1. Cause analysis
According to the morphological analysis of the casting pore defects after dissection, it is mainly invasive pores, which is caused by the gas produced by the resin sand core after pouring can not be discharged in time, enter and remain in the molten iron, and there may also be some entrapped gas. Compared with the traditional dry cylinder block structure, this cylinder block has a new oil duct structure, that is, one more layer of sand core, the gas generation of sand core increases by 1.08 times, and the insufficient exhaust area is the main reason for the formation of invasive pores.
2. Process optimization
2.1 Optimization of sand core composition and exhaust scheme
(1) Replace the oil duct core sand
Change 50/100 mesh coated sand into 40/70 mesh Baozhu sand. On the one hand, raw sand with better sphericity is used to reduce the amount of binder, so that the gas evolution of core sand is reduced from 15.6 ml/g to 10.2 ml / g; On the other hand, the gap of spherical core sand particles increases, which accelerates the exhaust speed of sand core.
(2) Improve sand core exhaust design
① Design and manufacture the special core bone for oil duct sand core, which is connected with the exhaust needle (as shown in Figure 1), increase the exhaust channel, speed up the exhaust speed of oil duct sand core, and reduce pore defects.
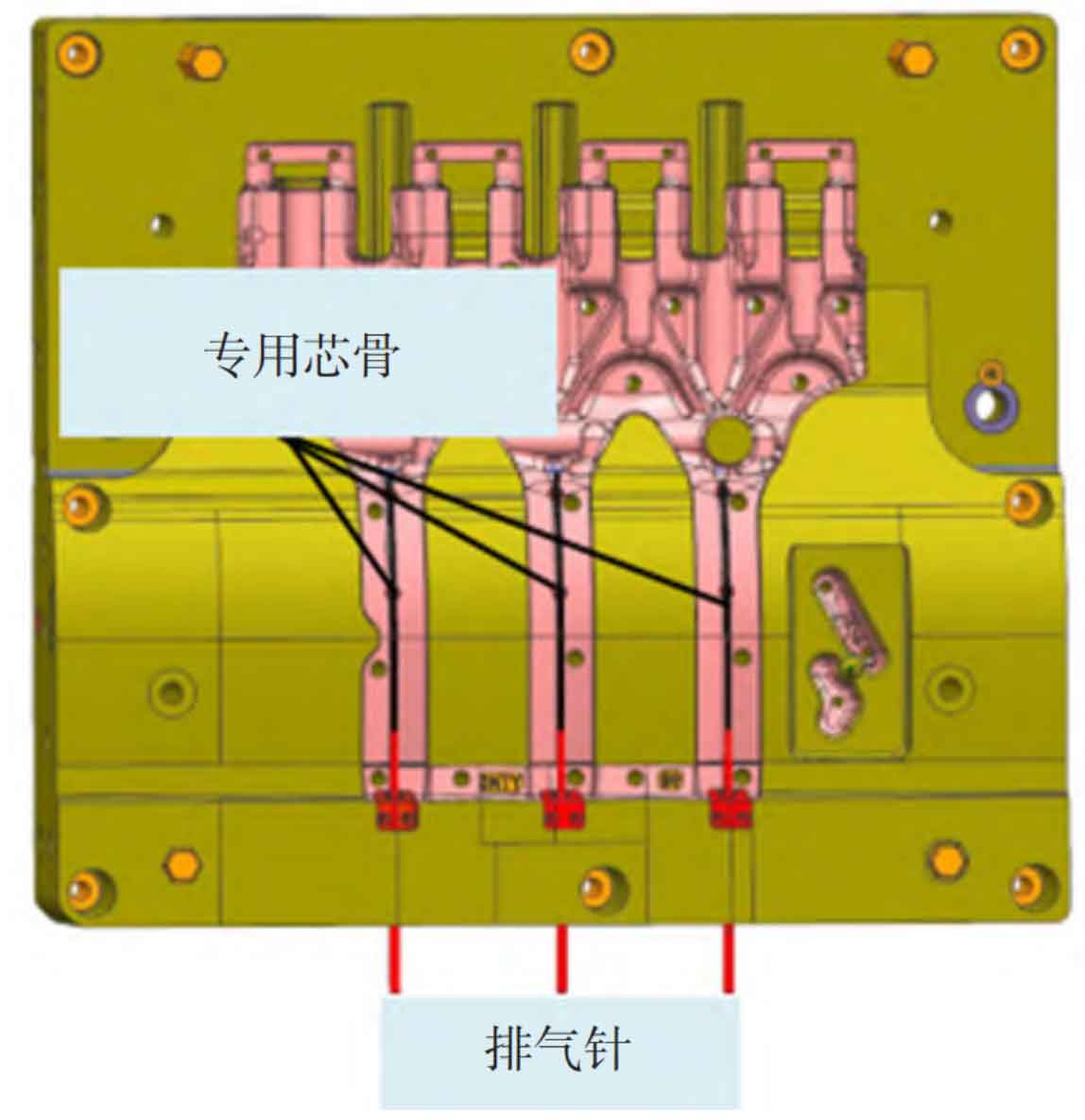
② Drill holes at the connecting parts of the main core and the oil duct sand core to ensure the smooth connection of the exhaust channel between the two cores and accelerate the exhaust of the oil duct core.
③ When lowering the core, add asbestos pad at the drilling part of the main core, and seal the fire to ensure that the oil duct and the exhaust channel of the main core are always kept unblocked with the outside world.
④ Increase the exhaust hole (as shown in Figure 2) at the matching place between the water jacket core and the side plate core to accelerate the exhaust.
