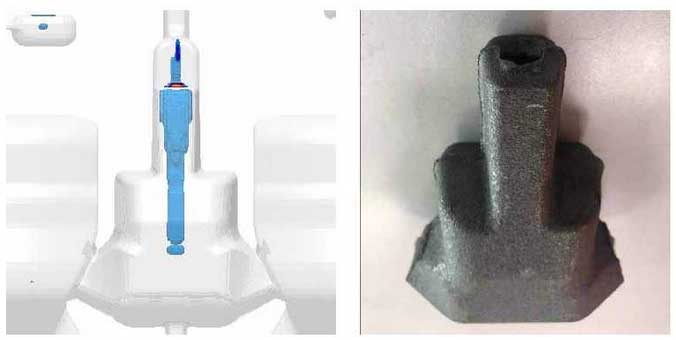
The selection of test parameters should be determined according to the acceptance standard of castings and the production experience of similar products. At the same time, individual parameters should be adjusted according to the guidance of magma simulation results. In the test plan, it is necessary to do limit test for key production parameters, grasp the products produced under different conditions for subsequent testing, including casting size, mechanical properties, internal defects and appearance, etc. in case of quality problems, it is necessary to analyze the types, distribution and causes of defects, and then obtain improvement measures, such as model size adjustment, mold process optimization or production parameter adjustment And repeated pouring verification was carried out until the castings with quality conforming to the specification could be obtained stably.