As the most important output component of the shearer gear transmission system, the planet carrier has a complex structure and bears a large torque during the operation of the shearer. Due to the harsh working environment, long working time and high strength of the shearer under the shaft, the planet carrier is prone to deformation, even fracture and other failures in the use process, leading to the shutdown of the shearer and even safety accidents. Therefore, the planet carrier must have excellent mechanical properties. The planet carrier is generally produced by casting process. First, the rough with structure and size close to the finished product is cast, and then the finished product meeting the requirements of structure and property is obtained through machining and heat treatment. Therefore, in order to ensure the safe operation of the shearer, the planet carrier needs to have high casting quality.
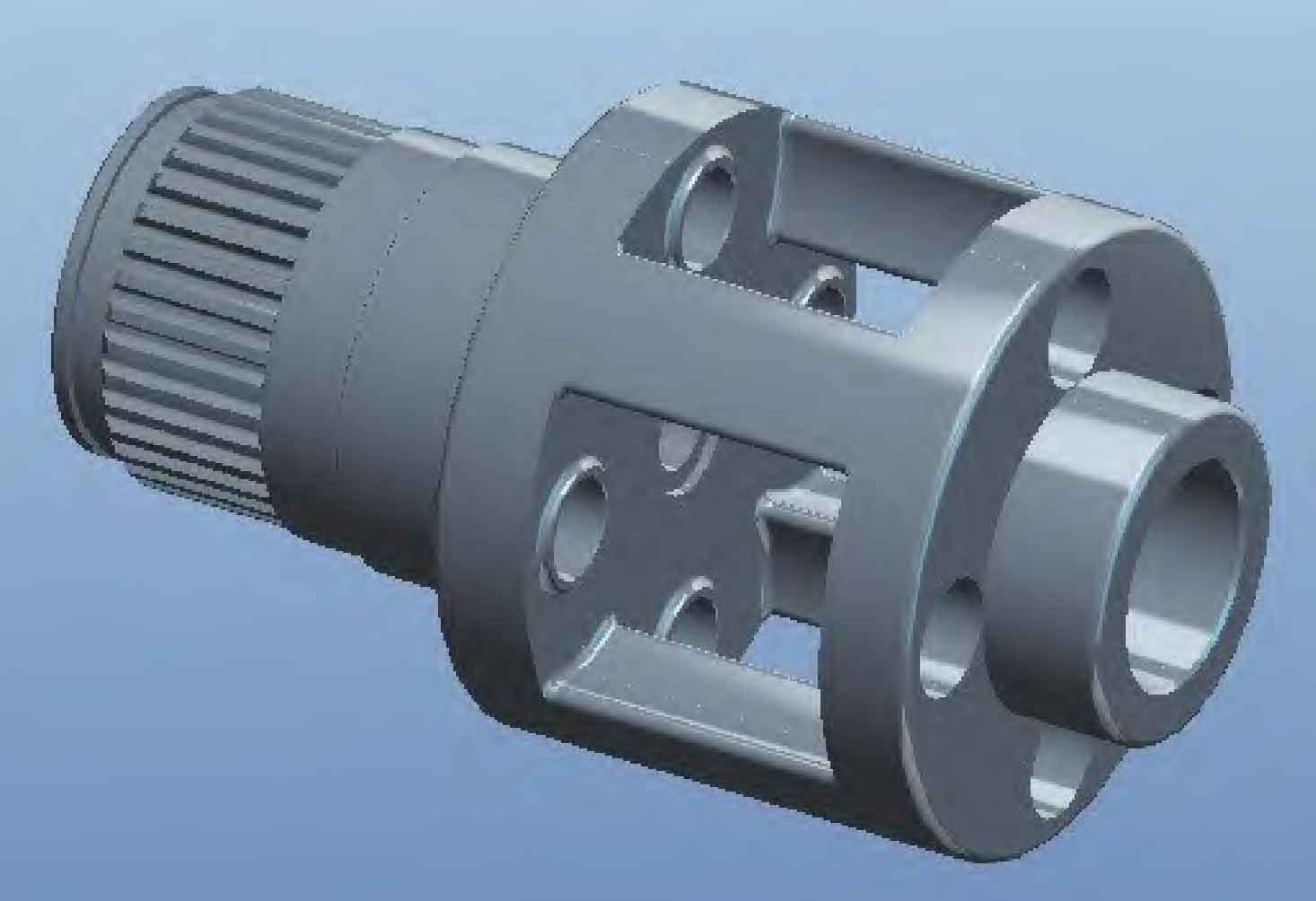
Figure shows the three-dimensional entity of the planet carrier of a certain type of shearer. The four triangular support columns between the upper and lower side plates of the planet carrier are relatively long and thin, with complex structure. They are easy to form hot spot dispersion during casting, which is not conducive to feeding. In addition, the feeding channel between each hot spot is not smooth, and casting defects such as looseness, shrinkage cavity, crack, slag inclusion and sand hole are easily produced. At present, the qualification rate of rough castings of shearer parts in our company is about 80%, while the qualification rate of rough castings of traveling star frame is lower. The casting quality of planet carrier has seriously restricted the high-quality development of enterprises. In order to solve this problem, the existing casting process must be improved to improve the casting quality of the planet carrier.
After years of development, finite element simulation has been widely used in casting production. Through finite element simulation, the causes of casting defects are clarified, which can provide theoretical guidance for process improvement. Finite element simulation has been widely used in improving the casting process of wind power and automobile planet carrier, and has achieved remarkable results. Therefore, this paper plans to use the finite element software to simulate the casting process of the shearer planet carrier, clarify the causes of the defects, and propose the process improvement method, and finally obtain the optimized casting process of the shearer planet carrier.