A total of 25 planet carriers were produced in 10 batches by using the optimized casting process plan. Except for one piece with cracks on the cutting surface due to improper cutting riser, no macro defects such as porosity, shrinkage cavity and cracks were found on the remaining castings after rough machining, and all the castings were qualified. The casting has no obvious porosity, shrinkage cavity, crack and other micro defects through secondary NDT, as shown in the figure.
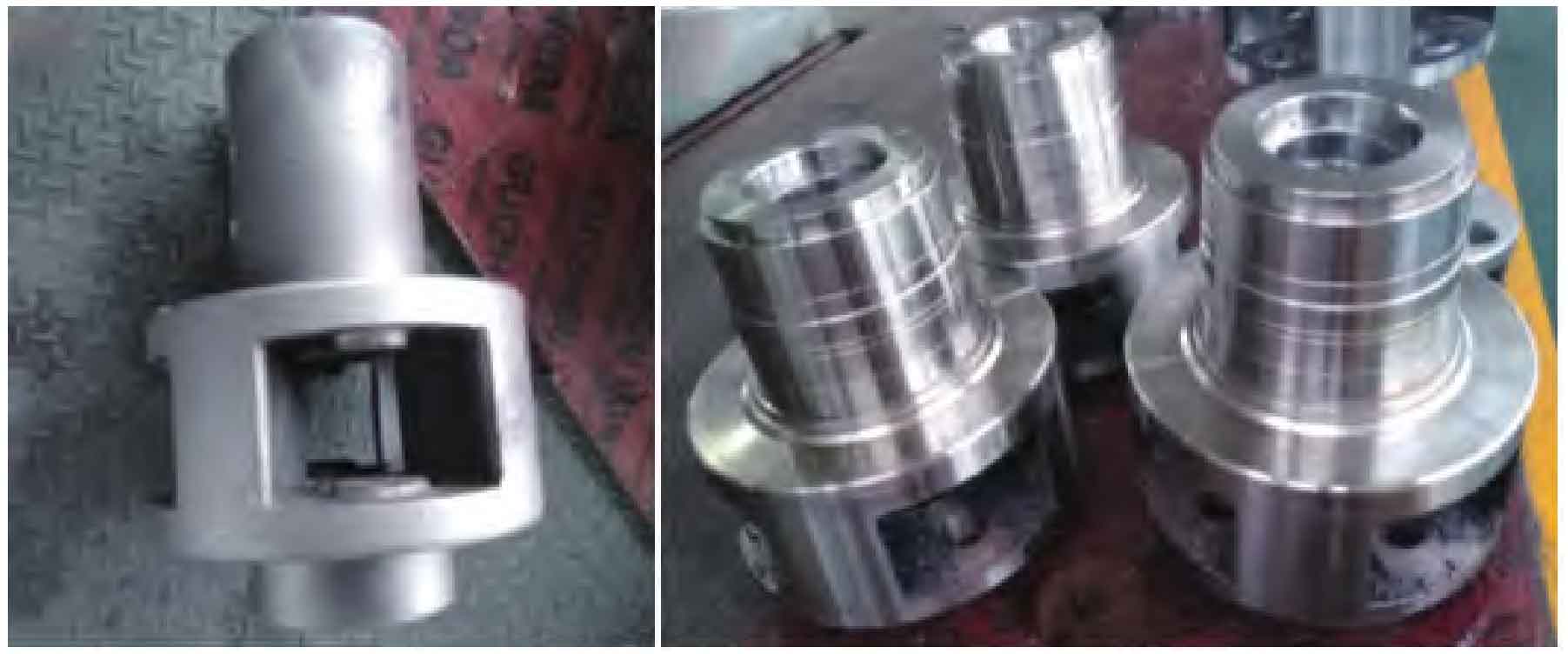
The overall quality of the planet carrier castings produced by the optimized process scheme has been improved, which can be verified by the obvious improvement of the mechanical properties of the initial state (normalized delivery of castings) of the castings. Due to the effective control of casting defects, the density of the casting increases and the microstructure improves, so the quality of the planet carrier heat treatment process is also guaranteed. The quenching and cooling in the quenching and tempering process is changed from the original oil-based quenching and cooling medium to a more intense water-based quenching and cooling medium, which increases the quenching hardness and effective hardening layer depth of the planet carrier, greatly improves the comprehensive mechanical properties of the planet carrier products, and meets the standard requirements. The mechanical property test results of the finished planetary carrier are shown in the table.
Rm/MPa | Rp0.2/MPa | A(%) | Z(%) | KU/J |
859 | 618 | 12.5 | 39.0 | 57.5 |
As the triangular support column between the two side plates of the shearer planetary frame is relatively long and thin, it blocks the metal flow in the solidification process, making this part prone to a large number of defects such as looseness and shrinkage cavity. The casting process of planet carrier was simulated by finite element software, and the original process was optimized. The optimized casting process not only solved the problems of porosity, shrinkage cavity and crack, but also ensured the stable casting quality, which met the design requirements of the drawing and was recognized and praised by customers. The new process shortens the processing cycle of the casting, reduces the production cost, improves the production efficiency, improves the service life of the casting, and has good economic value.