This article focuses on the optimization of the high and low speed switching point in the high-pressure casting process of the transmission main housing. Through simulation and experimental research, the influence of different switching points on the filling process, microstructure and mechanical properties of the casting is analyzed. The results show that an appropriate switching point can effectively improve the quality of the casting, providing a reference for the actual production process.
1. Introduction
The transmission is an important component in the automotive industry, and the quality of its main housing directly affects the performance and reliability of the transmission. High-pressure casting is a commonly used manufacturing method for transmission housings. However, in the casting process, factors such as the flow of molten metal and the formation of pores can affect the quality of the casting. The high and low speed switching point of the injection process is an important parameter that can significantly influence these factors. By optimizing this parameter, it is possible to improve the filling process of the molten metal, reduce defects such as pores, and ultimately enhance the quality of the casting.
2. Casting Model and Material
2.1 Model of the Transmission Main Housing
The 9AT transmission main housing has a complex structure with a large number of gears and shifting mechanisms. The outer dimensions are approximately 470 mm×400 mm×400 mm, and the mass is about 12.6 kg. The average wall thickness is about 6 mm, with the thinnest part being about 4 mm and the thickest part about 30 mm. There are also many reinforcing ribs and oil pipes inside, which can cause stress concentration during the casting process and lead to problems such as deformation, pores, shrinkage porosity, and shrinkage holes.
2.2 Material Selection
ADC12 aluminum alloy is chosen for the casting of the transmission main housing. This alloy has the characteristics of low density, high specific strength, and high specific stiffness, which can meet the requirements of the main housing’s strength and stiffness. The chemical composition of ADC12 is shown in Table 1.
Element | Si | Fe | Cu | Mn | Mg | Cr | Ni | Zn | Pb | Sn | Ti | Al |
---|---|---|---|---|---|---|---|---|---|---|---|---|
Content | 9.6 – 12.0 | ≤1.3 | 1.5 – 3.5 | ≤0.5 | ≤0.3 | ≤0.05 | 0.55 | ≤1.0 | ≤0.2 | ≤0.2 | ≤0.3 | Remainder |
3. Casting Process and Scheme
3.1 Design of the Gating System
The gating system is designed according to the shape of the transmission main housing. The ingate is set on the side of the deep cavity to facilitate the filling of the deep cavity. A branch is also set on the right valve plate surface to fill the complex valve plate surface.
3.2 Determination of Process Parameters
Based on the casting process design manual and practical production experience, the initial temperature of the molten metal is set to 680 °C, the initial temperature of the mold is 200 °C, and the total mass is about 18.95 kg with a total projected area of 265327 mm². The injection pressure is selected as 80 MPa with a safety factor of 1.2. The clamping force is calculated to be about 25470 kN, so a Buhler CATAT305 type die-casting machine is selected with a clamping force of 30500 kN and a punch diameter of ϕ150 mm. The low-speed injection speed is 0.2 m/s, the high-speed injection speed is 3.5 m/s, and the total length of the barrel is 800 mm. For the high and low speed switching point, three positions are considered: 480 mm, 520 mm, and 560 mm, corresponding to different situations in the filling process.
4. Simulation Results and Analysis
4.1 Simulation of the Filling Process
The Flow – 3D software is used to simulate the filling process of the transmission main housing for the three different high and low speed switching points.
4.1.1 Scheme 1 (Switching Point at 480 mm)
In this case, when the molten metal enters the cavity, it does not converge smoothly and directly fills the cavity at a high speed. A significant jet flow appears at the front end of the molten metal (as shown in Figure 3b), which is prone to cause backflow and air entrapment. There is an obvious unfilled part in the left shallow cavity, and the gas that has not been discharged in time is wrapped by the molten metal, resulting in internal pore defects in the transmission main housing. The filling in the left side of the cavity is slow, and the air entrapment is relatively serious, which has a great impact on the quality of the casting.
4.1.2 Scheme 2 (Switching Point at 520 mm)
When the molten metal converges smoothly and the injection speed changes from low to high, the molten metal can fill the cavity smoothly. Compared with Scheme 1, the jet flow at the front end is significantly improved, and the air entrapment phenomenon on the left side is also improved. However, because the left side is a shallow cavity area and requires less molten metal for filling, when the molten metal starts to be injected at a high speed after smooth convergence, it first enters the left shallow cavity part, forming a small amount of jet flow, and a small amount of gas is wrapped in the left shallow cavity molten metal (as shown in Figure 4b).