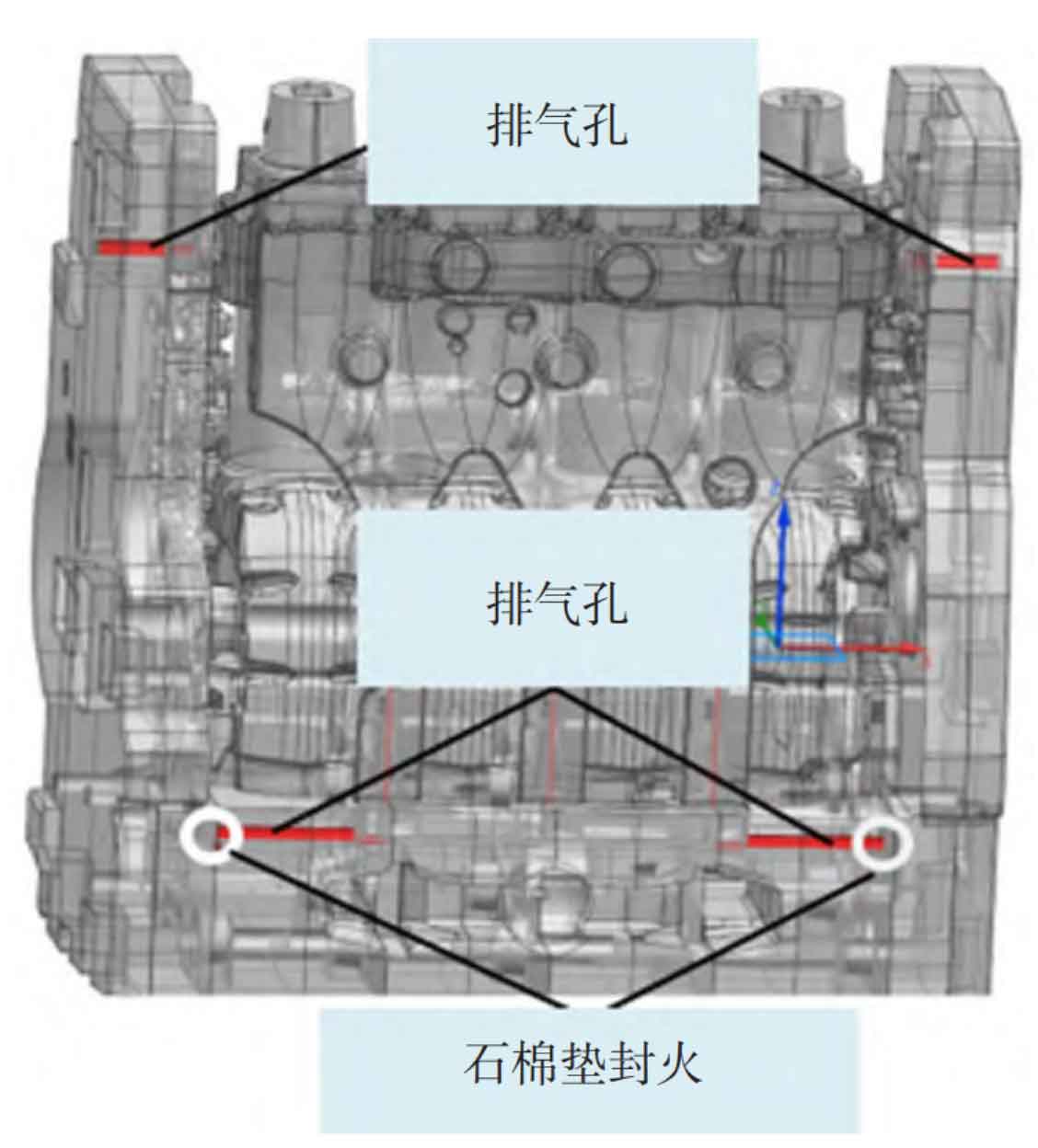
(3) Speed up the exhaust speed of the cavity, add air outlet pins and exhaust channels on the parting surface, and use the clearance of the parting surface to exhaust; An exhaust overflow riser is added at the highest point on both sides of the flange on the bottom of the cylinder block to make the molten iron entering the cavity in advance flow into the riser, improve the temperature of molten iron in the upper box and reduce the tendency of pores; Increase the number of gas outlet boreholes from 25 to 37, and the exhaust area is 1.48 times larger than the original.
2.2 Optimization of gating system
(1) Increase the iron feeding area and increase the top pouring ingate, so that the upper box temperature is higher and the tendency of pores is reduced in the process of molten iron filling.
(2) Improve the sprue proportion and replace the original sprue proportion Σ F straight: Σ F horizontal: Σ In F =1.1:1.4:1 is changed to Σ F straight: Σ F horizontal: Σ F inside =1.5:2:1, to ensure that the transverse runner is full and play a better role in slag retaining.
(3) Increase the flow area of the filter. The original process uses two pieces with a size of 60 mm × 60 mm × 16 mm ceramic filter, with a size of 70 mm × 70 mm × For 16 mm filter, the overflow area is increased by 1.44 times, and the filter is changed from horizontal to vertical, so as to improve the problem of slow flow rate of molten iron caused by slag accumulation blocking the filter during pouring and ensure the mold filling speed.
2.3 Product structure optimization
After consultation with the product designer, using UG three-dimensional simulation assembly, there is no assembly part at the highest point of the arc surface above the oil passage, and two 20 mm wide stiffeners can be added to facilitate the design of the exhaust riser and increase the exhaust area of the cavity.
After the optimization of the process plan, a total of 45 castings in three batches were poured. The test results showed that by changing the raw sand used for core sand, improving the core assembly process and exhaust system, optimizing the pouring system, the air hole defects in the upper box were eliminated, and the yield of cylinder castings reached more than 95%. After subsequent machining, no air holes were found on the top lap of the upper box, and the effect was obvious.