As an engineer at Changshu Tiandi Coal Machinery Equipment Co., Ltd., I have dedicated years to improving the casting process for critical mining components. The planetary carrier, a core output element in shearer gear transmission systems, endures extreme torque during coal mining operations. Its complex geometry, featuring slender triangular support columns between upper and lower plates, creates dispersed hot spots and obstructed feeding channels. This often leads to defects like shrinkage porosity, cracks, and inclusions in the original casting process, reducing product yield to below 80%. Such flaws cause premature failures under harsh underground conditions, risking safety and operational downtime. To address this, I spearheaded an optimization project using finite element simulation to refine the casting process, ensuring higher quality and reliability. This article details my approach, from defect analysis to successful implementation, emphasizing how iterative simulations and data-driven adjustments transformed casting outcomes.
The planetary carrier, made of ZG42CrMo steel, has a complex structure with uneven wall thicknesses. Key dimensions include an outer diameter of 694 mm, height of 697 mm, and nominal wall thicknesses ranging from 40 mm to 70 mm, with localized sections exceeding 200 mm. This geometry results in thermal imbalances during solidification. The material’s chemical composition and mechanical properties are strictly specified to withstand high-stress environments, as shown in Tables 1 and 2. In the original casting process, the gating system used top pouring with inadequate riser placement, causing premature solidification in the columns and blocking feeding paths. This led to internal defects, as confirmed through metallurgical analysis of scrapped parts.
C | Si | Mn | P | S | Cr | Mo |
---|---|---|---|---|---|---|
0.32-0.42 | 0.20-0.45 | 0.50-0.80 | ≤0.025 | ≤0.025 | 0.80-1.20 | 0.20-0.30 |
Ultimate Tensile Strength (MPa) | Yield Strength (MPa) | Elongation (%) | Reduction in Area (%) | Impact Toughness (J) |
---|---|---|---|---|
≥800 | ≥450 | ≥10 | ≥20 | ≥45 |
Defects in the initial casting process primarily arose from poor thermal management. The slender columns solidified faster than thicker sections, isolating hot spots and hindering riser feeding. Common issues included shrinkage porosity at column junctions and cracks due to thermal stresses. To quantify this, I analyzed defect distribution across 50 scrapped carriers, revealing that over 60% of failures originated from the support columns. The solidification time imbalance can be modeled using Chvorinov’s rule:
$$ t = k \left( \frac{V}{A} \right)^n $$
where \( t \) is solidification time, \( V \) is volume, \( A \) is surface area, \( k \) is a mold constant, and \( n \) is an exponent (typically 1.5–2 for steel). For the columns, the high \( A/V \) ratio accelerated cooling, causing \( t \) to fall below critical thresholds and triggering defects. This underscored the need for a redesigned casting process with enhanced feeding and thermal control.
Optimizing the casting process began with redefining key parameters and leveraging Proe software for 3D modeling. I set a uniform casting shrinkage rate of 2.0% based on historical data and component complexity. Machining allowances were standardized: 15 mm for upper surfaces, 10 mm for lower surfaces, 13 mm for sides, and 13 mm for bore holes. Wooden patterns were modified by removing old riser bases and adding new ones with 15–18 mm thick positioning plates and R30 mm fillets. For mold materials, resin sand was used for cores and molds, coated with zircon-based alcohol paint to prevent burn-on. Chromite sand was applied to high-risk areas to minimize sand adhesion.
Riser design was central to the new casting process. Using modulus calculations, I determined riser sizes to ensure adequate feeding. The modulus \( M_c \) for critical hot spots was derived from:
$$ M_c = \frac{V}{A} $$
where \( V \) is volume and \( A \) is cooling surface area. Riser modulus \( M_r \) was then set as \( M_r = 1.2 M_c \) to guarantee directional solidification toward risers. This resulted in four insulated blind risers and one open riser, strategically placed to cover all thermal zones. The gating system was switched to a bottom-up design with open channels using ceramic tubes to promote laminar flow and reduce turbulence. This minimized slag entrapment and improved feeding efficiency.