4.1.3 Scheme 3 (Switching Point at 560 mm)
At this switching point, when the injection speed changes from low to high, due to the filling effect of the right branch on the right deep cavity, the molten metal can fill both the left shallow cavity area and the right deep cavity area simultaneously. The molten metal fills the cavity in a laminar flow manner. The jet flow generated during the entire filling process is small, and the filling is relatively uniform. There is no gas wrapping phenomenon in the left shallow cavity part. The filling process is stable, which is beneficial for discharging the gas in the cavity and reducing the occurrence of pore defects.
4.2 Analysis of Air Entrapment Probability
The air entrapment probability in different parts after the filling process of the three schemes is simulated. The results are shown in Figure 6. When the high and low speed switching point is 480 mm, the air entrapment probability in the left shallow cavity and at the end is about 30%, and in some parts it can reach 50%. When the switching point is 520 mm, the air entrapment in the left shallow cavity is significantly improved, and only in some end regions the air entrapment probability reaches 50%. When the switching point is 560 mm, the overall air entrapment probability is the smallest. The air entrapment probability in the left shallow cavity area is lower than 13%, and in some end regions it is lower than 30%. Compared with Scheme 1 and Scheme 2, Scheme 3 has the most stable filling process and the smallest air entrapment probability.
5. Microstructure and Mechanical Properties
5.1 Microstructure of the Casting
The microstructure of the 9AT transmission main housing is observed. The shell structure is mainly composed of α – Al and α – Al + Si eutectic phases. The primary α – Al phase partly presents a dendritic morphology and partly a spherical or granular morphology. The eutectic Si exists in a needle – like shape. At the same time, there are a small number of blocky precipitates in the matrix. Due to the faster cooling speed at the end, the primary α – Al and eutectic Si cannot continue to grow, and a large number of primary α – Al grains are spherical. The microstructure of the 9AT main housing is relatively dense, with fine grains and uniform distribution.
5.2 Mechanical Properties of the Casting
The tensile strength and elongation of the near – gate and end positions of the actual production transmission main housing are analyzed. The results are shown in Table 3. The tensile strength and elongation at the near – gate are 272.0 MPa and 3.4% respectively, and at the end are 230.6 MPa and 2.7% respectively. The mechanical property requirements for the transmission main housing are a tensile strength of 190 MPa and an elongation greater than 1%. It can be seen that the mechanical properties of the transmission main housing produced by Scheme 3 meet the requirements.
Sampling Location | Tensile Strength/MPa | Elongation/% |
---|---|---|
Near – gate | 272.0 | 3.4 |
End | 230.6 | 2.7 |
6. Conclusion
6.1 Optimization of the Switching Point
Through the simulation of the filling process, it is found that when the high and low speed switching point is 560 mm, the entire filling process is stable and uniform, and the air entrapment probability is the smallest compared with when the switching points are 480 mm and 520 mm.
6.2 Verification of the Process
By selecting a low – speed injection value of 0.2 m/s, a high – speed injection value of 3.5 m/s, and a high and low speed switching point of 560 mm for actual production trials, the trial – produced transmission main housing has no obvious external defects, and the internal structure has fine grains, uniform distribution, and dense organization. The tensile strength and elongation at the near – gate are 272.0 MPa and 3.4% respectively, and at the end are 230.6 MPa and 2.7% respectively, all of which meet the mechanical property requirements of the transmission main housing. This research provides a valuable reference for the optimization of the high – pressure casting process of the transmission main housing.
7. Simulation and Analysis of the Filling Process
- Simulation Software and Methods
- The Flow – 3D software is used to simulate the filling process of the transmission main housing for the three different high and low speed switching points. This software can accurately model the flow of molten metal and predict the formation of defects during the casting process.
- Analysis of Different Switching Points
- Scheme 1 (Switching Point at 480 mm)
- In this case, when the molten metal enters the cavity, it does not converge smoothly and directly fills the cavity at a high speed. A significant jet flow appears at the front end of the molten metal (as shown in Figure 3b), which is prone to cause backflow and air entrapment. There is an obvious unfilled part in the left shallow cavity, and the gas that has not been discharged in time is wrapped by the molten metal, resulting in internal pore defects in the transmission main housing. The filling in the left side of the cavity is slow, and the air entrapment is relatively serious, which has a great impact on the quality of the casting.
- Scheme 2 (Switching Point at 520 mm)
- When the molten metal converges smoothly and the injection speed changes from low to high, the molten metal can fill the cavity smoothly. Compared with Scheme 1, the jet flow at the front end is significantly improved, and the air entrapment phenomenon on the left side is also improved. However, because the left side is a shallow cavity area and requires less molten metal for filling, when the molten metal starts to be injected at a high speed after smooth convergence, it first enters the left shallow cavity part, forming a small amount of jet flow, and a small amount of gas is wrapped in the left shallow cavity molten metal (as shown in Figure 4b).
- Scheme 3 (Switching Point at 560 mm)
- At this switching point, when the injection speed changes from low to high, due to the filling effect of the right branch on the right deep cavity, the molten metal can fill both the left shallow cavity area and the right deep cavity area simultaneously. The molten metal fills the cavity in a laminar flow manner. The jet flow generated during the entire filling process is small, and the filling is relatively uniform. There is no gas wrapping phenomenon in the left shallow cavity part. The filling process is stable, which is beneficial for discharging the gas in the cavity and reducing the occurrence of pore defects.
- Scheme 1 (Switching Point at 480 mm)
8. Analysis of Air Entrapment Probability
- Simulation Results
- The air entrapment probability in different parts after the filling process of the three schemes is simulated. The results are shown in Figure 6. When the high and low speed switching point is 480 mm, the air entrapment probability in the left shallow cavity and at the end is about 30%, and in some parts it can reach 50%. When the switching point is 520 mm, the air entrapment in the left shallow cavity is significantly improved, and only in some end regions the air entrapment probability reaches 50%. When the switching point is 560 mm, the overall air entrapment probability is the smallest. The air entrapment probability in the left shallow cavity area is lower than 13%, and in some end regions it is lower than 30%.
- Conclusion on Air Entrapment
- Compared with Scheme 1 and Scheme 2, Scheme 3 has the most stable filling process and the smallest air entrapment probability. This indicates that an appropriate high and low speed switching point can effectively reduce the air entrapment during the casting process, thereby improving the quality of the casting.
9. Microstructure and Mechanical Properties
- Microstructure Observation
- The microstructure of the 9AT transmission main housing is observed. The shell structure is mainly composed of α – Al and α – Al + Si eutectic phases. The primary α – Al phase partly presents a dendritic morphology and partly a spherical or granular morphology. The eutectic Si exists in a needle – like shape. At the same time, there are a small number of blocky precipitates in the matrix. Due to the faster cooling speed at the end, the primary α – Al and eutectic Si cannot continue to grow, and a large number of primary α – Al grains are spherical. The microstructure of the 9AT main housing is relatively dense, with fine grains and uniform distribution.
- Mechanical Property Testing
- The tensile strength and elongation of the near – gate and end positions of the actual production transmission main housing are analyzed. The results are shown in Table 3. The tensile strength and elongation at the near – gate are 272.0 MPa and 3.4% respectively, and at the end are 230.6 MPa and 2.7% respectively. The mechanical property requirements for the transmission main housing are a tensile strength of 190 MPa and an elongation greater than 1%. It can be seen that the mechanical properties of the transmission main housing produced by Scheme 3 meet the requirements.
10. Conclusion
- Optimal Switching Point Determination
- Through the simulation of the filling process, it is found that when the high and low speed switching point is 560 mm, the entire filling process is stable and uniform, and the air entrapment probability is the smallest compared with when the switching points are 480 mm and 520 mm.
- Process Verification and Significance
- By selecting a low – speed injection value of 0.2 m/s, a high – speed injection value of 3.5 m/s, and a high and low speed switching point of 560 mm for actual production trials, the trial – produced transmission main housing has no obvious external defects, and the internal structure has fine grains, uniform distribution, and dense organization. The tensile strength and elongation at the near – gate are 272.0 MPa and 3.4% respectively, and at the end are 230.6 MPa and 2.7% respectively, all of which meet the mechanical property requirements of the transmission main housing. This research provides a valuable reference for the optimization of the high – pressure casting process of the transmission main housing.
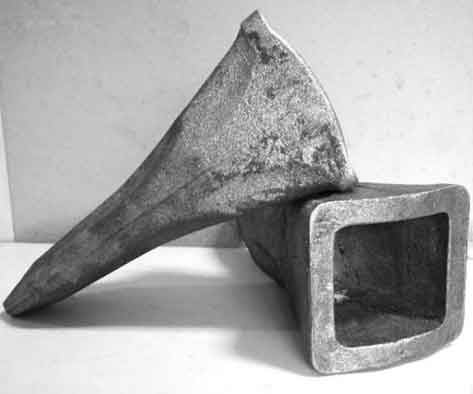