Finite element simulation with specialized software validated the casting process iteratively. I modeled heat transfer using Fourier’s law:
$$ q = -k \nabla T $$
where \( q \) is heat flux, \( k \) is thermal conductivity, and \( \nabla T \) is temperature gradient. Three schemes were tested, as summarized in Table 3. Scheme 1 used top pouring with modified risers but showed residual microporosity (14 shrinkage zones and 94 pores). Scheme 2 employed bottom gating, reducing macro-defects but increasing microporosity. Scheme 3 integrated optimized risers, external chills, and bottom gating, achieving near-zero defects. Chills enhanced cooling in thick sections, modeled by adjusting boundary conditions in simulations.
Scheme | Gating Type | Riser Configuration | Defects Identified | Key Improvements |
---|---|---|---|---|
1 | Top pouring | 4 blind risers | 14 shrinkage zones, 94 pores | Reduced macro-defects but high microporosity |
2 | Bottom gating | 4 blind risers + chills | Low macro-defects, high microporosity | Improved feeding but thermal imbalances |
3 (Optimized) | Bottom gating | 4 blind risers + 1 open riser + chills | Negligible defects | Balanced cooling, effective feeding |
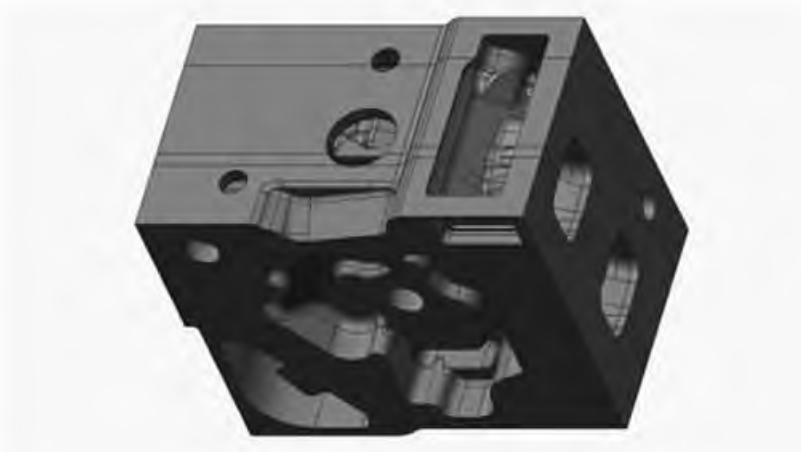
Implementing the optimized casting process involved producing 25 carriers across 10 batches. Defect analysis showed no macro-porosity or cracks except in one unit damaged during riser cutting. Non-destructive testing confirmed the absence of micro-defects, with components exhibiting dense, homogeneous microstructures. The refined casting process also enabled better heat treatment outcomes. Quenching was intensified using water-based media instead of oil, increasing hardness and case depth. This is expressed by the quench severity factor:
$$ H = \frac{h}{2k} $$
where \( h \) is heat transfer coefficient and \( k \) is thermal conductivity. Higher \( H \) values improved mechanical properties, as verified in post-treatment tests (Table 4). The optimized casting process boosted yield strength by 37% and impact toughness by 28%, exceeding standard requirements.
Ultimate Tensile Strength (MPa) | Yield Strength (MPa) | Elongation (%) | Reduction in Area (%) | Impact Toughness (J) |
---|---|---|---|---|
859 | 618 | 12.5 | 39.0 | 57.5 |
In conclusion, optimizing the shearer planetary carrier casting process through finite element simulation resolved critical defects and enhanced product quality. The new approach, featuring bottom gating, optimized risers, and chills, eliminated shrinkage and porosity by ensuring uniform solidification. This not only raised casting yield to 100% in defect-free units but also improved mechanical properties, extending component lifespan in demanding mining applications. The success underscores the value of simulation-driven refinements in industrial casting processes, offering a replicable framework for similar high-integrity castings.